Il trattamento di indurimento superficiale mediante laser di componenti meccanici è un sistema di lavorazione che ha incontrato negli ultimi anni un consenso industriale in continua crescita, grazie ad alcune caratteristiche peculiari che lo differenziano dai suoi diretti competitori.
Alla base della tecnologia di indurimento superficiale mediante laser c’è l’opportunità di riscaldare la superficie del componente in modo selettivo, mantenendo il più possibile controllata la temperatura la quale, infatti, deve essere superiore ai valori critici che sono funzione del materiale e dello specifico trattamento da realizzare, ma anche inferiore al punto di fusione del materiale stesso al fine di non causare un inaccettabile deterioramento della superficie della parte lavorata.
A tale scopo le prime applicazioni industriali di trattamento termico prevedevano l’utilizzo di una sorgente di calore a fiamma opportunamente veicolata sulla superficie da trattare attraverso un sistema di bruciatori geometricamente configurati in modo da adattarsi alla conformazione della superficie stessa e garantirne un riscaldamento il più possibile uniforme.
A valle di tale sorgente veniva poi applicato un flusso d’aria o di liquido refrigerante che provvedesse allo “spegnimento” adeguato del materiale favorendo la formazione di strutture di tempra in uno strato di materiale con spessori dell’ordine del millimetro.
L’utilizzo della fiamma naturalmente, non essendo una sorgente ad elevata concentrazione di energia, comportava grandi difficoltà nel controllo sia della temperatura massima raggiunta dal pezzo, sia dell’estensione della zona effettivamente riscaldata e poteva causare un inquinamento indesiderato del materiale dovuto alla presenza dei prodotti della reazione di combustione tra combustibile e comburente.
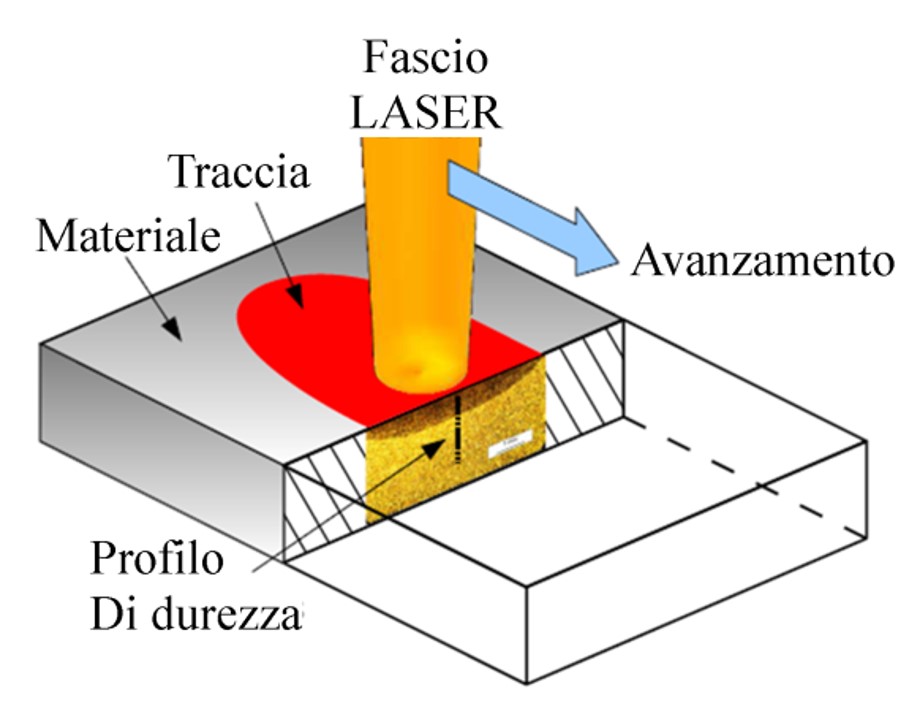
L’introduzione dei sistemi di riscaldamento a induzione elettromagnetica, che equipaggiano tutt’ora la maggior parte delle attuali attrezzature per indurimento superficiale, ha consentito di ridurre le problematiche peculiari della tecnologia a fiamma, non senza introdurre, però, nuove criticità.
In primo luogo, la forma dell’induttore deve adattarsi in maniera sufficientemente precisa alla geometria da trattare, in modo da garantire un “traferro” costante tra i conduttori e favorire, di conseguenza, una distribuzione uniforme delle correnti parassite dalle quali dipende direttamente il riscaldamento del materiale.
Tale condizione pregiudica in maniera sensibile il trattamento delle superfici geometricamente complesse e che presentino “features” di piccole dimensioni quali fori, spallamenti, dentature, scanalature, etc. In secondo luogo, è opportuno sottolineare la grande richiesta di potenza elettrica atta a garantire un riscaldamento adeguato delle superfici e ottenere la profondità di trattamento desiderata. Tenendo conto dei rendimenti non particolarmente brillanti di questo tipo di processo non è infrequente l’impiego di impianti per induzione con potenze nominali di 150 kW e oltre.
Alla luce delle problematiche sopra descritte si può comprendere come l’impiego di un fascio LASER concentrato possa divenire congeniale alla realizzazione di trattamenti estremamente efficienti per l’indurimento superficiale di componenti metallici.
La possibilità, infatti, di riscaldare il materiale semplicemente “illuminandolo” con una radiazione di potenza nota, con data lunghezza d’onda ed opportunamente focalizzata in modo da ottenere l’irradianza necessaria a riscaldarlo sufficientemente (fig. 1), apre uno scenario applicativo totalmente nuovo, nel quale il fascio laser diviene “l’utensile universale” per il trattamento termico di ogni tipo di superficie.
