In meccanica l’operazione di alesatura è la finitura di un foro cilindrico, grezzo di fusione oppure già lavorato con trapano, consiste nell’ingrandirlo fino al diametro esatto, mediante asportazione di piccole quantità di soprametallo, eseguita a mano o a macchina. A seguito di questa generale definizione esiste una tipologia enorme di utensili alesatori.
Tralasciamo qui di parlare delle operazioni di finitura dei grandi fori finiti con operazioni di tornitura e di rettifica, caratteristici per esempio degli ingranaggi o dei particolari su cui vengono inseriti alberi di scorrimento.
Ci limitiamo qui a parlare degli alesatori a gambo con taglienti che possono essere in HSS o in metallo duro e che sono destinati a finire fori sgrossati con punte ad elica e semifiniti eventualmente con allargatori (figura 1 in apertura).
Gli alesatori in metallo duro, cioè con i taglienti in carburi sinterizzati, sono usati moltissimo nelle produzioni di grandi serie, dove è assolutamente necessario che i diametri ottenuti siano tutti entro tolleranze molto ristrette.
La caratteristica principale di questo materiale, come è noto, è l’elevata durezza che limita l’usura anche in tutte quelle lavorazioni dove il materiale lavorato rende difficile il processo di asportazione del truciolo.
Basta pensare ai fori presenti nelle parti di un motore per automobile, nella testa cilindri o nel basamento, rispettivamente in leghe di alluminio (molto abrasive) e in ghisa (molto dura e abrasiva), alla loro esigenza di precisione e di costanza dei diametri per garantire l’assoluta intercambiabilità dei pezzi.
Nella quasi totalità dei fori non è possibile usare altri sistemi di finitura se non l’alesatura.
Gli alesatori in metallo duro possono essere costruiti con placchette brasate sul corpo, con inserti staffati meccanicamente (per i diametri maggiori) oppure, fino a diametri intorno a 12 mm, integralmente in metallo duro.
La costruzione di alesatori integrali in metallo duro presenta il vantaggio, rispetto a quelli con placchetta brasata, che non hanno limitazioni nel numero di denti e nell’angolo dell’elica.
In genere si usa un metallo duro del gruppo K, in pratica quasi sempre un K10, che è il gruppo che ha la durezza maggiore e la più alta resistenza all’abrasione.
Questa categoria di carburi sinterizzati abbina all’alta durezza anche una maggior fragilità, ma, salvo casi del tutto particolari, un alesatore non subisce urti durante la lavorazione e quindi questa caratteristica negativa non ha alcun effetto sul rendimento.
Caratteristiche dimensionali
Le parti essenziali che caratterizzano un tipico alesatore sono:
- i taglienti (numero dei taglienti, elica, gola);
- l’imbocco;
- il quadretto e le spoglie dorsali;
- la spoglia anteriore.
Numero dei taglienti
Il numero dei taglienti varia in funzione del diametro e può essere da un minimo di 3 per diametri fino a 5 mm ad un massimo di 10 – 12, raramente di più per alesatori di grande diametro.
Normalmente un alesatore con un numero di taglienti dispari (ad esempio, 5 o 7) genera fori con minori errori di circolarità ed evitano imperfezioni dovute a vibrazioni.
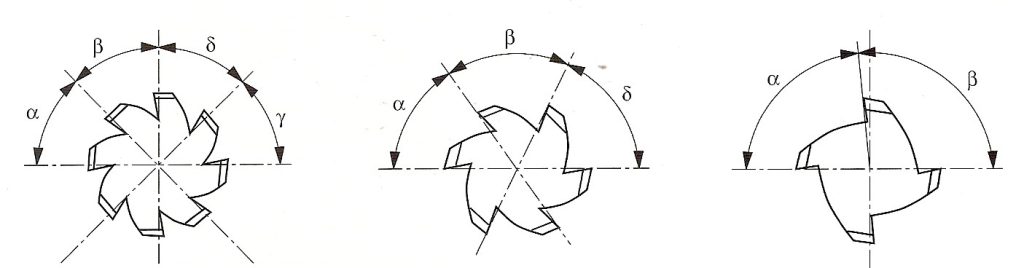
I taglienti possono essere dritti od elicoidali. I primi, di costruzione relativamente comoda, hanno la caratteristica di innescare facilmente vibrazioni, producendo difetti sulla superficie lavorata.
