Un nuovo processo “esplosivo” di produzione dell’acciaio promette di generare metallo fuso in pochi secondi e di ridurre le emissioni. Il tutto grazie all’uso dell’idrogeno e di uno speciale forno di reazione. Scopriamo come funziona.
La produzione dell’acciaio, tradizionalmente basata sull’uso di altoforni, rappresenta uno dei processi industriali più energivori.
Gli altoforni, noti per la loro complessità e l’elevato consumo di risorse, generano significative emissioni di CO₂, rendendo la siderurgia un settore chiave nel panorama delle sfide ambientali globali.
Negli ultimi anni, la ricerca si è concentrata su tecnologie avanzate volte a ottimizzare l’efficienza energetica e a ridurre l’impatto ambientale del settore.
La CO₂ emessa è dovuta all’utilizzo del carbone, utilizzato sia per generare calore che per ridurre il minerale di ossido di ferro, rimuovendo l’ossigeno per generare ferro liquido e anidride carbonica.
Come già trattato sulle pagine di Lamiera, alcune acciaierie stanno sperimentando l’utilizzo di idrogeno al posto del carbone come agente riducente.
Una nuova tecnologia, già impiegata da decenni per i metalli non ferrosi, alza ancora di più l’asticella dell’innovazione in acciaieria: si tratta del flash ironmaking. Questo processo trae origine dal flash smelting, utilizzato per la produzione di rame.
Il flash smelting
Il flash smelting (letteralmente “fusione flash“) è una tecnologia avanzata utilizzata nel settore metallurgico per la fusione di minerali di rame. Introdotta per la prima volta negli anni ’40 dalla società finlandese Outokumpu, questa tecnologia si è affermata come uno dei metodi più efficienti e sostenibili per la produzione di rame.
Il processo di flash smelting si basa sulla reazione esotermica tra il minerale di rame (solfuro, tipicamente sotto forma di concentrato) e l’ossigeno, in un ambiente ad alta temperatura.
Il minerale finemente macinato viene miscelato con ossigeno o aria ricca di ossigeno e introdotto in un reattore ad alta temperatura.
Durante l’iniezione, il minerale si ossida rapidamente generando il calore necessario per il processo senza richiedere combustibili esterni. Il rame prodotto nel processo è nella forma di rame blister, che contiene circa il 98% di rame puro e necessita di ulteriori raffinazioni.
Uno dei padri di questa tecnologia è il Prof. Zhang Wenhai, che troveremo più avanti in questo articolo.
La ricerca del “ferro flash”
L’importanza della filiera dell’acciaio ha fatto sì che gli sforzi della comunità scientifica si indirizzassero all’applicazione del flash smelting anche per la produzione dei metalli ferrosi. Tuttavia, l’applicazione ha incontrato diverse difficoltà principalmente a causa di fattori legati alla chimica e alla fisica del processo:
– Composizione del minerale di ferro: i minerali di ferro, in particolare quelli che contengono ossidi complessi come l’ematite (Fe₂O₃) o la magnetite (Fe₃O₄), richiedono temperature molto elevate per essere ridotti efficacemente. La riduzione flash è un processo ad alta velocità che richiede un controllo preciso delle temperature e delle condizioni di riduzione. Nei primi tentativi, l’applicazione della fusione flash a questi minerali è stata difficile a causa della difficoltà nel mantenere le condizioni ottimali di temperatura e riduzione in tempi così brevi.
– Controllo della temperatura: la fusione flash richiede il raggiungimento di temperature elevate in tempi molto brevi, ma mantenere un controllo costante della temperatura dentro un reattore è complesso. Il minerale di ferro ha una temperatura di fusione relativamente alta e la necessità di evitare la sinterizzazione del minerale (processo che indurisce le particelle e rende difficile la riduzione) rendeva la gestione termica particolarmente difficile.