La mancata necessità di un utensile costruito “ad hoc” per la geometria specifica del pezzo in questione determina, tra l’altro, il completo svincolamento delle caratteristiche costruttive dell’impianto di trattamento da quelle geometriche dei componenti da lavorare, garantendo una forte versatilità applicativa ed una notevole scalabilità dell’attrezzatura stessa, consentendo la possibilità di trattare virtualmente ogni tipo di geometria e dimensione.
Il riscaldamento del materiale, per effetto dell’interazione dello stesso con la radiazione laser, è circoscritto all’area della superficie dello “spot” che, istante per istante, si muove sulla superficie da trattare.
Tale condizione determina, nella maggior parte dei casi industriali, un effetto di “auto-spegnimento” dovuto all’azione di drenaggio del calore che la grande massa di materiale freddo circostante compie sulla piccola porzione di materiale riscaldato, determinando la mancata necessità di utilizzare un fluido refrigerante durante il processo, il quale invece risulta pressoché indispensabile nei procedimenti tradizionali a fiamma o a induzione.
L’effetto di auto-spegnimento, qualora la massa e lo spessore del componente non siano troppo contenuti, è così marcato da consentire anche la tempra laser superficiale di materiali normalmente non classificabili come autotempranti, quale ad esempio l’acciaio C40.
Tra le applicazioni industriali dei LASER di elevata potenza, quella del trattamento di indurimento superficiale può essere definita, a ben vedere, come “contro corrente” in quanto, dovendo garantire il riscaldamento controllato a temperature ben al di sotto del punto di fusione del materiale oggetto del trattamento, implica la necessità di utilizzare spot con dimensioni relativamente grandi e con distribuzioni di potenza il più possibile costanti.
Tale prerogativa, in prima considerazione, potrebbe sembrare in disaccordo con tutte le caratteristiche considerate salienti delle radiazioni laser (elevata focalizzabilità, spot con dimensioni estremamente ridotte, elevata brillanza, valori di M2 prossimi a 1, etc.), chiamando in causa un uso che parrebbe quasi “improprio” del laser stesso.
In realtà l’introduzione di questa tecnica piuttosto recente di trattamento superficiale ha aperto la scena a sorgenti, quali quelle a diodi, che fino ad ora non avevano trovato una precisa collocazione nell’ambito delle lavorazioni industriali ad alta potenza, risultando impiegate quasi esclusivamente come sorgenti di pompaggio per i più “raffinati” laser allo stato solido. Tra le caratteristiche peculiari delle sorgenti a diodi quelle che le rendono particolarmente idonee alle applicazioni di trattamento superficiale sono:
• la possibilità di essere organizzate ed assemblate in array e stack per creare spot con forme quadrate o rettangolari ottimizzando, di conseguenza, il riscaldamento della superficie e la velocità del trattamento;
• la distribuzione di potenza pressoché costante su tutta l’area dello spot, la quale consente un riscaldamento maggiormente controllabile e uniforme;
• la possibilità di essere impiegate in configurazione a “illuminazione diretta” oppure con trasporto in fibra ottica, con conseguente grande versatilità di impiego sia in configurazioni in linea che fuori linea;
• la lunghezza d’onda compresa tra 800 e 1000 nm, la quale favorisce un assorbimento della radiazione da parte del materiale trattato maggiore rispetto a quella ottenibile utilizzando qualunque altro tipo di laser industriale ad alta potenza;
• l’elevata potenza attualmente ottenibile, la quale può essere di oltre 6 kW;
• la buona affidabilità e l’assenza pressoché totale di manutenzione;
• la semplicità costruttiva della sorgente ed il suo relativamente basso costo.
In realtà il trattamento termico superficiale mediante laser può essere realizzato con qualunque altro tipo di sorgente, sia allo stato solido che allo stato gassoso, con fascio opportunamente defocalizzato, in modo da ottenere le densità di potenza corrette per il tipo di applicazione, ed eventualmente corretto con elementi ottici che ne rendano il profilo spaziale il più possibile con distribuzione di potenza costante.
Una delle prerogative chiave per comprendere come il trattamento termico laser superficiale possa essere industrialmente interessante è l’intrinseca possibilità di implementare lo stesso direttamente sulla linea di produzione, evitando di ricorrere a lavorazioni di trattamento in conto terzi.
La facilità di movimentazione ed il ridottissimo ingombro della testa di focalizzazione (specialmente per i fasci trasportati in fibra), unitamente alla mancata necessità di un mezzo di spegnimento, rendono infatti la tecnologia in oggetto facilmente integrabile in una qualunque linea di produzione, sia attraverso una movimentazione mediante braccio antropomorfo che mediante sistemi più rigidi posizionati direttamente a bordo macchina.
Sono descritte di seguito due attività preliminari di studio del trattamento termico superficiale mediante laser, condotte presso il Laboratorio MATMEC, focalizzate su due specifici filoni di ricerca, distinti ma complementari tra loro, come:
• l’applicazione sperimentale del processo su materiali e geometrie diverse al fine di valutarne con precisione i campi di applicabilità e determinarne le condizioni ottimali di implementazione;
• la modellazione matematico-numerica dei fenomeni che vi stanno alla base con lo scopo di ottenere strumenti in grado di simulare condizioni reali di lavorazione, prevedendo i risultati del trattamento in termini di estensione delle zone trattate, di durezze ottenibili e di microstrutture risultanti nel materiale.
Per comprendere meglio i vantaggi del trattamento termico superficiale mediante laser è opportuno analizzare un caso industriale analizzato e studiato riguardante la tempra superficiale dei fianchi verticali di una sede per linguetta ricavata sul mozzo di un limitatore di coppia realizzato in acciaio al carbonio C43. Allo stato attuale il componente viene trattato ad induzione tramite una lavorazione in conto terzi ed il risultato è mostrato in figura 2.