Per evitare questo inconveniente è molto utile dividere irregolarmente i taglienti, mantenendoli però accoppiati a due a due per consentire l’annullamento delle forze radiali. In questo modo inoltre si facilita anche la misura esatta del diametro dell’alesatore. Nella figura 2 è schematizzata la disposizione dei denti in questo caso.
Elica
Si è detto che gli alesatori possono essere a denti dritti o a denti elicoidali; questi ultimi si possono distinguere in due tipi:
- alesatori ad elica positiva, cioè con senso concorde al senso di taglio (elica destra-taglio destro; elica sinistra-taglio sinistro);
- alesatori ad elica negativa, cioè con senso discorde al senso di taglio (elica destra-taglio sinistro; elica sinistra-taglio destro).
L’elica positiva provoca l’espulsione dei trucioli in senso opposto alla direzione di avanzamento e quindi sono adatti alla lavorazione di fori ciechi.
Questo tipo di elica favorisce l’auto-penetrazione dell’alesatore e quindi può verificarsi che esso si pianti nel foro; se però l’avanzamento è regolare (comandi meccanici o CNC) tale inconveniente accade raramente.
L’elica negativa, chiamata anche elica discendente, invece spinge i trucioli nel senso dell’avanzamento e quindi è indicata nella lavorazione di fori passanti, ma ciò non impedisce che si possa adoperare anche per la finitura di fori ciechi dove non sia necessario finire tutto il foro. In questo caso evidentemente i trucioli si accumulano sul fondo del foro e quindi si dovrà prevedere una maggiorazione della profondità.
Con l’elica negativa l’alesatore tende a “rifiutare” il foro e perciò si ha una migliore finitura delle superfici.
La gola di scarico deve essere ampia e ben lucidata per permettere lo scorrimento libero dei trucioli. I raggi di raccordo devono essere i più ampi possibile e non devono dar luogo a spigoli che possono essere di ostacolo al libero avvolgimento dei trucioli.
In condizioni normali il valore dell’angolo dell’elica varia da 5° a 10°. Per ottenere buoni risultati nell’alesatura di fori interrotti, si usano talvolta alesatori a denti alternati, cioè con un dente avente elica destra ed uno con elica sinistra. Essi hanno un funzionamento senza vibrazioni e sono adatti ad asportare soprametalli maggiori del normale.
Valori molto elevati di angolo di elica si adottano in casi particolari, come per esempio fori molto profondi (elica a forte inclinazione in senso positivo) o dove necessitano superfici con bassa Ra (forti angoli di elica in senso negativo, i cosiddetti alesatori a taglio discendente).
Imbocco
Può avere dimensioni variabili a seconda delle esigenze del pezzo lavorato e del soprametallo da asportare. Se il soprametallo non è eccessivo e rientra nei limiti normali 0,3 – 0,7 mm) l’imbocco assume la forma di uno smusso di 2 mm a 45°. L’imbocco è la parte attiva dell’alesatore, la parte cioè che asporta il truciolo e che subisce la maggior parte dell’usura.
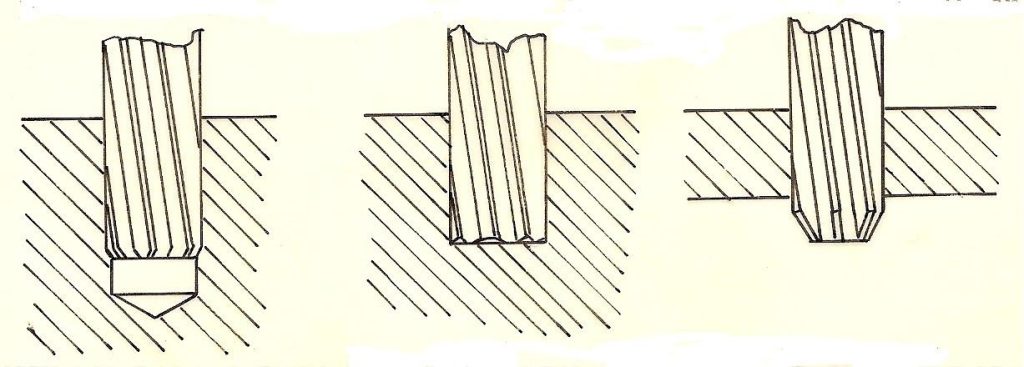
L’alesatore verrà quindi sempre affilato sull’imbocco, rettificandolo prima e poi eseguendo su ogni dente l’opportuna spoglia dorsale. Ovviamente l’imbocco deve sempre risultare centrato rispetto all’asse dell’alesatore. Anche lievi eccentricità provocano anomalie quali: ovalità, errori di allineamento, incostanza del diametro; inoltre, l’usura non sarà uniforme e avverrà in modo rapido.