– Selezione degli agenti riducenti: mentre il flash smelting è stato molto efficace per i minerali non ferrosi (come il rame), applicare lo stesso principio ai minerali ferrosi ha richiesto lo sviluppo di agenti riducenti adatti. La difficoltà iniziale era trovare un agente riducente che fosse in grado di ridurre efficacemente il minerale di ferro alle temperature richieste senza causare problemi di contaminazione o di reazioni indesiderate. Il processo di produzione del ferro con idrogeno nel forno flash si distingue dai tradizionali processi di fusione flash già consolidati, come quelli per rame, piombo e zinco. La differenza fondamentale risiede nella natura delle reazioni coinvolte: mentre nei processi maturi la reazione principale è un’ossidazione esotermica dei solfuri, nel caso della produzione del ferro con idrogeno, il fulcro del processo è una reazione endotermica di riduzione degli ossidi di ferro.
– Problemi di cinetica di riduzione: la cinetica di riduzione, ossia la velocità con cui avviene la reazione chimica di riduzione degli ossidi di ferro, era un’altra sfida. L’applicazione della tecnologia flash smelting richiede che il minerale di ferro abbia una superficie di contatto molto alta per favorire la riduzione rapida. Questo richiede tecniche particolari di spruzzatura e dispersione del minerale, che non erano facili da implementare inizialmente.
– Problemi di scalabilità e costi: la fusione flash, pur essendo promettente per i metalli non ferrosi, non era facilmente scalabile per l’industria del ferro, che ha una domanda molto più alta e un costo più basso del prodotto finito. Inoltre, l’infrastruttura e le attrezzature necessarie per adattare la tecnologia flash smelting ai minerali ferrosi richiedono ingenti investimenti.
Il team guidato dal professor Hong Yong Sohn dell’Università dello Utah ha condotto una serie di sperimentazioni innovative sull’uso della tecnologia di riduzione flash per il trattamento del minerale di ferro. Tra i principali sviluppi figurano la proposta della “fusione in sospensione” e una serie di esperimenti fondamentali. I risultati ottenuti finora prevedono due strade:
– Uso del gas naturale: il gas naturale, utilizzato sia come agente riducente che come combustibile, consente di aumentare la temperatura all’interno del reattore grazie alla combustione parziale del gas. L’H+CO generato alimenta ulteriori reazioni di riduzione. A 1350 °C, con il minerale di ferro che rimane nel reattore per circa 35 secondi, il tasso di riduzione del minerale a spugna di ferro raggiunge almeno il 90%.
– Utilizzo dell’idrogeno come agente riducente: il minerale di ferro, riscaldato a 1175 °C, rimane per alcuni secondi all’interno del reattore, con un tasso di riduzione del minerale ridotto a spugna di ferro che supera il 90%.
Il team ha anche sviluppato un forno pilota su scala ridotta (circa 800×2100 mm), equipaggiato con un reattore centrale, bruciatore, alimentatore, sistema di raffreddamento ad acqua, analisi e test, nonché un sistema di controllo. Con questo impianto pilota, sono stati condotti esperimenti che hanno confermato che, a condizioni di alimentazione del minerale di ferro pari a 2,3 kg/h, una dimensione media delle particelle di 45 µm, una portata di gas naturale di 25 m³/h e ossigeno di 20 m³/h a 1250°C, è stato possibile ridurre il minerale di ferro a spugna di ferro in pochi secondi, con un tasso di riduzione pari al 94%.
Sulla base di questi principi, il team ha proposto un “nuovo processo di produzione del ferro con riduzione flash“. Questo processo impiega direttamente il minerale di ferro, che viene essiccato e spruzzato nella torre di riduzione del forno flash. Qui, il minerale si disperde nell’ambiente a temperatura elevata e in un ambiente altamente riduttivo, aumentando la superficie specifica del materiale e creando condizioni chimiche che favoriscono una reazione rapida.
I prodotti di reazione vengono separati nel bacino di fusione inferiore, dove avviene la separazione del ferro, mentre i gas di scarico sono convogliati nella sezione di trattamento dei fumi tramite una ciminiera.
I principi dinamici fondamentali della riduzione flash del ferro seguono le stesse leggi della dinamica gas-solido applicate a tutti i processi di riduzione indiretta del ferro. Tuttavia, la principale differenza risiede nella natura del materiale trattato: nei metodi tradizionali, la carica è costituita da pellet o minerali a blocchi di grande diametro, caratterizzati da una superficie specifica ridotta. In questi processi, l’utilizzo di un agente riducente gassoso comporta tempi di riduzione dell’ordine di diverse ore.