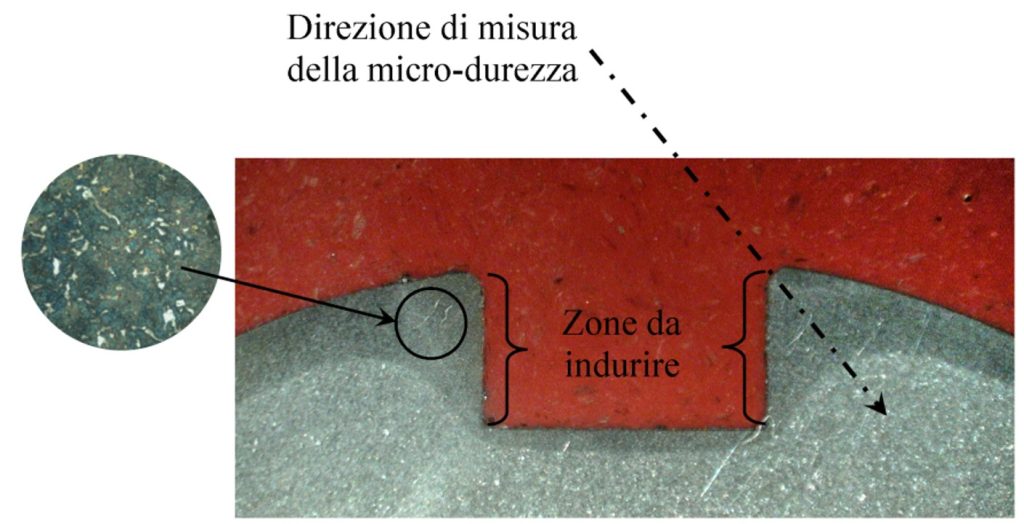
Si può notare chiaramente come la zona temprata interessi tutta la superficie esterna del componente, a fronte di una richiesta di indurimento estremamente circoscritto come mostrato in sempre in figura 1. Ciò dimostra come gran parte della potenza elettrica impiegata durante il processo vada “sprecata”, per lo meno in questo specifico caso, per indurire zone del pezzo per le quali il trattamento non risulta necessario.
Inoltre, la micrografia ingrandita a sinistra della figura mostra una struttura martensitica tutt’altro che uniforme, nella quale sono presenti evidenti tracce di ferrite non trasformata.
Lo studio di fattibilità ha portato a realizzare lo stesso trattamento mediante una sorgente laser, come mostrato in figura 2, nella quale si notano le zone trattate estremamente circoscritte e la formazione di una struttura martensitica uniforme e priva di tracce di ferrite.
Confrontando i dati di durezza, misurati nelle direzioni indicate in figura 2 e 3 e riportati nel grafico di figura 4, si evince come il trattamento mediante laser consenta di ottenere una durezza superiore di circa 100 HV rispetto a quella ottenibile con la tradizionale tempra a induzione.
Per quanto riguarda il set-up dell’esperimento si può fare riferimento allo schema di figura 5, nel quale sono rappresentati i parametri tecnologici impiegati e il posizionamento del fascio rispetto al componente.
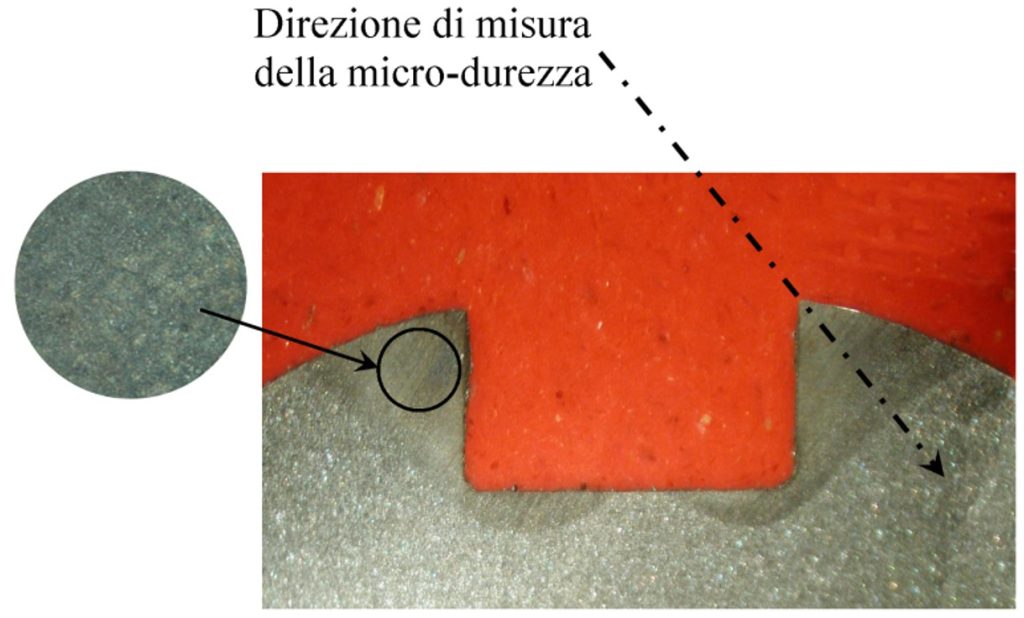
Le casistiche industriali per le quali può essere richiesto un trattamento superficiale di indurimento, naturalmente, non si limitano superfici e “features” di dimensioni limitate e molto circoscritte come nel caso appena analizzato, ma spesso coinvolgono porzioni di spazio con estensioni molto più grandi rispetto alla dimensione media dello spot laser, la quale normalmente non supera i 10 mm di diametro.
