Questo studio analizza gli effetti di diversi metodi di post-processing, tra cui i trattamenti termici (HT) e la lucidatura elettrochimica (ECP), nonché la loro combinazione, sulla rugosità superficiale, sulla porosità, sulla microstruttura e, infine, sul comportamento a fatica a flessione rotante di campioni intagliati di AlSi10Mg prodotti con tecnologia LPBF
di Mario Guagliano
Con il processo di fusione laser a letto di polvere (Laser Powder Bed Fusion, LPBF), una delle più diffuse tecniche di fabbricazione additiva (AM), si possono fabbricare elementi metallici con geometrie intricate e buone precisioni dimensionali. Tuttavia, le parti realizzate con LPBF contengono diversi tipi di difetti superficiali e interni, dovuti ai complessi fenomeni legati alla fusione e solidificazione e al rapido raffreddamento del materiale. Le concentrazioni di tensioni indotte dalle anomalie superficiali possono accelerare l’innesco di cricche da fatica e la rottura per fatica. Di conseguenza, l’applicazione di trattamenti da eseguire a valle della fabbricazione diventa importante per alleviare le problematiche legati alla difettosità rispetto alla resistenza meccanica, in particolare a fatica. Oltre ai difetti superficiali, che sono intrinseci alla tecnica di produzione, anche le caratteristiche legate alla progettazione, come la complessità geometrica e la presenza di superfici sporgenti con orientamenti diversi rispetto alla direzione di costruzione, possono influenzare in modo significativo lo stato superficiale dei pezzi ottenuti con LPBF.
Considerando che la maggior parte dei cedimenti per fatica ha origine in superficie, risulta evidente l’importanza di definire correttamente il trattamento superficiale a cui sottoporre i pezzi LPBF al fine di conferire loro adeguate caratteristiche meccaniche.
Focalizzando l’attenzione su elementi intagliati o con discontinuità superficiali, trattamenti come la lucidatura elettrochimica (ECP), possono essere utilizzati per risolvere i problemi legati alle irregolarità superficiali, mentre i trattamenti termici (HT) sono utili per i ridurre e, auspicabilmente, rimuovere i difetti di massa, come la disomogeneità microstrutturale.
Poiché l’efficienza dei metodi di post-lavorazione dipende in larga misura dalla geometria dei pezzi lavorati, in questo studio ci siamo concentrati su una geometria complessa che enfatizza le problematiche prima introdotte; in particolare si sono considerati su campioni con intaglio a U e apertura molto stretta. Su questi provini, fabbricati con LPBF e utilizzando la lega AlSi10Mg, sono stati studiati gli effetti di due diversi metodi di post-lavorazione, HT ed ECP, sia singolarmente che in combinazione, sulla porosità, la microstruttura, la rugosità superficiale e le proprietà meccaniche, compresa la fatica. Il trattamento elettrochimico si è rivelato molto influente sulla modifica della rugosità superficiale dei pezzi con intaglio molto stretto, per i quali l’applicazione di altri trattamenti meccanici può essere piuttosto impegnativa. È stato inoltre riscontrato che il comportamento a fatica dei campioni intagliati è più sensibile alla rugosità superficiale che ai difetti vicini alla superficie. Il trattamento ibrido HT+ECP è risultato il più efficace per il miglioramento del comportamento a fatica, grazie alla simultanea omogeneizzazione della microstruttura, al rilassamento delle tensioni residue di trazione, alla maggiore duttilità e all’elevata modifica della rugosità superficiale.
Prove sperimentali
La Figura 1 mostra la forma e le dimensioni di un provino cilindrico con intaglio a U, con un raggio di intaglio pari a 0,25 mm e una larghezza dell’intaglio di 0,5 mm, nonché i supporti utilizzati per la fabbricazione con un sistema SLM 500 HL, che sono stati successivamente rimossi. L’influenza della rimozione dei supporti (SR) sulle proprietà dei provini ottenuti è stata valutata eseguendo questa operazione prima o dopo il trattamento termico.