L’imbocco a 45° ben si adatta a fori ciechi con un piccolo avanforo, mentre per fori passanti risulta più conveniente sia dal punto di vista della durata che da quello della miglior superficie ottenuta, un imbocco allungato, costituito da un primo tratto a 45° e da un secondo a 15°. Si assicura così un’entrata più graduale, ma il tempo di alesatura aumento leggermente.
Un ultimo tipo di alesatore adatto per fori ciechi senza raggi di raccordo sul fondo non ha l’imbocco conico ma è dotato invece di taglienti frontali. Questa particolare categoria di alesatori è impiegata spesso sui centri di lavoro a CNC.
Dovendo alesare su queste macchine fori precedentemente sgrossati con altri perché quelli con imbocco tendono ad auto-allinearsi nel foro precedente.
Questo alesatore è molto simile alle frese cilindrico-frontali e si distingue da esse per il quadretto sui taglienti periferici non spogliato e per la precisione di costruzione, (figura 6).
Fase e spoglie dorsali
Come nelle punte elicoidali, anche negli alesatori si ha una fascetta calibrata cilindrica chiamata comunemente fase o quadretto, a cui spetta il compito di guida e di conservazione della quota diametrale.
È evidente che se mancasse la fase il filo tagliente si ridurrebbe ad uno spigolo acuto che sarebbe soggetto ad una rapida usura e quindi il diametro dell’alesatore diminuirebbe dopo pochissimi pezzi.
Sui taglienti dell’imbocco (o su quelli frontali), il quadretto propriamente detto non viene eseguito negli alesatori in acciaio, si esegue invece negli alesatori in lega dura, ma è sempre consigliabile però l’uso della doppia spoglia. Nella figura 4 sono rappresentati gli angoli e gli elementi principali dei taglienti.
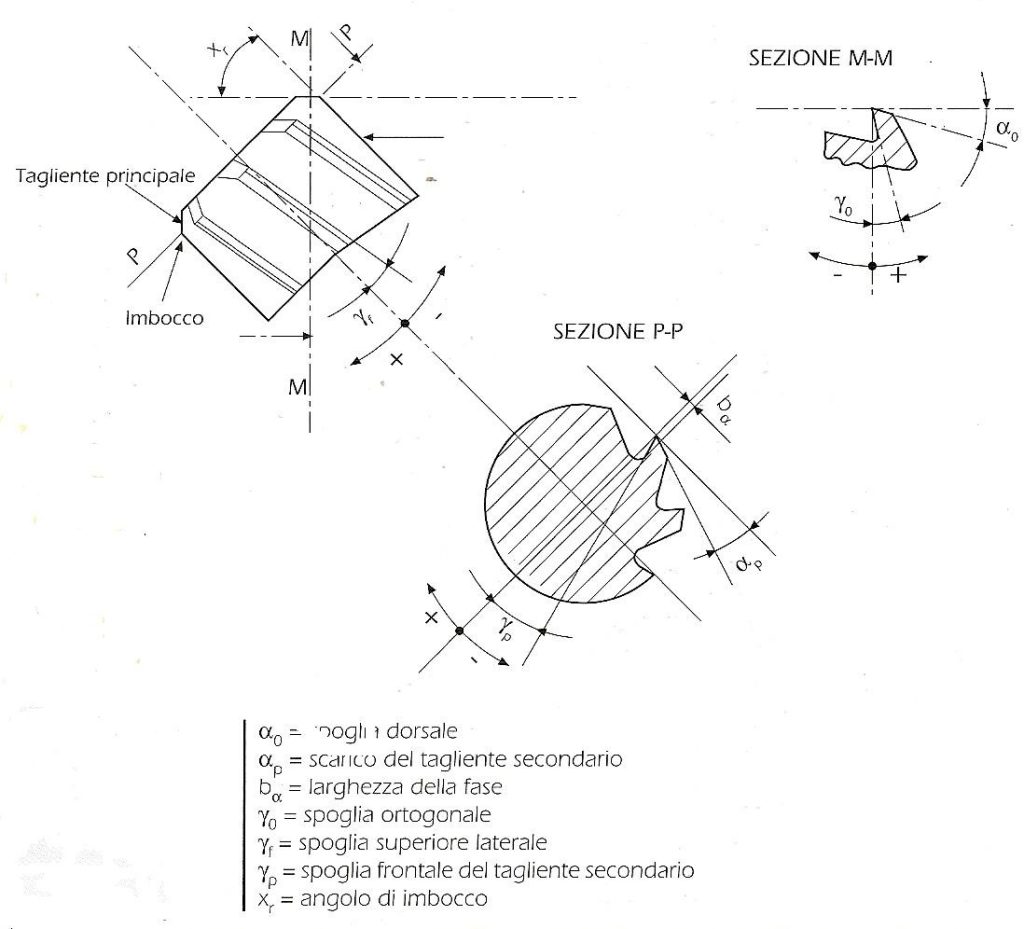
Figura 4. Angoli ed elementi principali dei taglienti.