In questi casi la strategia di trattamento mediante l’utilizzo di un fascio laser non può essere del tipo a “singola passata”, ma occorre campire la superficie da trattare con passate sufficientemente ravvicinate che consentano un riscaldamento del materiale il più possibile uniforme.
Tale strategia, se da un lato può essere facilmente implementata dai sistemi di movimentazione robotizzata del fascio, dall’altra è causa di una problematica particolarmente delicata chiamata “effetto di rinvenimento”.
Supponendo infatti di realizzare una prima passata di trattamento mediante un fascio laser e di affiancare a quest’ultima una seconda passata in modo tale che vi sia continuità tra le due zone riscaldate, accade inevitabilmente che il calore sviluppato dalla seconda passata vada a innalzare la temperatura di parte della zona interessata dalla prima al di sopra dei valori critici caratteristici dello specifico materiale, innescando il rinvenimento dello stesso con conseguente calo della durezza nella zona interessata dal fenomeno.
Tale effetto è tanto più marcato quanto più le passate sono temporalmente ravvicinate in quanto il materiale già trattato non fa in tempo a raffreddarsi completamente prima dell’arrivo della passata successiva, con conseguente ampliamento dell’area soggetta al calo di durezza.
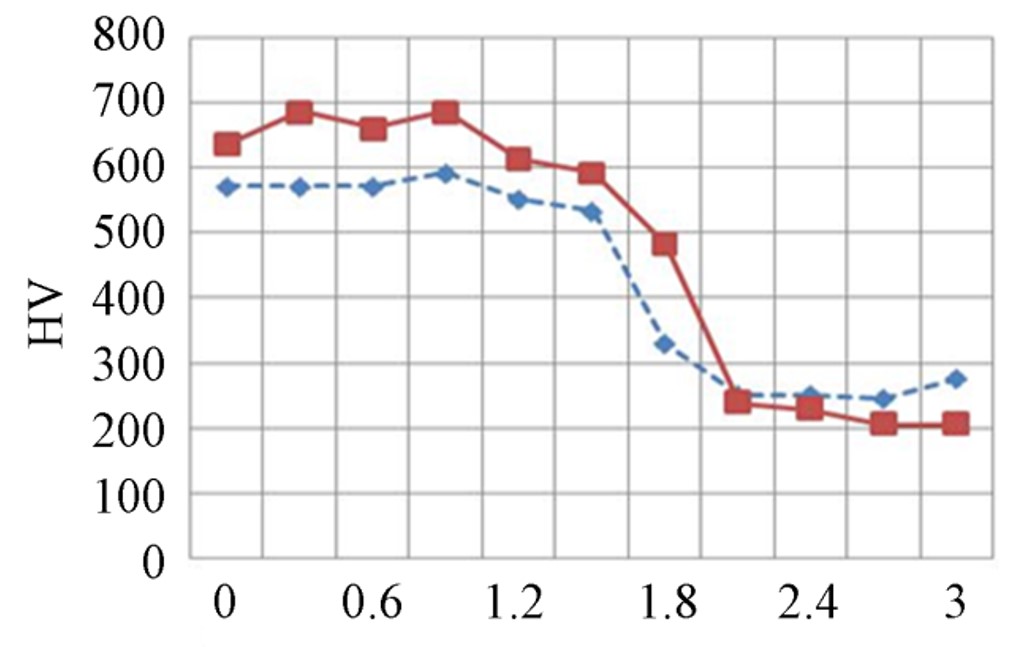
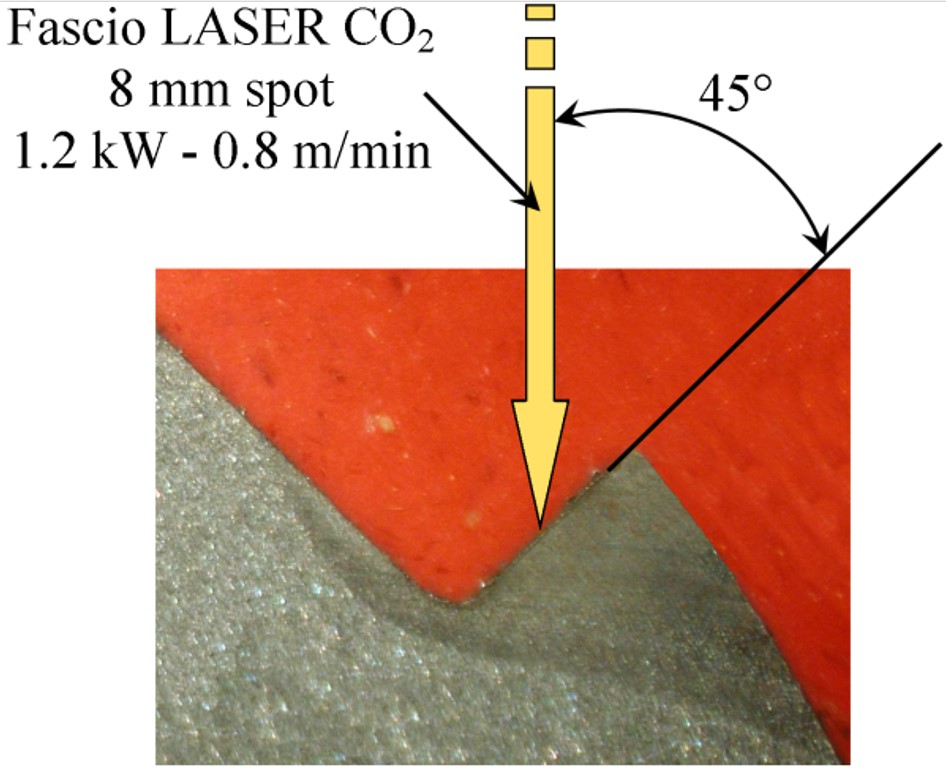
La micrografia di figura 6, corredata del relativo grafico, mostra il comportamento di un trattamento superficiale in due passate mutuamente sovrapposte del 30% realizzato su un acciaio C40; si nota chiaramente la zona rinvenuta (ombreggiata in colore più scuro) e il corrispondente calo di durezza il quale, in realtà, interessa non solo la porzione di materiale a immediato ridosso della seconda passata, ma tutta l’area interessata dalla prima.