La misura della porosità è stata eseguita utilizzando un approccio di analisi basato sulla elaborazione delle immagini. In primo luogo, sono state unite diverse immagini prese al microscopio ottico (OM) per coprire l’intera sezione trasversale dei campioni nell’area dell’intaglio e poi è stato utilizzato il software ImageJ per analizzare le micrografie. Nella Figura 2 sono presentate le sezioni trasversali e longitudinali di tutti i campioni, con particolare attenzione alle zone con intaglio. I valori medi di porosità ottenuti per i diversi campioni sono i seguenti: 0,61% per AB (as built), 0,59% per AB+SR+ECP, 0,55% per AB+HT e 0,58% per AB+HT+SR+ECP. È importante sottolineare che i difetti più piccoli di 10 µm non erano rilevabili. Questi risultati forniscono chiare indicazioni, suggerendo che né i processi ECP né quelli HT hanno avuto un effetto discernibile sui valori di porosità all’interno dei campioni. La presenza di porosità sub-superficiali intorno alla radice dell’intaglio e vicino alla faccia inferiore dell’intaglio potrebbe avere implicazioni per le proprietà meccaniche e le prestazioni complessive dei materiali, come dimostrato da ulteriori indagini.
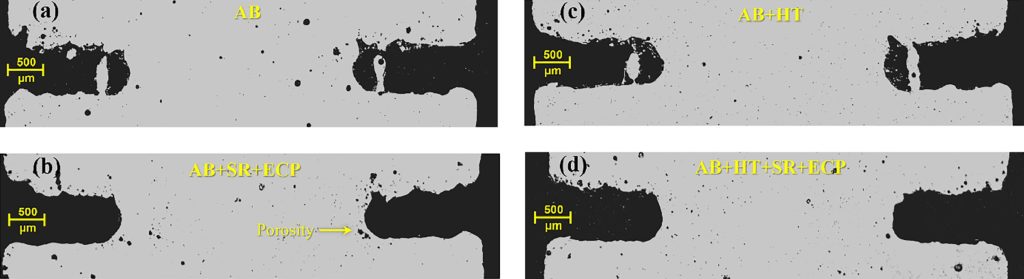
Le analisi della rugosità superficiale sono state condotte utilizzando il SEM per ottenere la morfologia della superficie e il microscopio confocale per le misure di rugosità. Per ogni misura di rugosità sono stati considerati tre percorsi diversi e si è riportato il valore medio. Il confronto qualitativo tra le superfici con intaglio verso il basso e verso l’alto ha indicato una maggiore prevalenza di anomalie superficiali nella prima delle due zone, come mostrato nella Figura 3a. I risultati dimostrano la peggiore qualità della superficie per la faccia rivolta verso il basso, con un’alta densità di difetti superficiali, seguita dalla radice dell’intaglio e poi dalla faccia superiore. Ciò è attribuito principalmente alla complessa storia termica, alle ridotte velocità di raffreddamento e alla presenza di sporgenze. I valori di rugosità superficiale di Ra = 29.30, 9.40 e 4. 78 µm sono stati ottenuti rispettivamente per la faccia inferiore, la radice dell’intaglio e la faccia superiore. La Figura 3b mostra le osservazioni confocali di diverse superfici nella regione dell’intaglio a U. Sulla faccia inferiore si notano irregolarità superficiali di circa 350 µm. Tuttavia, anomalie superficiali con un’altezza massima di 250 e 150 µm sono state osservate rispettivamente sulla radice dell’intaglio e sulle facce verso l’alto.
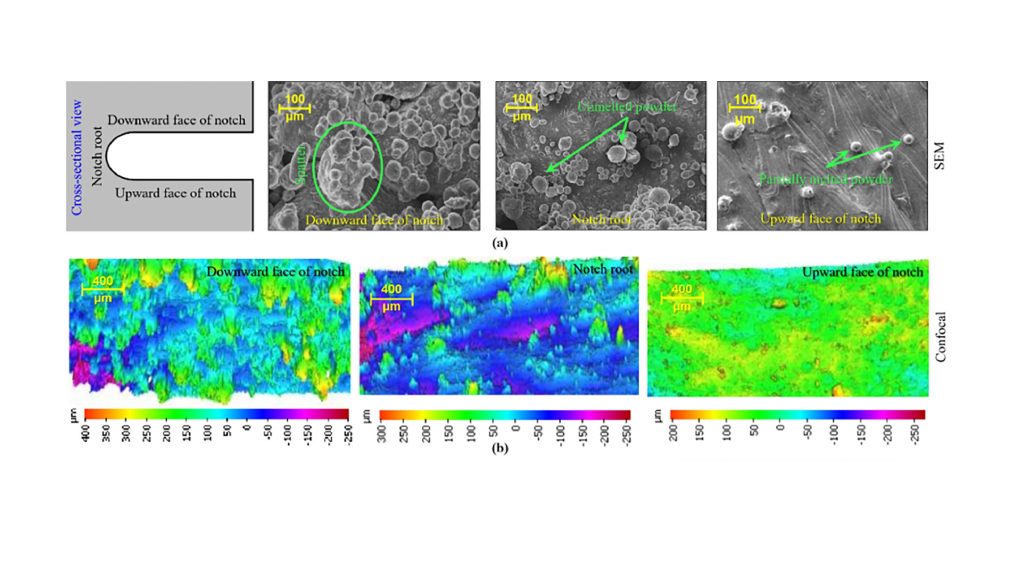