La tecnologia di fusione flash del ferro, invece, sfrutta speciali ugelli per l’iniezione diretta di minerale di ferro in polvere (a granulometria fine e elevata dispersione) all’interno di un forno flash ad alta temperatura e in un ambiente fortemente riducente. Questo approccio crea condizioni dinamiche ottimali per la riduzione, grazie alla ridotta dimensione delle particelle e alla maggiore superficie specifica disponibile per le reazioni chimiche. Di conseguenza, il processo di riduzione, che nei metodi convenzionali richiede diverse ore, può essere completato in pochi secondi, migliorando drasticamente l’efficienza e la sostenibilità del sistema produttivo.
Le ricerche del Prof. Sohn sono state pubblicate su varie riviste scientifiche come “Metallurgical & Material Transactions” e “Ironmaking & Steelmaking“. È inoltre facile trovarle raccolte nel libro “Flash Ironmaking“, pubblicato nel 2023 e disponibile su varie piattaforme di ecommerce.
Le ricerche cinesi
La Cina ha subito guardato con interesse gli sviluppi della tecnologia di flash ironmaking. In sostanza, il flash ironmaking consente di utilizzare anche minerale con bassa concentrazione di ferro e con poco pretrattamento. Questo processo, infatti, non richiede trattamenti preliminari ad alta emissione di inquinanti, come la sinterizzazione, la pellettizzazione o il coking, e presenta numerosi vantaggi, tra cui elevata efficienza, risparmio energetico, riduzione dei costi, facilità di scalabilità e la possibilità di raggiungere emissioni di carbonio pari a zero. In particolare, adottare su larga scala il flash ironmaking permetterebbe al gigante asiatico di attingere alle vaste riserve nazionali di minerale di ferro a bassa concentrazione.
Numerosi studi recenti svolti in Cina hanno quindi esaminato il processo di riduzione flash della polvere di minerale di ferro, affrontando diverse dinamiche e ottimizzazioni dei parametri di processo.
Yang Xiaobo e colleghi hanno analizzato il comportamento “gas-solido” usando CO-H₂ come agente riducente, evidenziando che il tasso di riduzione è più alto a 900°C rispetto a H₂-Ar, e che la reazione chimica interfacciale è il fattore limitante. A temperature più basse, si osservano fenomeni di deposizione di carbonio e sinterizzazione.
Zhou Guozhi ha studiato il comportamento multifase “gas-liquido“, proponendo modelli dinamici per descrivere l’influenza di vari parametri sul tasso di riduzione, mentre Zhang Liangliang ha sviluppato un sistema di simulazione numerica per analizzare la cementazione del ferro metallico e ottimizzare i parametri del processo.
Yang ha anche integrato la gassificazione del carbone con la riduzione flash, sviluppando un modello CFD per prevedere il flusso e la temperatura, e Abdelghany ha esplorato l’uso del gas naturale come agente riducente, costruendo un modello CFD per analizzare il tasso di riduzione della polvere di magnetite.
Un modello CFD (Computational Fluid Dynamics) è una simulazione numerica utilizzata per analizzare il comportamento di fluidi (gas o liquidi) e il loro scambio di calore e materia con le superfici circostanti.
Alabarda spaziale? No, lancia a vortice
La vera svolta è arrivata pochi mesi fa, quando il team del Prof. Zhang Wenhai è riuscito ad ottimizzare il design della torre di riduzione del forno flash, migliorando l’efficienza complessiva del sistema. Attraverso studi di simulazione e ottimizzazione, il gruppo di ricerca ha analizzato il comportamento delle scorie sulle pareti della torre durante il processo di riduzione flash della polvere di minerale di ferro. Questo ha permesso di identificare l’influenza di diversi parametri di processo, nonché la forma e le caratteristiche strutturali del forno, sullo spessore delle scorie aderenti, portando così a un’ottimizzazione del design.