Lo schema dimostra chiaramente anche l’effetto del preriscaldo dato dalla prima passata sulla zona temprata corrispondete alla seconda: quest’ultima risulta infatti più estesa della prima sia in senso longitudinale che verticale, sintomo che il fascio LASER, durante la seconda passata, ha investito una porzione di materiale non più a temperatura ambiente, ma con un certo grado di preriscaldo dipendente dal tempo intercorso tra un passaggio e l’altro.
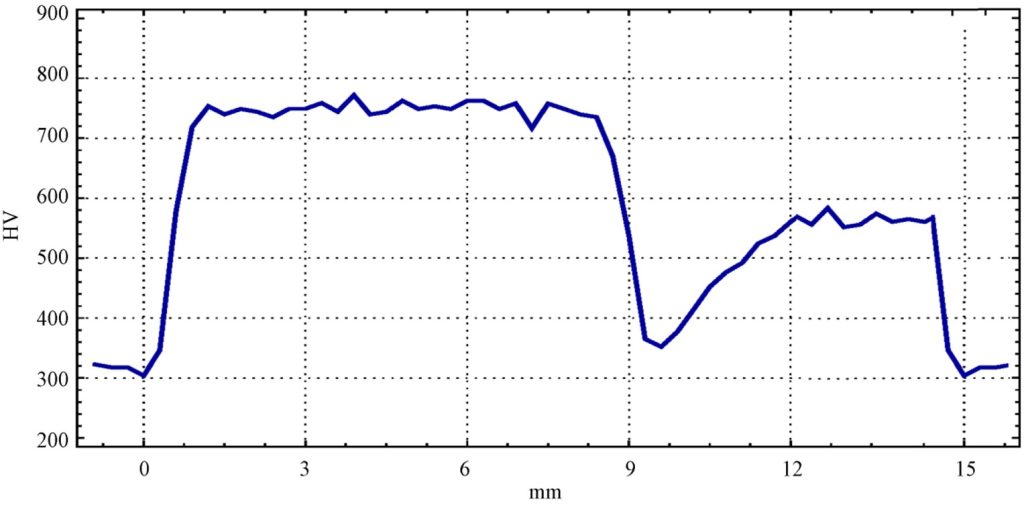
Il problema del rinvenimento non può essere totalmente eliminato in quanto la relativamente elevata conducibilità termica dei materiali metallici, unitamente alla necessità di realizzare passate adiacenti con un certo grado di sovrapposizione per favorire un adeguato riscaldamento di tutta la zona di interesse, causano inevitabilmente un calo di durezza nella porzione di materiale interessata dall’interazione tra passate adiacenti.
Tale fenomeno, tuttavia, può essere minimizzato agendo su numerosi fattori, quali la sequenza ed il verso delle passate, la velocità delle stesse, il grado di mutua sovrapposizione ed il tempo tra una passata e l’altra. Per comprendere meglio questa affermazione si faccia riferimento alle figure 7, 8 e 9, in cui sono rappresentati i profili di durezza rilevati “sotto pelle” per diverse strategie di trattamento laser a tre passate su acciaio C40.
Si noti come il realizzare le passate una di seguito all’altra (fig. 7) sia la strategia peggiore, in quanto la prima passata risente sia dell’effetto della seconda che della terza. Semplicemente variando la sequenza di passaggio, realizzando prima e seconda passata distanziate tra loro e poi la terza tra di esse (fig. 8), si ottiene un beneficio in termini di uniformità di durezza. Anche il grado di sovrapposizione influenza il risultato del trattamento: il grafico di figura 9 mostra come, passando dal 60% al 40% di sovrapposizione, mantenendo sempre una strategia di passata di tipo 1-3-2, si ottenga un ulteriore miglioramento in termini di uniformità nel profilo di durezza.
