Il settore delle macchine da taglio laser per la lavorazione della lamiera si è sviluppato rapidamente negli ultimi anni, rendendo disponibili impianti sempre più performanti in grado di fornire ulteriore valore aggiunto agli utilizzatori. Come nel caso del nuovo impianto Mazak con tecnologia a diodo diretto, completo di sistema di carico-scarico e magazzino automatico, che ha dato a Siderflange ulteriore slancio in termini di capacità e qualità di processo.
Con 40 anni di attività alle spalle, Siderflange si connota quale realtà ben consolidata nell’ambito della lavorazione lamiera, proponendosi al mercato come centro di trasformazione specializzato nel medio e nel grande formato. Fondata nel 1981 a Pievesestina di Cesena (FC), l’attività inizialmente si occupa di piccole lavorazioni di ossitaglio, di cesoiatura e di piegatura, rivolte per lo più a realtà locali, per poi cogliere alcune opportunità di crescita e ampliando progressivamente nel tempo la propria struttura e il proprio raggio d’azione.
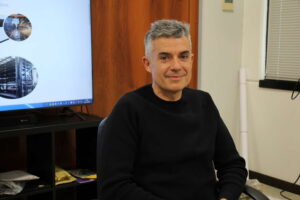
«Le dinamiche del comparto – spiega il general manager Fabio Biguzzi – e la precisa volontà di poter servire i nostri clienti con impianti e attrezzature sempre al passo con l’innovazione, hanno sempre determinato la necessità d’innovare con continuità il nostro parco macchine. Sia per migliorare capacità e qualità produttiva, sia per rendere i nostri processi sempre più competitivi».
Una ben radicata filosofia operativa, confermata anche dalla recente integrazione nel reparto di taglio di un nuovo impianto laser, un Mazak Optiplex 4020 DDL con sorgente a diodo diretto da 6 kW, con annesso sistema di carico/scarico e magazzino lamiere automatico Tekmag.
«Il nostro obiettivo – prosegue Biguzzi – è da sempre quello di riuscire a offrire un servizio a 360 gradi nella lavorazione della lamiera, quindi che comprenda non solo il taglio laser, il taglio plasma, l’ossitaglio, ma anche piega, cianfrinatura e calandratura. Per questo ci siamo dotati di un parco macchine articolato e performante, flessibile e molto polivalente. Prerogative queste ultime che ben rispecchiano il nuovo laser Mazak».
Specialisti nei grandi formati
Presso i propri stabilimenti, Siderflange è in grado di lavorare formati lamiere fino a 12000×3000 mm, in spessori che possono raggiungere i 300 mm, passando da acciai inox AISI 304 e AISI 316, agli acciai strutturali, dagli altoresistenziali, alle lamiere anti-usura, all’alluminio.
«Disponiamo a magazzino di tutta la gamma degli alto-resistenziali di SSAB, della quale siamo dal 2017 anche centro autorizzato Hardox Wareparts – precisa Biguzzi –. E a beneficiarne sono svariati settori: dal navale al comparto delle macchine da scavo e movimento terra, dal comparto strutturale a quello della meccanica in generale».
Stiamo parlando di un diversificato e frammentato portfolio clienti per i quali lo scorso anno sono state gestite oltre 8.000 commesse, con il supporto di un qualificato staff composto da una cinquantina di addetti e grazie a un’infrastruttura informatica, attiva da quasi un decennio, che assicura una gestione digitale dei processi.
«Tutte le nostre macchine – conferma Biguzzi – compreso l’ultimo laser Mazak, hanno a bordo un Pc direttamente collegato col gestionale, il cui scambio dati in tempo reale permette la tracciabilità e la rintracciabilità di tutti i particolari, nonché di seguire la commessa passo-passo. Non a caso, in Siderflange si può parlare di Industria 4.0 già da diversi anni, ovvero un approccio operativo divenuto contestualmente esigenza e opportunità ben prima della sua grande diffusione, con un sistema di controllo che abbraccia tutte le fasi di lavorazione: dall’entrata del materiale allo stoccaggio in magazzino, alle lavorazioni ed eventuali trattamenti».
Connessa in rete, come sottolineato, è anche la nuova e performante Mazak Optiplex 4020 DDL con sorgente a diodo diretto da 6 kW, macchina che Siderflange ha potuto ammirare in produzione presso la sede del costruttore nipponico, nonché confrontarne prestazioni e differenze con le proprie tecnologie a diodo diretto e a CO2.