La dimensione della fase bα varia con il diametro dell’alesatore: da 0,15 mm per diametri di 8 mm a 0,50 mm per diametri oltre 18 mm. Per quanto riguarda la dimensione della fase resta da dire che il suo valore dipende anche dal materiale lavorato e dalla sua proprietà abrasiva.
Più il materiale è abrasivo più si consumano rapidamente i taglienti sia quelli periferici che quelli dell’imbocco e quando questi sono usurati hanno tendenza a ricalcare il materiale anziché asportarlo con conseguenze dannose per le superfici.
I valori delle spoglie dorsali sul tagliente periferico αp e sull’imbocco α0 sono riportati nella tabella 1.
Angolo di spoglia dorsale sulla periferia | Angolo di spoglia dorsale sull’imbocco | ||
Diametri | Materiale | ||
Fino a 9 | 20° – 15° | Acc. con R<700 N/mm2 | 2° |
9 – 16 | 15° – 10° | Acc. duri R | 1°30’ – 2° |
16 – 25 | 10° – 8° | Acciai rapidi | 1° – 1° 30’ |
25 – 40 | 8° – 6° | Ghisa malleabile | 1°30’ – 2° |
Oltre 40 | 6° | Ottone, bronzo, Acc. Ni-Cr | 3° |
— | — | Leghe leggere | 30’ – 1° |
Angoli di spoglia anteriore
Questi angoli (Υ0 e Υp) sono analoghi alla spoglia superiore degli utensili a punta singola e seguono più o meno le stesse leggi generali.
In particolare, sarà utile ricordare che questi angoli dovranno essere tanto più grandi quanto più tenero è il materiale lavorato. I due angoli non sono indipendenti, infatti stabilito l’angolo di spoglia frontale sul tagliente secondario, cioè quello lungo la scanalatura, l’altro viene definito dall’angolo di imbocco.
I valori consigliati sono i seguenti:
- Per acciaio e ghisa malleabile: 5° – 8°
- Per ghise comuni: 0° – 5°
- Per leghe leggere: 10° – 15°
- Per bronzo e ottone: 0°- 10°
Nella tabella 2 sono schematizzate le caratteristiche costruttive di alcuni tipici alesatori con placchette in metallo duro brasate su un corpo in acciaio da costruzione ad alta resistenza.
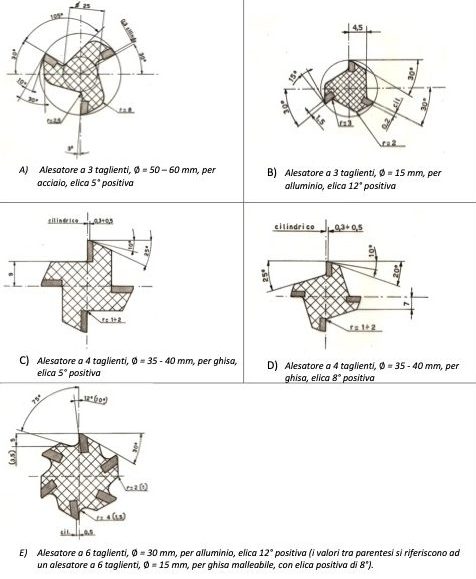
Tutti gli angoli caratteristici di questi alesatori sono in pratica uguali a quelli relativi agli alesatori in acciaio rapido. Solo l’angolo di spoglia frontale può essere leggermente inferiore.
Condizioni di lavoro in alesatura
Come in ogni lavorazione ad asportazione di truciolo è difficile, anche per l’operazione di alesatura dare dei dati precisi relativi alla velocità di taglio e di avanzamento.