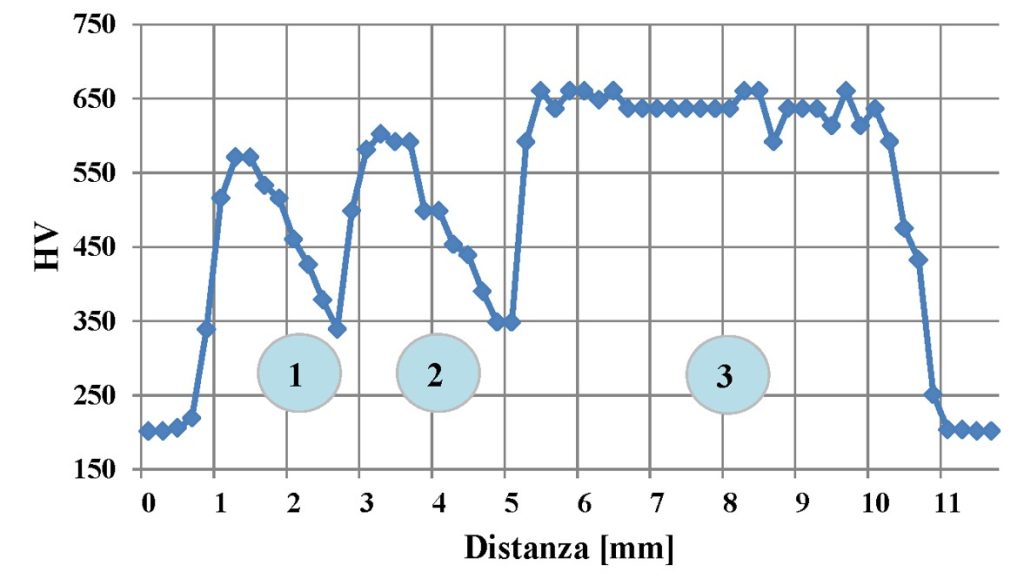
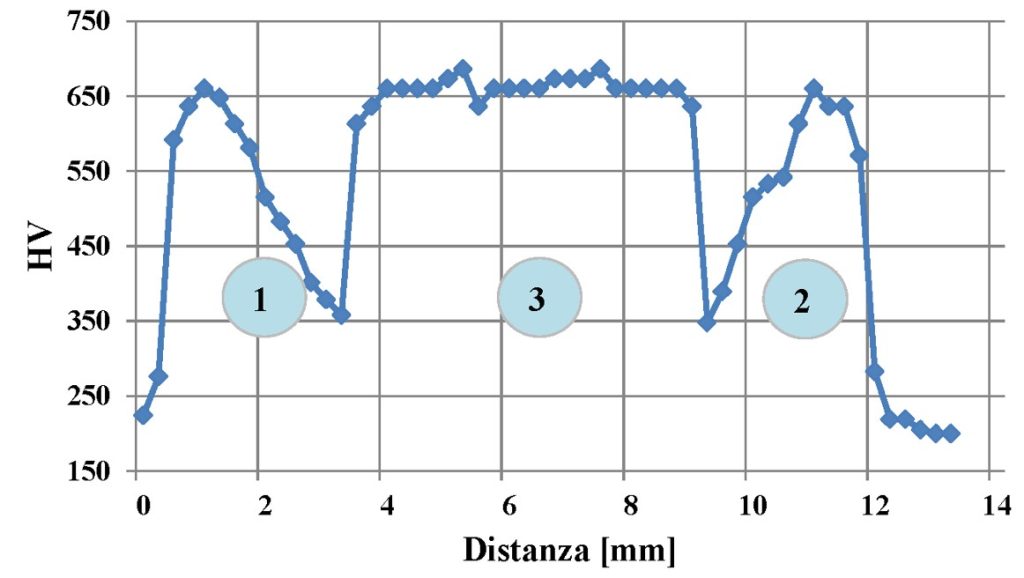
Le considerazioni enunciate finora rendono evidente come i parametri significativi in un processo di trattamento superficiale mediante laser siano numerosi e non interessino solo il fascio e le sue caratteristiche di potenza e dimensione, ma anche le strategie con cui questo viene movimentato sulla superficie. La messa a punto ottimale del processo chiama, quindi, inevitabilmente in causa la necessità di effettuare numerose prove sperimentali, volte ad individuare il set di parametri che consenta di ottenere i risultati migliori. Tale attività può diventare assai lunga e dispendiosa, soprattutto quando si ha a che fare con componenti, geometrie e materiali sempre diversi tra loro.
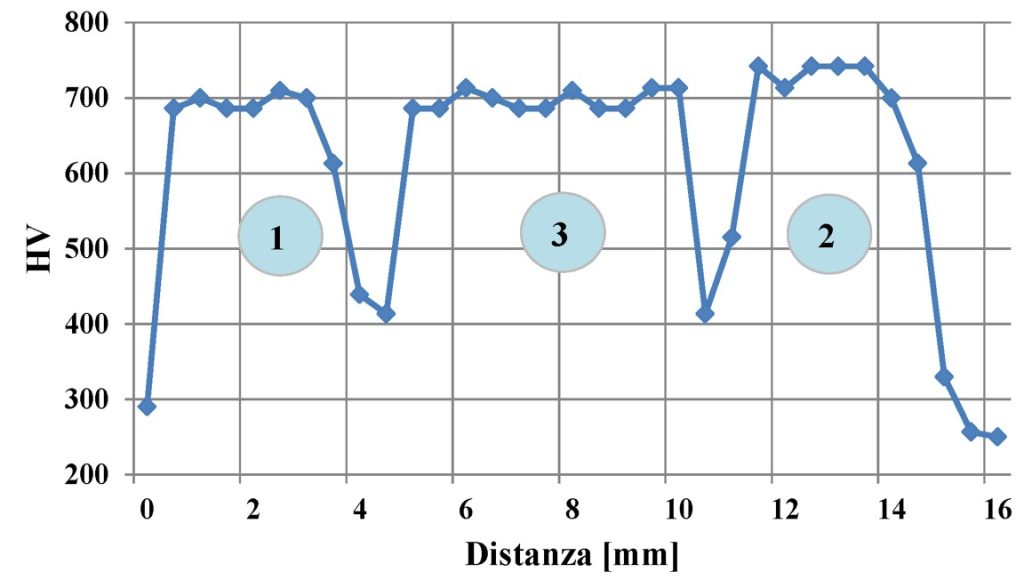
Uno strumento il quale possa aiutare a ridurre i tempi di setup, consentendo l’individuazione dei parametri ottimali riducendo le prove sperimentali al minimo, è la simulazione di processo realizzata mediante strumenti software basati sulla modellazione matematica dei fenomeni che vi risiedono alla base.
Come accaduto per numerose lavorazioni industriali, quali i processi fusori e quelli per deformazione plastica, anche le lavorazioni mediante laser possono trovare supporto dall’impiego della simulazione numerica.