«La qualità di taglio a diodo diretto – afferma Biguzzi – ha subito carpito la nostra attenzione; sicuramente per la finitura, che presenta una rugosità migliore, molto ma molto simile a quella del taglio a fibra. In più, abbiamo potuto verificare una grande qualità di taglio anche su lamiere particolari magari un po’ ostiche, come potrebbero essere quelle primerizzate o la lamiera sabbiata».
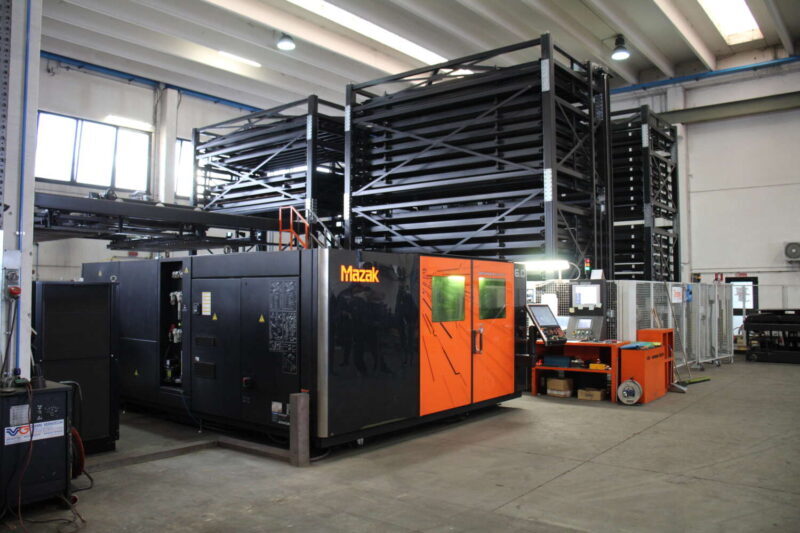
Alta qualità, alta efficienza, alte prestazioni
A garantire sulle macchine Mazak Optiplex DDL la migliore qualità delle finiture, specialmente nella lavorazione di medi e grandi spessori, è la lunghezza d’onda del laser a diodo diretto che è compresa tra un minimo di 0,94 e un massimo di 0,97 μm. Ovvero è molto più corta di quella della tecnologia fibra (compresa invece tra 1,06 e 1,08 μm) e ancor più di quella del CO2 (pari a circa 10 mm). Onde così corte migliorano il taglio ad alta velocità di lastre medio-sottili, inclusi materiali altamente riflettenti come alluminio, ottone e rame. Inoltre, possono così essere assorbite più facilmente e riescono a scaldare il materiale più in profondità. Risiede in questo la motivazione per cui il “rapporto di conversione”, cioè il rapporto tra la potenza sviluppata e quella realmente impegnata nel taglio, è all’incirca pari al 50% per il diodo diretto, al 40% per il fibra e al 10% per il CO2.
«Subito dopo l’installazione – rileva lo stesso Biguzzi – al nuovo impianto sono stati indirizzati i tagli di spessori medio grossi, cioè tutte quelle lamiere per noi fino a quel momento abbastanza critiche da eseguire con altre tecnologie di taglio. I risultati sono stati ben più che soddisfacenti. Si tenga conto che ci troviamo a processare con una certa regolarità acciai altoresistenziali, molto Hardox, molto alluminio e altrettanti acciai inox fino a 25 mm di spessore. Ultimamente abbiamo prodotto anche dei coni da 55 mm in acciaio inox ed è stata una scommessa che ci ha portato a ottimi risultati. È stato un prodotto interessante, di grande soddisfazione, che ha confermato come il nuovo Mazak ci abbia reso ancora più competitivi».
Altrettanto apprezzata in Siderflange è la citata resa, assicurata dalla tecnologia a diodo diretto, nonché la manutenzione è ridotta al minimo, con dati oggettivi confermati direttamente sul campo, visto l’articolato parco macchine.
«Senza dimenticare – aggiunge Biguzzi – la facilità di utilizzo e la velocità nel cambio tipo materiali di lavorazioni».
A rendere ancore più efficiente e performante il nuovo impianto di taglio è inoltre il già citato sistema di carico-scarico e magazzino lamiere automatico Tekmag che l’officina ha deciso di connettere; e grazie al quale riesce a processare in turni non presidiati lamiere anche di 20 mm di spessore.
«Non di certo uno standard – sottolinea Biguzzi – come nemmeno lo sono i fogli di lamiera pre-sabbiati da 15 mm che riusciamo perfettamente a gestire. È indubbio come oggi come oggi sia la macchina che più delle altre stiamo sfruttando per smaltire la gran parte degli oltre 6.000 quintali di lamiera che lavoriamo mediamente ogni mese. Un risultato ottenuto grazie anche alla disponibilità del personale Mazak, resosi sempre molto disponibile e pronto nell’assistenza. È stato per noi il primo laser fibra a diodo diretto, una tecnologia totalmente nuova e disconosciuta, la cui gestione ha richiesto in alcuni casi un supporto. E devo ammettere che gli interventi sono sempre stati rapidi e risolutivi, confermando la bontà di questa nuova partnership».