In alesatura, in particolare, per stabilire questi dati bisogna tenere presente che la priorità è quella di una lunga durata del filo tagliente che garantisca la costanza dei diametri eseguiti che, come si è detto in altri articoli, hanno tolleranze molto strette.
Un altro dato molto importante che non bisogna dimenticare è che in alesatura normalmente sono richieste superfici con una bassa rugosità.
È evidente quindi che i dati riportati nella tabella 4 sono dati indicativi che servono come base per una verifica più accurata con qualche prova pratica. La tabella riporta i dati relativi ad alesatori in metallo duro. Per quanto riguarda gli alesatori in acciaio rapido, si possono considerare velocità di taglio circa la metà di quelle suggerite per il metallo duro, ma anche qui possono essere considerevolmente aumentate, fino ad arrivare ai livelli del metallo duro, se si usano alesatori in acciaio rapido ricoperti con i moderni layers.
Naturalmente molta importanza agli effetti della durata e di conseguenza della velocità di taglio permessa è il tipo di refrigerazione.
Sono molto comuni al giorno d’oggi degli alesatori con i fori interni per il refrigerante (figura 5). In questo caso il refrigerante viene portato direttamente nella zona in cui si forma il truciolo, con un maggior effetto refrigerante e lubrificante, ma soprattutto il getto di refrigerante che passa all’interno dell’utensile, facilita di molto l’evacuazione dei trucioli.
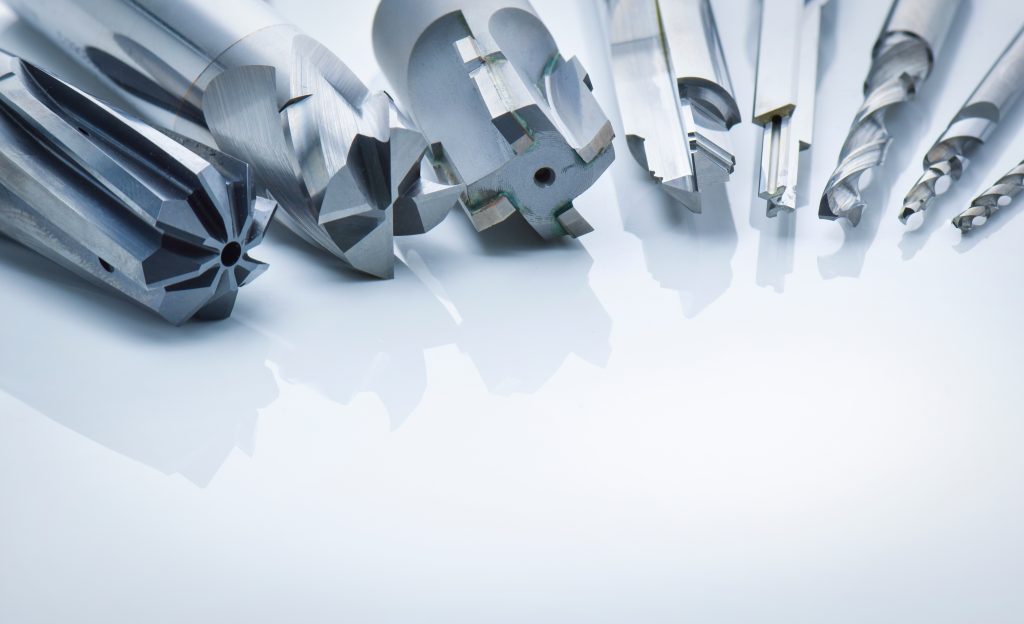
Oggi inoltre sono oggi sul mercato macchine utensili che hanno potenti sistemi di refrigerazione che sono in grado di portare il refrigerante nella zona di lavoro a pressioni molto elevate, 40 – 80 bar e anche più. In queste condizioni è evidente che le condizioni di lavoro riportate di seguito non sono più valide.
Prima dei dati sulla velocità di taglio e sull’avanzamento indichiamo nella tabella 3 quali sono i soprametalli normalmente adottati per questa operazione.
Diametro del foro (mm) | 5 – 10 | 10 – 20 | 20 – 40 |
Acciaio — Ghisa | 0,2 | 0,25 | 0,4 |
Bronzo — Ottone | 0,3 | 0,4 | 0,6 |
Alluminio | 0,4 | 0,6 | 0,8 |
Qualora sia necessario eseguire un foro con un grado di finitura molto elevato è opportuno suddividere l’operazione in alesatura di sgrossatura e alesatura di finitura. In questo caso, il soprametallo misurato sul diametro dovrà essere di circa 0,012 x D per materiali a truciolo corto e di 0,01 x D per materiali a truciolo lungo, essendo D il diametro del foro da alesare. Nella alesatura vale la norma: più sottile è il truciolo, più preciso risulta il foro alesato. Bisogna tenere presente però che lo spessore del truciolo non deve scendere sotto i 0,05 mm.