A questo scopo, si è rivelato utile sviluppare codici di calcolo specifici in grado di simulare lavorazioni di microasportazione, pallinatura (shot-peening) e trattamento termico realizzati sempre attraverso l’applicazione di sorgenti laser. In particolare, il software qui discusso, per la simulazione dei trattamenti superficiali, denominato LHS (LASER Hardening Simulator), prevede di ricevere in ingresso informazioni inerenti (fig. 10):
• la geometria del pezzo, attraverso l’importazione di un modello CAD-3D, che viene opportunamente discretizzata da un “meshatore” integrato;
• il materiale con i relativi parametri fisici e la sua microstruttura;
• il percorso di movimentazione del fascio attraverso istruzioni in linguaggio ISO-base;
• i parametri relativi alla sorgente impiegata, quali la dimensione e la forma dello spot, il profilo spaziale di distribuzione della potenza, la riflettività del materiale nei confronti della radiazione emessa, la potenza impiegata;
• le posizioni di punti salienti della zona da trattare (detti “probes”) nelle quali andare a memorizzare l’evoluzione della temperatura e della microstruttura al fine di generare output grafici e testuali congeniali a comprendere i risultati del trattamento.
Una volta acquisite tutte le informazioni in ingresso ed impostate le condizioni al contorno, il computo della simulazione avviene attraverso passaggi ben definiti i quali consentono di:
• calcolare, attraverso la risoluzione dell’equazione di Fourier con il metodo alle differenze finite, il campo termico all’interno del materiale istante per istante, considerando anche la naturale variabilità dei parametri fisici del materiale stesso in funzione della temperatura;