Analizzando lo stato superficiale del provino nella zona liscia (parte cilindrica al di sotto dell’area di intaglio), si è osservato che dopo l’applicazione dell’ECP si sono ottenute superfici più livellate e prive di irregolarità posizionate in modo casuale, sia sui provini grezzi che su quelli trattati termicamente. Sono stati misurati valori di rugosità superficiale di Ra = 8.37, 3.31, 8.46 e 3.21 µm per i campioni AB, AB+SR+ECP, AB+HT e AB+HT+SR+ECP, rispettivamente, dimostrando una notevole riduzione della rugosità dopo l’applicazione di ECP. Il diametro della radice dell’intaglio e la corrispondente perdita di massa dopo l’ECP sono stati misurati per tutti i set, dimostrando una modesta modifica dalla geometria originale dopo l’ECP, misurando il diametro della radice dell’intaglio pari 6.04 mm e 6.01 mm per i campioni AB+SR+ECP e AB+HT+SR+ECP, rispettivamente. Inoltre, è stata osservata una maggiore perdita di massa, pari a circa il 2,13%, dopo il trattamento ECP rispetto allo stato trattato termicamente.
Per studiare ulteriormente la microstruttura dei campioni L-PBF AlSi10Mg con intaglio a U, la regione dell’intaglio è stata analizzata con analisi EBSD sulla sezione trasversale (piano xy), come illustrato nella Figura 4. L’orientamento cristallografico in termini di figura di polo inversa (IPF), dimensione dei grani e mappe di disorientamento medio Kernel (KAM) sono stati analizzati con i dati ottenuti con EBSD. La Figura 4a presenta le mappe IPF-Z in tutti i set, dimostrando la dominanza dell’orientamento (001) dei grani a causa della crescita epitassiale dei grani lungo la direzione di costruzione (Z). I risultati ottenuti concordano con i dati disponibili in letteratura sulla formazione di grani colonnari lungo la direzione di costruzione nei metalli FCC, che porta alla formazione di una struttura a fibre (001) nello stato AM. La formazione di anomalie superficiali, tra cui polveri parzialmente e non fuse e spruzzi sulla faccia inferiore, sulla radice dell’intaglio e sulla faccia superiore dell’intaglio, nonché porosità sub-superficiali nei campioni AB e AB+HT, sono chiaramente visibili in Figura 4a. Per quanto riguarda i campioni trattati con ECP, si può notare che le imperfezioni superficiali associate alla regione dell’intaglio sono state quasi completamente rimosse, risultando in superfici altamente modificate. La Figura 4b mostra le mappe di distribuzione delle dimensioni dei grani nella radice dell’intaglio di tutti i set di campioni. I risultati rivelano che, a causa della strategia di produzione adottata, i grani relativamente più grandi si sono allungati nella radice dell’intaglio lungo la direzione di costruzione. All’interno delle aree fotografate mostrate in Figura 4b, sono state misurate aree medie dei grani di 33,2, 28,3, 44,5 e 41,2 µm2 per i campioni AB, AB+SR+ECP, AB+HT e AB+HT+SR+ECP, rispettivamente. In generale, la dimensione dei grani è aumentata dopo l’applicazione di HT, mentre un sottile strato di radice dell’intaglio che presentava grani più grandi e allungati è stato rimosso con l’applicazione di ECP, portando a una leggera riduzione della dimensione media dei grani.