Materiale da lavorare | Velocità di taglio m/min | Avanzamento per giro in funzione del diametro (mm) | Refrigerante | ||||||
2 | 5 | 8 | 10 | 12 | 16 | 20 | |||
Acciaio non legato o poco legato | 20 – 25 | 0,10 | 0,15 | 0,20 | 0,25 | 0,30 | 0,35 | 0,40 | Olio emulsionato |
Acciaio legato e molto legato | 10 -15 | 0,10 | 0,12 | 0,15 | 0,20 | 0,25 | 0,25 | 0,30 | Olio emulsionato |
Acciaio per utensili | 8 – 10 | 0,08 | 0,10 | 0,12 | 0,15 | 0,15 | 0,20 | 0,30 | Olio da taglio |
Acciaio temprato | 6 – 8 | 0,05 | 0,08 | 0,10 | 0,15 | 0,15 | 0,20 | 0,25 | Olio da taglio |
Acciaio per molle | 8 – 10 | 0,08 | 0,10 | 0,12 | 0,15 | 0,15 | 0,20 | 0,30 | Olio da taglio |
Acciaio al Cr-Ni | 8 – 10 | 0,06 | 0,08 | 0,10 | 0,15 | 0,20 | 0,25 | 0,30 | Olio emulsionato |
Acciaio inossidabile | 10 – 15 | 0,05 | 0,08 | 0,10 | 0,15 | 0,15 | 0,20 | 0,20 | Olio emulsionato |
Acciaio legato, leghe speciali | 8 – 12 | 0,06 | 0,10 | 0,15 | 0,20 | 0,20 | 0,25 | 0,30 | Olio da taglio |
Ghisa acciaiosa | 8 – 10 | 0,06 | 0,08 | 0,10 | 0,15 | 0,20 | 0,25 | 0,30 | Olio emulsionato |
Ghisa in conchiglia | 6 – 8 | 0,08 | 0,10 | 0,15 | 0,20 | 0,25 | 0,30 | 0,35 | Olio emulsionato |
Ghisa grigia | 10 – 12 | 0,10 | 0,15 | 0,20 | 0,30 | 0,35 | 0,40 | 0,50 | A secco |
Ghisa sferoidale, ghisa malleabile | 10 – 12 | 0,10 | 0,15 | 0,20 | 0,30 | 0,35 | 0,40 | 0,50 | Olio emulsionato |
Rame | 25 – 35 | 0,15 | 0,20 | 0,25 | 0,25 | 0,30 | 0,30 | 0,40 | Olio emulsionato |
Bronzo | 25 – 30 | 0,10 | 0,15 | 0,20 | 0,25 | 0,30 | 0,35 | 0,40 | Olio emulsionato |
Leghe alluminio fino 11% di Si | 25 – 35 | 0,10 | 0,15 | 0,20 | 0,25 | 0,30 | 0,35 | 0,40 | Olio emulsionato |
Leghe alluminio oltre 11% di Si | 20 – 30 | 0,05 | 0,10 | 0,15 | 0,20 | 0,25 | 0,30 | 0,40 | Olio emulsionato |
Ottone e zinco | 30 – 35 | 0,10 | 0,15 | 0,20 | 0,25 | 0,30 | 0,35 | 0,40 | Olio emulsionato |
Titanio e leghe di titanio | 10 – 15 | 0,05 | 0,08 | 0,10 | 0,15 | 0,15 | 0,20 | 0,20 | Olio emulsionato |
Leghe di magnesio | 35 – 40 | 0,10 | 0,15 | 0,20 | 0,20 | 0,30 | 0,30 | 0,35 | A secco |
Materie plastiche termoindurenti | 25 – 30 | 0,10 | 0,15 | 0,20 | 0,25 | 0,30 | 0,40 | 0,45 | A secco |
Termoplastiche e laminati | 30 – 35 | O,15 | 0,20 | 0,25 | 0,30 | 0,35 | 0,40 | 0,50 | A secco |
Resina epossidica e fibre rinforzate | 20 – 30 | 0,05 | 0,08 | 0,10 | 0,15 | 0,20 | 0,20 | 0,25 | A secco |
Tolleranze ed errori in alesatura
L’alesatura è un’operazione di finitura dei fori, ma non tutti i fori hanno le stesse tolleranze di rotondità, di diametro e di rugosità delle superfici.