• valutare le trasformazioni di fase che avvengono nel materiale in funzione del ciclo termico al quale gli elementi della mesh si vengono a trovare a seguito del passaggio del fascio. In particolare, in questa fase possono essere trascurati gli effetti diffusivi del carbonio (semplificazione del tutto accettabile dati i tempi estremamente ridotti nei quali avviene il ciclo termico), favorendo un calcolo più snello e veloce, oppure, attraverso la risoluzione dell’equazione di Fick, è possibile tenere in conto qualunque tipo di effetto diffusivo con grande aumento dei tempi di calcolo ma con maggiore accuratezza nei risultati.
In entrambe le modalità di simulazione, comunque, il codice tiene conto dell’effettiva microstruttura di partenza del materiale in termini sia di distribuzione delle fasi caratteristiche che della dimensione media dei grani.
Tale prerogativa è resa possibile attraverso un opportuno modulo software appositamente sviluppato, il quale, partendo da una micrografia del materiale oggetto del trattamento, è in grado di tradurla in un formato “testuale” da cui il codice riceve le informazioni sulla distribuzione delle fasi e sulle dimensioni dei grani (fig. 11) per ognuno degli elementi in cui la geometria è stata discretizzata;
• valutare l’eventuale effetto di rinvenimento in funzione di passate ravvicinate e mutuamente interagenti, tenendo conto sia dell’eventuale riaustenitizzazione della martensite precedentemente formatasi che del suo rinvenimento effettivo.
In figura 12 è mostrato il confronto tra i dati sperimentali e quelli previsti mediante la simulazione di un trattamento in due passate sovrapposte del 30% su acciaio C67 con potenza 1.8 kW, velocità di passata 1.3 m/min e diametro dello spot 6.5 mm.
Il software LHS è in grado di simulare trattamenti su ogni tipo di superficie e geometria, come mostrato in figura 13 e 14 in cui, rispettivamente, è mostrata la lavorazione di un profilo dentato e di un componente cilindrico cavo.
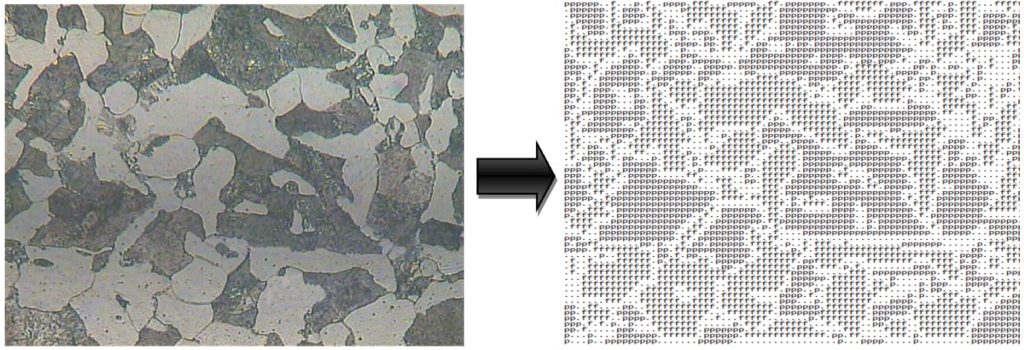
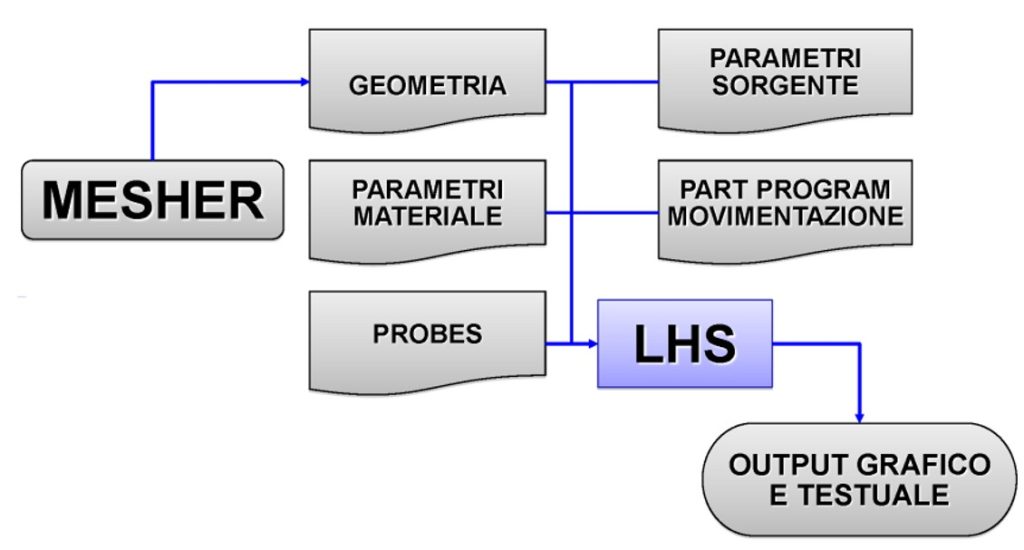
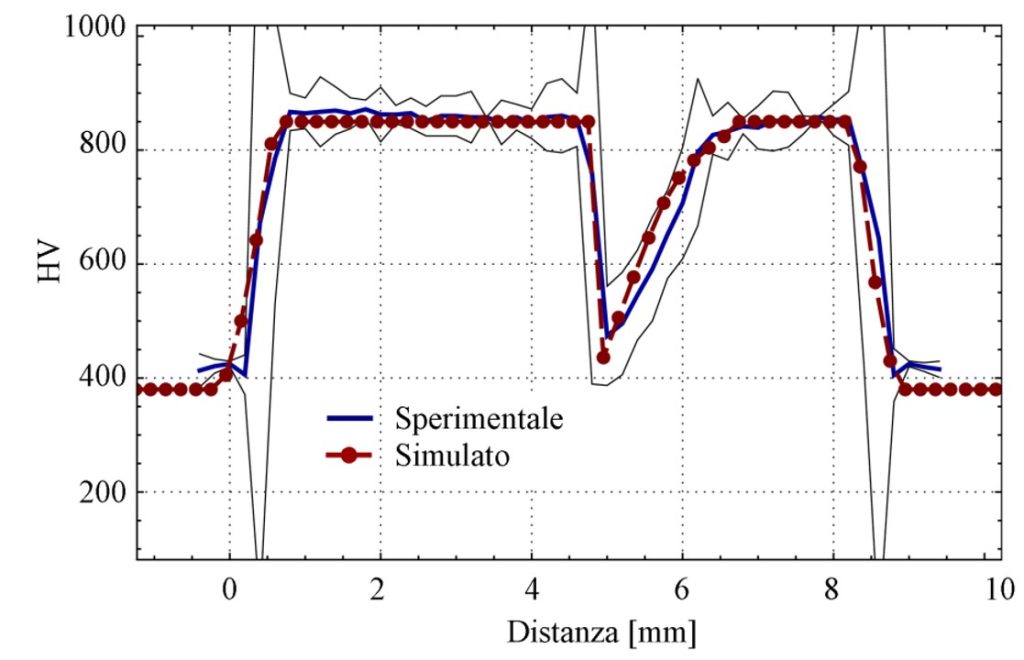
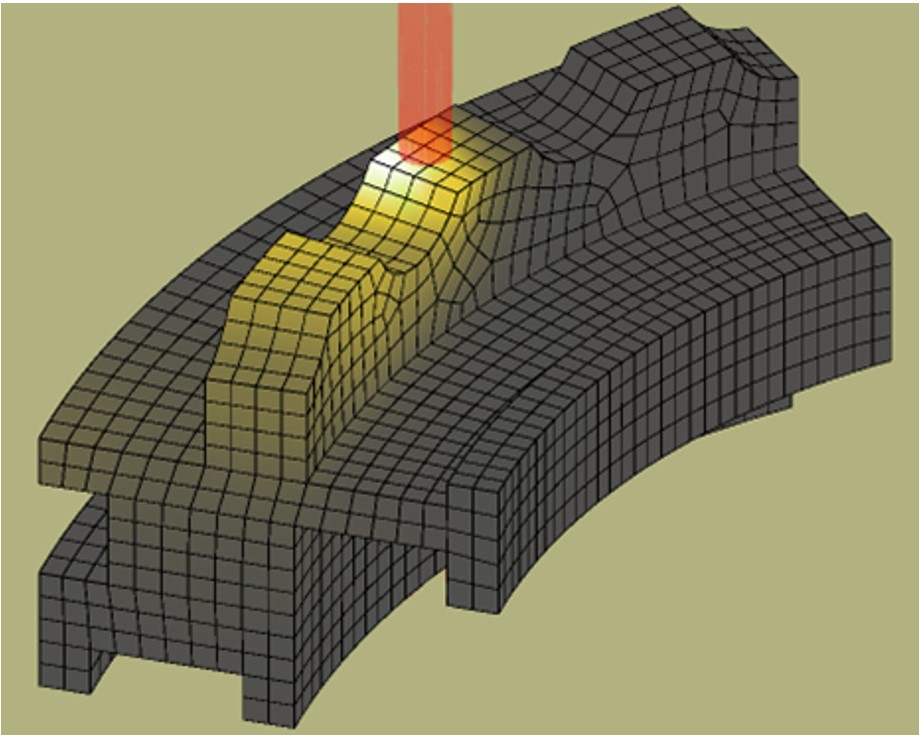
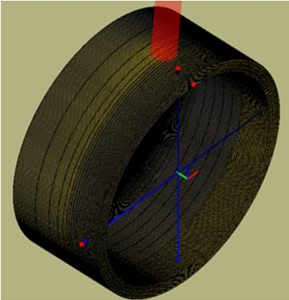