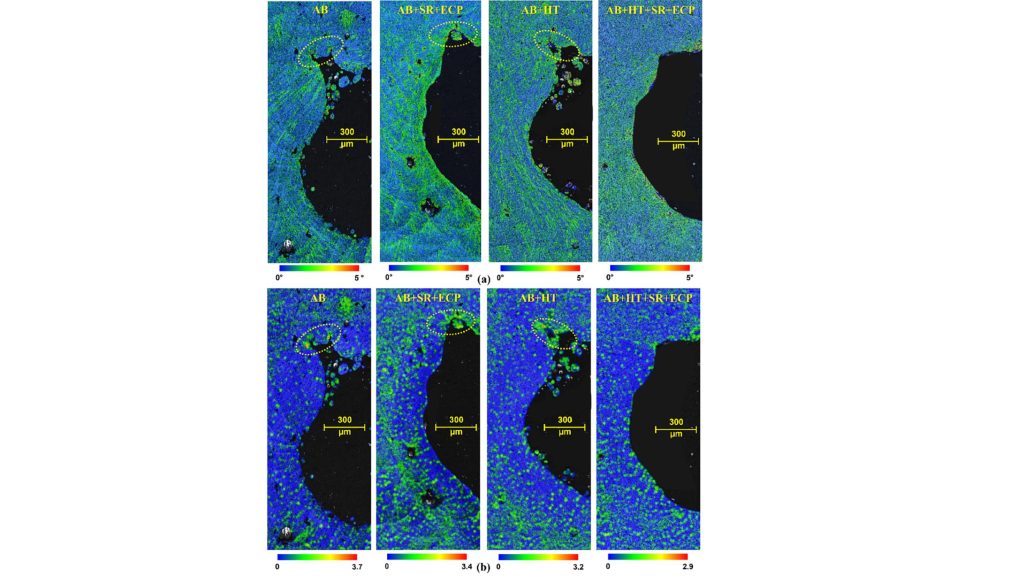
Per quanto riguarda gli effetti dell’ECP sulle proprietà meccaniche dei materiali L-PBF, questo processo chimico non influisce sulla distribuzione della durezza e delle tensioni residue né sul comportamento a trazione. Pertanto, le misurazioni della microdurezza e delle tensioni residue sono state condotte solo sui campioni AB e AB+HT. In un nostro lavoro precedente si è illustrato che dopo l’applicazione di HT, l’allungamento di LPBF AlSi10Mg è aumentato rispetto a quello senza alcun post-trattamento. Tuttavia, i carichi di snervamento e di rottura dello stato as-built si sono ridotti rispettivamente a 201 e 264 MPa, in condizioni di HT (vedi Figura 5a). Il profilo di microdurezza ottenuto per i campioni AB e AB+HT è mostrato nella Figura 5b. Si nota che lo stato di trattamento termico ha portato a una microdurezza inferiore nella condizione AB+HT a causa di cambiamenti microstrutturali.
Le distribuzioni delle tensioni residue in profondità ottenute mediante analisi diffrattometrica (XRD) per i campioni AB e AB+HT sono mostrate in Figura 5c. Si osservano le tensioni residue di trazione nella condizione as-built, con un valore medio di 40 MPa, dopo trattamento termico si rilassano e mostrano valori leggermente negativi, con un valore medio di -31 MPa, il che può influenzare notevolmente il comportamento a fatica. I risultati hanno rivelato valori residui di trazione più elevati, pari a circa 60-70 MPa a una profondità di 50-150 µm nel provino AB, probabilmente dovuti all’applicazione della sagomatura durante la fabbricazione.
La valutazione del comportamento a fatica è stata effettuata utilizzando una macchina per prove di fatica a flessione rotante a tre livelli di sollecitazione (40, 60 e 80 MPa) con un numero di cicli di run-out pari a cinque milioni, con un rapporto di sollecitazione R = -1. Per ogni serie sono stati testati tre campioni per ogni livello di sollecitazione. Inoltre, sui campioni rotti è stata condotta una frattografia mediante microscopia elettronica a scansione (SEM). I risultati per tutte le condizioni sono mostrati nella Figura 5d. Rispetto alla serie AB, si può notare che per la serie AB+HT, grazie all’omogeneizzazione microstrutturale e alla migliore duttilità, nonché al rilassamento delle tensioni residue, i campioni hanno mostrato migliori prestazioni a fatica. Tuttavia, la serie AB+SR+ECP, beneficiando del trattamento chimico, ha mostrato prestazioni a fatica migliori rispetto al set AB+HT. Questo miglioramento può essere attribuito alla drastica riduzione della rugosità superficiale, nonostante la presenza di una minore duttilità e di tensioni residue di trazione. Inoltre, si può osservare che la serie AB+HT+SR+ECP presenta le migliori prestazioni a fatica rispetto alle altre, grazie agli effeti positivi di entrambi i metodi di post-trattamento termico e chimico, come la microstruttura omogeneizzata, il miglioramento della duttilità, le tensioni residue di compressione indotte e la riduzione della rugosità superficiale. Considerando le serie trattate con ECP, sia nello stato iniziale di costruzione (AB) che in quello trattato termicamente, a un’ampiezza di sollecitazione maggiore di 80 MPa, gli effetti della modifica della superficie hanno messo in ombra l’influenza della migliore duttilità.