Ovviamente ci saranno tecniche ed utensili per raggiungere la massima precisione del foro nel minor tempo possibile. Inoltre, non sempre si ottengono buoni risultati a causa di disfunzioni della macchina, errori nell’attrezzatura, scelte errate delle condizioni di lavoro, materiale non omogeneo, ecc.
In generale, prima della finitura con alesatore si esegue una semi-finitura con un allargatore che ha lo scopo di uniformare il soprametallo e di correggere eventuali grandi errori di rettilineità e ovalità del foro
Le tolleranze ottenibili con i diversi cicli di lavorazione sono elencate in tabella 5.
Tolleranza richiesta | 1^ operazione | 2^ operazione | 3^ operazione |
IT 8 – 9 rotondità > 0,1 mm | Punta elicoidale standard (rotondità | Allargatore IT 8 – 9 Ra = 3,2 | Alesatore monotagliente IT 8 – Ra =1,6 |
IT<8 rotondità > 0,1 mm | Punta elicoidale standard (rotondità | Allargatore IT 8 – 9 Ra = 3,2 | 1 -Alesatore con basso angolo di elica e imbocco a 45°: Ra = 1,6 IT 7 2) Alesatore con alto angolo di elica ed imbocco doppio: Ra = 0,8 IT 6 |
IT 8 – 9 Rotondità < 0,1 mm | Punta ad elica speciale autocentrante (rotondità | Allargatore IT 8 – 9 Ra = 3,2 | — |
IT 7 Rotondità < 0,1 mm | Punta ad elica speciale autocentrante (rotondità | Allargatore IT 8 – 9 Ra = 3,2 | Alesatore con basso angolo di elica e imbocco a 45°: Ra = 1,6 IT 7 |
IT 6 Rotondità < 0,1 mm | Punta ad elica speciale autocentrante di precisione (rotondità | Allargatore IT 8 (rotondità | Alesatore con alto angolo di elica ed imbocco doppio: Ra = 0,6 IT 6 |
Per rientrare nelle tolleranze volute non è solo necessario eseguire lo smusso di imbocco accuratamente ed in modo appropriato, ma è indispensabile esaminare con cura tutti quei fattori estranei all’alesatore cui si è appena accennato, non solo, ma è anche determinante la scelta del materiale costituente l’utensile.
Se parliamo di alesatori in acciaio rapido la scelta si restringe a tre tipi fondamentali di acciaio, per ognuno dei quali si possono citare le principali prerogative:
- Acciaio rapido normale, per esempio il classico M2: può essere impiegato per alesatori a mano o per lavorare a macchina acciai dolci, ghisa e materiali non ferrosi.
- Acciaio rapido ad alto contenuto di cobalto, esempio M35, resiste bene all’usura e quindi ha una produttività maggiore del precedente. Si usa con successo su acciai duri e resistenti al calore, leghe al titanio ecc.
- Acciai molto legati ottenuti da polveri, gruppo HSS-PM; essi hanno in ogni caso prestazioni più elevate con una più lunga vita dell’utensile.
Se invece si parla di alesatori in metallo duro, si è già detto che si impiega quello de grado K10, meglio se del tipo “micrograna”.
Nella tabella 6 sono elencati alcuni fattori che hanno influenza sulla precisione del foro e sul grado di finitura delle superfici.
Fattori determinanti | Conseguenze |
Materiale dolce | L’alesatore tende ad allargare |
Materiale duro e compatto | Il foro è più preciso |
Materiale con resistenza e sovrametallo variabile | Variano le misure del foro |
Alesatura con boccola di guida | Si rispettano meglio le misure del foro |
Alesatura senza boccola di guida o comunque inefficiente | Assialità e cilindricità non rispettate; pericolo di vibrazioni |
Soprametallo piccolo | Il foro risulta più preciso; pericolo di vibrazioni |
Soprametallo grande | L’alesatore tende ad allargare |
Velocità di taglio bassa | Il foro risulta più precisi; migliori superfici |
Velocità di taglio alta | L’alesatore tende ad allargare; pericolo di vibrazioni e rigature |
Avanzamento basso | Il foro risulta più preciso; pericolo di vibrazioni |
Avanzamento elevato | Minore precisione; pericolo di rotture o scheggiature dell’utensile |
Uso di refrigerante adatto | Il foro risulta più preciso; migliori superfici |
Assenza di refrigerante | L’alesatore tende ad allargare; pericolo di rigature |
Nella tabella 7 invece sono riepilogate le più comuni anomalie che si verificano in alesatura e le loro probabili cause.