Oltre alle ricerche e alle migliorie dal punto di vista chimico, uno degli ostacoli da superare per l’industrializzazione del flash ironmaking era la necessità di garantire un flusso costante e uniforme di materiale. Il Prof. Wenhai e il suo team hanno sviluppato una lancia di insufflaggio denominata vortex lance, o lancia a vortice. Questa speciale lancia utilizza un flusso vorticoso di gas per migliorare la dispersione e il contatto tra il minerale di ferro in polvere e il gas riducente, aumentando così l’efficienza della reazione. Grazie a questa configurazione, si ottiene un trasferimento di calore e massa più uniforme, riducendo il consumo energetico e migliorando il tasso di riduzione. Inoltre, questa innovativa pistola a spruzzo consente di estendere la traiettoria di caduta delle particelle, aumentando il tempo di permanenza del minerale all’interno della torre e migliorando ulteriormente l’efficienza del processo.
I risultati di questi esperimenti sono stati recentemente pubblicati nell’articolo “Research progress of flash ironmaking technology” sulla rivista Nonferrous Metals.
A differenza del processo sviluppato dal professor H.Y. Sohn, che produce ferro spugnoso, il team di Wenhai ha integrato una vasca di separazione alla base della torre di riduzione, ispirandosi alla consolidata tecnologia di fusione flash già in uso per altri metalli non ferrosi. Inoltre, ha sviluppato autonomamente un forno pilota di 1,2×5,4 m (con un tubo di 0,12×2,7 m), dotato di torre di riduzione, vasca di separazione, riscaldatori, alimentatori, sistema di raffreddamento ad acqua, strumenti di analisi e test, e un sistema di controllo avanzato. Utilizzando questa infrastruttura, il team ha condotto una serie di esperimenti su scala pilota, dimostrando che, con una velocità di alimentazione del minerale di ferro di 2,3 kg/h, una granulometria media di 45 µm, una portata di gas naturale di 25 m³/h, una portata di ossigeno di 20 m³/h e una temperatura di riduzione tra 1350 e 1500 °C, il minerale di ferro può essere trasformato in metallo fuso in soli 10 secondi, con un tasso di riduzione superiore al 90%.
didascalia: il forno di reazione del team del prof. Z. Wenhai. Sulla destra, in alto il minerale di ferro polverizzato e in basso l’acciaio ottenuto tramite flash smelting. Credit: Z. Wenhai et al.
Come nel caso del processo tradizionale, è possibile sostituire il coke con il gas naturale, ma soprattutto con l’idrogeno. Questo processo è già sperimentato ed utilizzato dalle acciaierie europee negli altoforni “fossil free” (seppure su scala ridotta) e già presentato in queste pagine in passato.
Nel caso in cui si utilizzi l’idrogeno, i fumi del flash ironmaking possono contenerne un’elevata concentrazione. Questo fattore, insieme all’elevata temperatura dei fumi, comportano un significativo consumo energetico. Tuttavia, l’adozione di avanzati sistemi di recupero e trattamento dei fumi può migliorare il bilancio energetico complessivo. Le principali apparecchiature aggiunte includono:
– Sistema di recupero del calore: una tecnologia consolidata che permette di riutilizzare oltre il 95% dell’energia termica dei fumi, con un’efficienza pari ad almeno l’85%. Il vapore generato nel recupero viene impiegato nell’essiccatore a vapore del processo precedente;
– Sistema di rimozione della polvere: in grado di recuperare circa il 4% delle particelle solide presenti nei fumi, con un’efficienza di filtrazione superiore al 99%;
– Sistema di ciclo di purificazione: utilizzato per rimuovere circa il 40% dell’acqua e il 5% delle impurità presenti nei fumi;
– L’idrogeno incombusto viene recuperato con un’efficienza di oltre il 98%, consentendo il suo riutilizzo nel processo.
Inoltre, le acque reflue contenenti ioni metallici possono essere trattate con processi idrometallurgici, come l’elettrolisi, per il recupero di metalli di valore. Il consumo energetico complessivo (351 Kgce per tonnellata di acciaio) del ferro flash è inferiore a quello del processo di produzione del ferro in altoforno (553 Kgce per tonnellata di ferro).