Infatti, a tale ampiezza di sollecitazione, il comportamento a fatica è stato migliorato rispettivamente fino a 4.3 e 5.3 volte rispetto al set AB, il che non rappresenta una differenza significativa. Tuttavia, a un’ampiezza di sollecitazione inferiore, pari a 40 MPa, gli effetti del miglioramento della duttilità sono diventati più pronunciati. La vita a fatica è stata notevolmente migliorata dall’applicazione di HT+ECP, aumentando di 255 volte rispetto alla condizione AB. Si tratta di una differenza notevole, soprattutto se confrontata con il miglioramento di 119 volte ottenuto con il solo ECP.
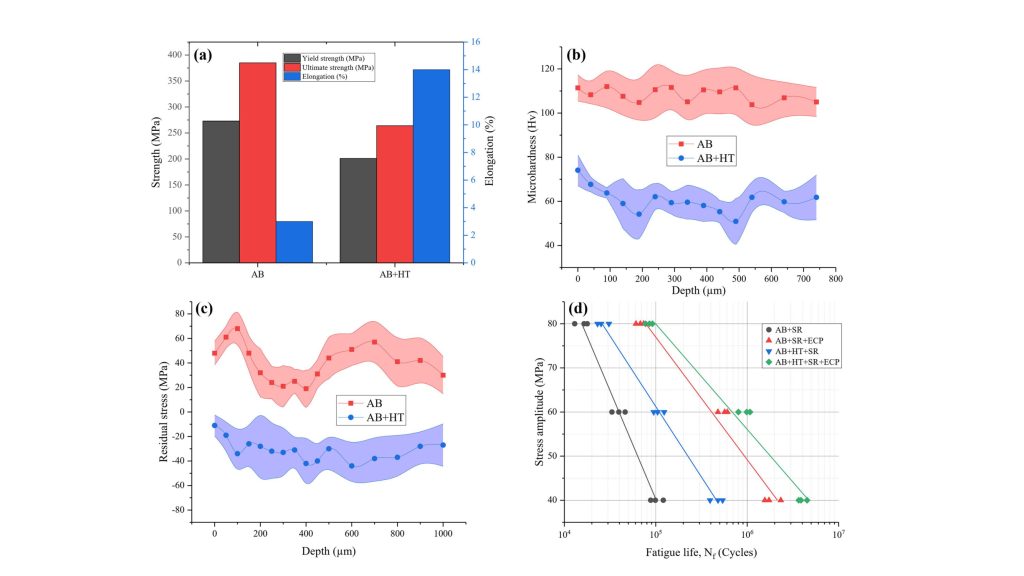
Conclusioni
In questo studio sono stati analizzati sperimentalmente gli effetti dei trattamenti separati ECP e HT, nonché della loro combinazione, sulla morfologia superficiale, sulla porosità, sulla microstruttura, sulle proprietà meccaniche e sul comportamento a fatica dei campioni L-PBF AlSi10Mg con intaglio a U. Sulla base dei risultati ottenuti, si possono trarre le seguenti conclusioni:
– L’ECP si è rivelato un efficace post-trattamento per la riduzione della rugosità superficiale per le geometrie con intaglio stretto per le quali l’applicazione di altri post-trattamenti superficiali è difficile o impossibile. La rugosità superficiale è stata ridotta a circa il 60% dopo l’applicazione di ECP.
– L’HT permette di omogeneizzare la microstruttura, rilassando le tensioni residue di trazione, che variano da un valore medio di 40 MPa nei provini as-built, a tensioni residue di compressione con un valore medio di -31 MPa.
– Sia l’HT che l’ECP hanno influito positivamente sul comportamento a fatica dei provini; il trattamento ibrido HT+ECP ha avuto la massima influenza sul miglioramento del comportamento a fatica, seguito dai soli trattamenti di ECP e HT, rispettivamente. È stato inoltre rilevato che il comportamento a fatica dei provini L-PBF AlSi10Mg con intaglio a U era più sensibile alla morfologia superficiale piuttosto che alla microstruttura e alla duttilità. Nei set trattati con ECP, sia allo stato iniziale di costruzione che a quello di trattamento termico, gli effetti della modifica della superficie hanno relativamente mascherato l’influenza di una migliore duttilità ad ampiezze di sollecitazione più elevate. Mentre ad ampiezze di sollecitazione inferiori, l’effetto della duttilità migliorata era più evidente.
Riferimento
L’articolo riprende i risultati contenuti in:
Maleki et al., Fatigue performance of U-notched additively manufactured AlSi10Mg parts: The effects of chemical and thermal post-treatments, Additive Manufacturing Letters, Volume 7, December 2023, 100175