Dal capitale umano al tecnologico, e viceversa
Se è vero che Siderflange investe tanto in tecnologie, è altrettanto vero di quanto tenga al capitale umano.
«Innovazione e tecnologie sono determinanti – sostiene Biguzzi – ma lo sono altrettanto le persone, con la loro qualifica e formazione alla quale guardiamo con molta attenzione».
Sono svariati da questo punto vista i corsi messi a budget annualmente a rotazione per i vari reparti, sia in produzione, sia per l’ufficio tecnico (dove sono impiegati una decina di addetti) e per l’ufficio che si dedica al nesting, da cui nasce e si dirama l’organizzazione secondo i principi della lean manufacturing.
«Ritengo la crescita il cercare di migliorarsi e di guardare al futuro puntando sull’innovazione a tutto tondo, elementi fondamentali di sviluppo», sostiene Biguzzi.
In questo contesto Siderflange ha sempre dimostrato grande lungimiranza su tutti i fronti, con una conferma che riguarda diversi ambiti, anche non direttamente produttivi. Da sempre attenta anche all’ambiente, nel 2008 ha installato sulla copertura del proprio stabilimento 6.000 mq di pannelli fotovoltaici, per una potenza di 300 kW che alimenta gran parte del fabbisogno energetico.
«Siamo inoltre stati anche tra i primi del settore in cui operiamo – conclude Biguzzi – ad acquisire la certificazione UNI EN 1090, quindi a poter fornire manufatti con marcatura CE per strutture in acciaio. Tra i prime a dotarci di un impianto di taglio laser da 8 m, di una pressa piegatrice da 10 m per 1.000 ton, di una calandra per grossi spessori in grado di lavorare 60 mm su 3 m. Il nuovo laser Mazak a diodo diretto rappresenta un ulteriore passo, al quale si aggiungerà il già programmato nuovo impianto di taglio laser da 12 m con testa Bevel in arrivo il prossimo anno. Siamo sempre alla ricerca di nuovi obiettivi per migliorarci. Un approccio che ha sempre dato buone soddisfazioni, incrementando la nostra specializzazione verso le grandi dimensioni».
Una crescita che presto si tradurrà anche in nuovi spazi produttivi, più che mai necessari, con l’ampliamento di altri 4.000 mq coperti, in aggiunta agli attuali 6.000 (sempre coperti), che darà la possibilità di migliorare ancora in termini di efficienza globale.
Il laser ideale per garantire alta produttività e ottima finitura superficiale su tutti gli spessori
La tecnologia laser a diodo diretto offre numerose possibilità d’uso, dimostrandosi adatta all’impiego in svariati settori applicativi, proprio come quelli serviti da Siderflange. Che si tratti di spessori sottili, medi o alti infatti l’impianto di taglio Mazak Optiplex DDL riesce a garantire elevata produttività unita a un’ottima finitura superficiale, sia con sorgente da 4, sia da 6 kW di potenza. Due sono infatti le versioni rese disponibili dal costruttore giapponese: la 3015 e la 4020 (la stessa scelta da Siderflange, con potenza da 6 kW), che si differenziano sostanzialmente per le dimensioni massime del pezzo lavorabile. Nel primo caso l’area di lavoro consente di caricare lamiere fino a 1525×3050 mm, nel secondo fino a 2000×4000 mm. Per ciò che concerne la velocità di traslazione degli assi X, Y e Z, si arriva rispettivamente in rapido a 120 m/min, 120 m/min e 60 m/min, rispettivamente. Dotata di testa “Multi Control Torch”, con cambio ugello automatico a 8 posizioni e controllo del diametro del fascio, la macchina utilizza il potente CN Preview G il quale, a sua volta garantisce un’accelerazione di 1,8 G. Lo stesso controllo è dotato di un’interfaccia touch screen semplificata e intuitiva, simile a quella di uno smartphone o di un tablet, con monitor da 19” a cristalli liquidi che permette massima visibilità e facilità di programmazione. E ancora: Preview G, oltre a garantire una maggiore capacità di automazione, consente di gestire la macchina (in termini di programmi di lavoro, percorsi utensili, manutenzioni, controlli, setup e così via) in tempi assai più rapidi e in maniera ben più facile rispetto al passato.
di Fabio Boiocchi e Gianandrea Mazzola