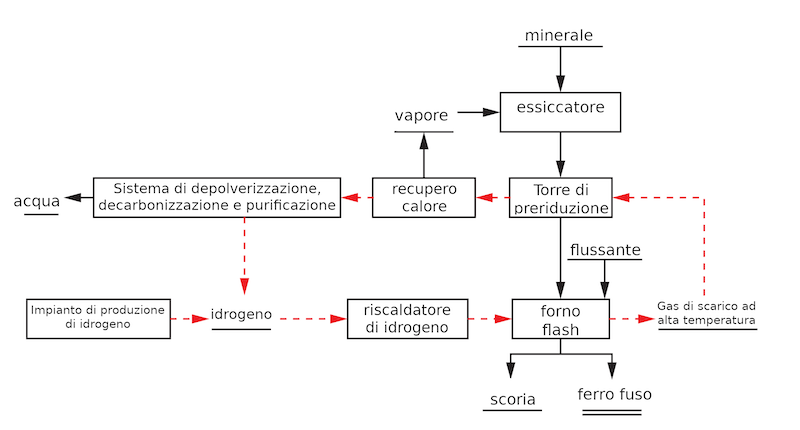
Approfondimento su ammoniaca e idrogeno
Il termine Kgce (Kilogrammi equivalenti di carbone) è un’unità di misura che permette di confrontare diverse fonti energetiche in base al loro contenuto energetico equivalente a quello del carbone.
Idrogeno come riducente
La produzione del ferro avviene attraverso la rimozione dell’ossigeno dagli ossidi di ferro, un processo che richiede un agente riducente capace di donare elettroni. L’idrogeno è particolarmente efficace per questo scopo e non produce anidride carbonica.
L’ammoniaca (NH₃) svolge un ruolo chiave in questo processo avanzato di produzione del ferro poiché può essere utilizzata come vettore di idrogeno (H₂) L’ammoniaca rappresenta una soluzione pratica per immagazzinare e trasportare l’idrogeno grazie alla sua elevata densità energetica e ai ridotti rischi di esplosione. Una volta sul luogo di utilizzo, può essere decomposta per liberare idrogeno gassoso, rendendolo disponibile per il processo di riduzione.
L’analisi precedente evidenzia che il principale fattore che incide sul consumo energetico complessivo del processo di produzione del ferro con idrogeno nel forno flash è la quantità e la temperatura dei fumi in uscita. Il consumo di idrogeno, invece, non rappresenta una variabile influente, poiché questo viene impiegato principalmente nella reazione di riduzione e il suo fabbisogno teorico è fisso. L’idrogeno non reagito può essere recuperato e riutilizzato, riducendo così gli sprechi. Tuttavia, un aumento della quantità e della temperatura dei fumi comporta una maggiore necessità di recupero di calore e ossigeno. A parità di efficienza e tasso di dispersione, un incremento di questi parametri si traduce in maggiori perdite e, di conseguenza, in un aumento del consumo energetico.
I principali fattori che determinano la quantità di fumi generati nel forno flash includono il contenuto di idrogeno e la presenza di gas di impurità. Secondo il diagramma di equilibrio della fase gassosa nella riduzione degli ossidi di ferro con H₂ a diverse temperature, il contenuto di idrogeno nei fumi è direttamente correlato alla temperatura: temperature più basse richiedono un quantitativo maggiore di idrogeno per la riduzione, mentre temperature più alte ne riducono il fabbisogno. I gas di impurità nei fumi derivano principalmente dalla reazione di riduzione e dalla combustione.
Fattori limitanti e potenzialità di scala del forno flash
La capacità di un singolo forno flash è determinata da tre fattori principali. Il primo riguarda la quantità di minerale di ferro che può essere spruzzata ogni ora attraverso la lancia, insieme alla capacità di distribuire uniformemente le particelle. Il secondo è l’intensità termica all’interno della torre di riduzione, che non deve superare i 2500 MJ/(m³·h). Il terzo è il tempo di permanenza del minerale, che deve essere di almeno 3 secondi.