Anomalia | Cause probabili |
Usura molto forte e generata in breve tempo | Materiale lavorato più duro del previsto Velocità di taglio e avanzamento troppo elevati Angolo di spoglia anteriore troppo grande Durezza del materiale tagliente inferiore a HRC 61 |
Strappature sulla superficie lavorata | Alesatore da riaffilare Angolo di spoglia anteriore troppo piccolo Ingolfamento dei trucioli nelle gole Quadretto troppo grande |
Foro ovale o con diametro maggiorato | Alesatore scentrato sull’imbocco Accoppiamento tra codolo e mandrino imperfetto Boccola di guida usurata |
Foro con vibrature longitudinali | Quadretto troppo piccolo Numero di denti non appropriato |
Scheggiature sul filo tagliente (alesatori in metallo duro) | Metallo duro non appropriato Troppo sovrametallo Avanzamento troppo forte Velocità di taglio troppo bassa |
In particolari lavorazioni è necessario utilizzare utensili con taglienti frontali in modo da generare un piano alla fine del foro.
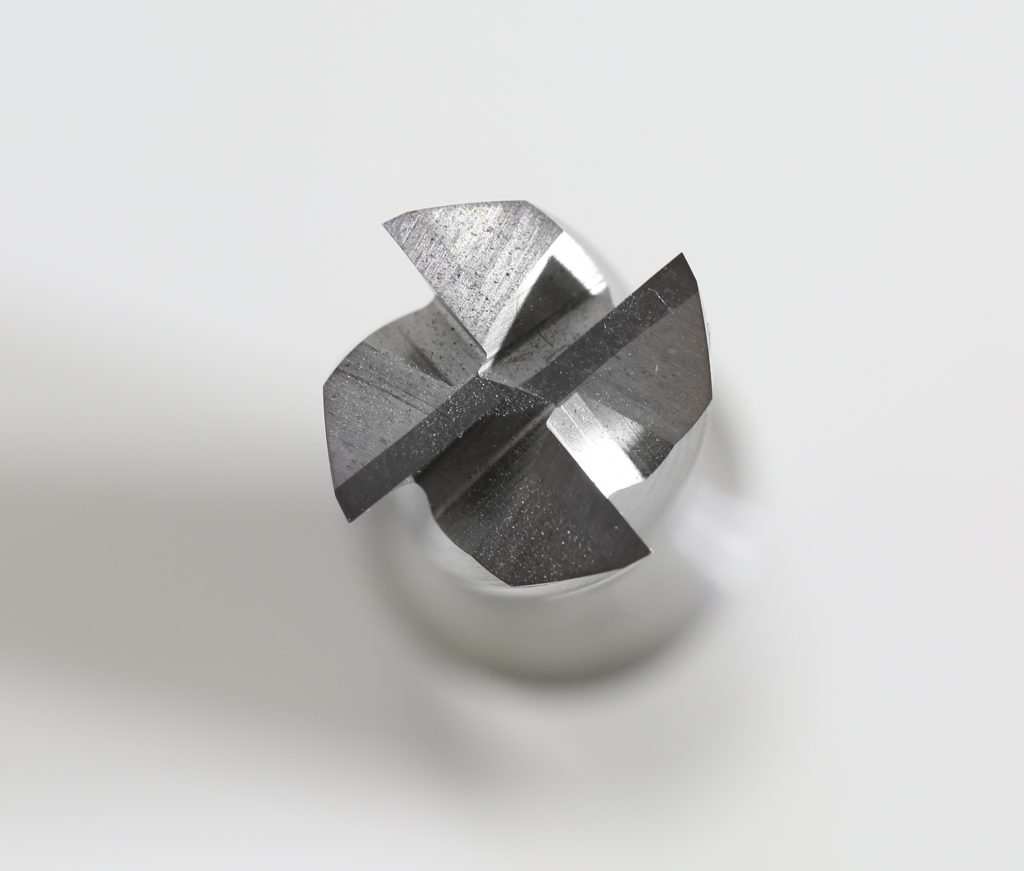
Esempio fori ciechi con sedi di perni o grani di riferimento. In questo caso si eseguono taglienti come in figura 6.