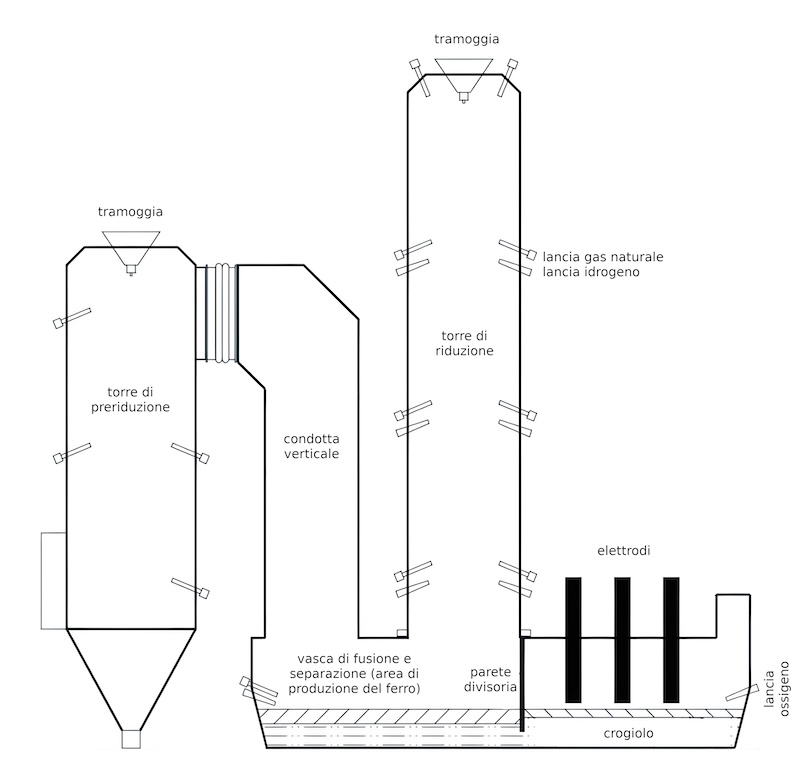
Mentre i vincoli termici e di permanenza possono essere gestiti attraverso un’attenta progettazione della torre di riduzione – ottimizzando il diametro interno, l’altezza e la conformazione della sommità – la capacità di insufflaggio del minerale può essere calcolata e ottimizzata grazie a software di simulazione ingegneristica come Metsim, che consente di modellare il processo produttivo del forno flash. L’obiettivo della tecnologia di produzione del ferro con forno flash è realizzare la produzione di acciaio in un solo passaggio all’interno del forno flash, produrre acciaio fuso di alta qualità e, allo stesso tempo, produrre la cosiddetta “scoria bianca” a basso contenuto di ossido di ferro e realizzare il recupero del calore residuo dei fumi ad alta temperatura e il recupero dell’idrogeno.
Le ricerche del team del Prof. Zhang Wenhai hanno dimostrato l’efficacia della lancia a vortice, che garantisce una distribuzione uniforme ad alta efficienza. Grazie a questa tecnologia, la capacità di insufflaggio può raggiungere 450 tonnellate all’ora, corrispondenti a una produzione annua di ferro di circa 2,37 milioni di tonnellate per singola unità. Un forno flash dotato di tre lance può raggiungere una produzione annua di 7,11 milioni di tonnellate, offrendo un notevole potenziale di scalabilità. Per dare un termine di paragone, si tratta della quantità di acciaio prodotta dall’intero polo siderurgico olandese di IJmuiden.
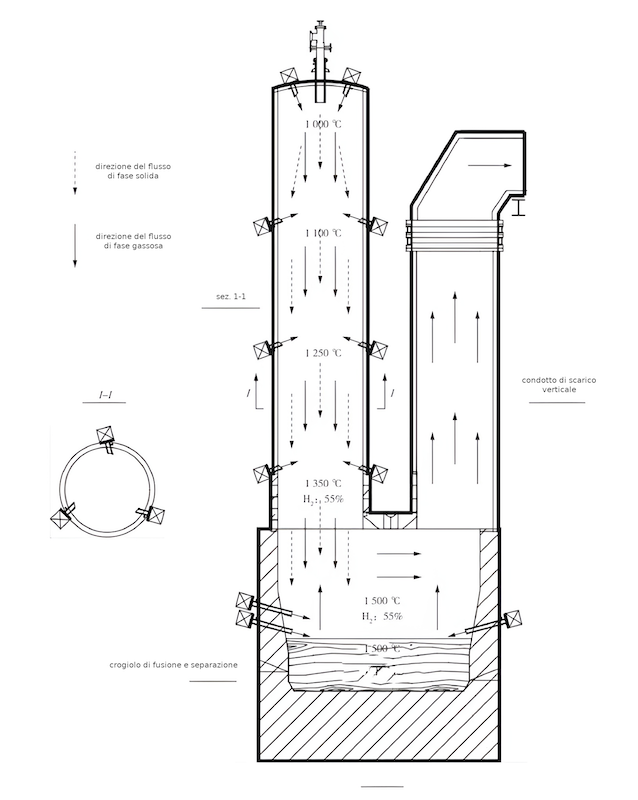
Sfide e prospettive future
Nonostante il suo potenziale, la produzione di ferro flash deve affrontare sfide che devono essere affrontate per la redditività commerciale:
– Ostacoli tecnici: il raggiungimento di una riduzione uniforme e la prevenzione di problemi come l’incollamento delle particelle o l’intasamento del reattore richiedono un controllo preciso delle condizioni operative.
– Requisiti infrastrutturali: l’implementazione di questa tecnologia richiede modifiche significative agli impianti di produzione dell’acciaio esistenti o la costruzione di nuovi impianti, con notevoli investimenti di capitale.
– Utilizzo dell’idrogeno: sebbene l’idrogeno offra il vantaggio di azzerare le emissioni di CO₂ quando viene utilizzato come agente riducente, la sua adozione su larga scala dipende dalla disponibilità di metodi di produzione dell’idrogeno economicamente vantaggiosi e sostenibili.
La ricerca in corso si concentra sull’ottimizzazione dei progetti dei reattori, sul miglioramento del controllo dei processi e sull’integrazione delle fonti di energia rinnovabili per produrre idrogeno verde. La collaborazione tra istituzioni accademiche, operatori del settore e agenzie governative è fondamentale per far progredire la tecnologia di produzione di ferro Flash verso l’implementazione commerciale.
Implicazioni economiche e geopolitiche
La capacità della tecnologia flash ironmaking di utilizzare minerale di ferro di qualità inferiore potrebbe alterare in modo significativo le dinamiche economiche globali, in particolare nel settore siderurgico.
Tradizionalmente, paesi come la Cina si affidano pesantemente all’importazione di minerale di ferro di alta qualità da fornitori primari quali l’Australia, il Brasile e l’Africa per soddisfare la loro domanda di produzione. Questa dipendenza non solo comporta costi elevati, ma rende la produzione di acciaio vulnerabile alle fluttuazioni dei prezzi e alle tensioni geopolitiche.
Consentendo l’uso diretto di abbondanti minerali di bassa e media qualità, la siderurgia flash può ridurre la dipendenza della Cina dai minerali importati, potenzialmente in grado di interrompere i flussi commerciali globali. Per i paesi ricchi di risorse, nello specifico quelli che dominano le esportazioni di minerale di alta qualità, questo spostamento potrebbe portare a una diminuzione della domanda, mettendo sotto pressione le loro industrie minerarie e le loro economie. D’altro canto, i paesi con abbondanti riserve di minerale di qualità inferiore potrebbero assistere a un aumento dell’utilizzo delle risorse, creando nuove opportunità economiche e favorendo la crescita industriale locale.
Questa ridistribuzione della domanda potrebbe anche incoraggiare un mercato globale del minerale di ferro più equo, riducendo l’influenza monopolistica di alcuni esportatori chiave e favorendo una maggiore resilienza della catena di approvvigionamento.
In definitiva, l’adozione diffusa del flash ironmaking potrebbe rimodellare le relazioni economiche all’interno dell’industria siderurgica.