Viene presentato un nuovo concetto di utensile per il miglioramento delle prestazioni meccaniche delle superfici degli ingranaggi, basato su un adattamento della rullatura profonda del piede dente che avviene durante il processo di skiving degli ingranaggi.
Lo skiving degli ingranaggi è noto essere un processo manufatturiero altamente produttivo. Poiché gli ingranaggi aventi modulo piccolo richiedono poco spazio per l’installazione nella scatola e generano, in genere, poche perdite di potenza dipendenti dal carico, essi risultano particolarmente adatti ai moderni sistemi di trasmissione. Nell’ambito della richiesta di ingranaggi sempre più efficienti e densità di potenza sempre maggiore, le nuove soluzioni devono trasmettere carichi sempre più elevati. Questo requisito può essere soddisfatto generando meccanicamente tensioni residue di compressione che aumentino la resistenza a flessione.
Gli sforzi residui, assieme a una buona finitura superficiale che minimizza l’effetto micro-intaglio, permettono di aumentare significativamente la resistenza a fatica. Tuttavia, il raccordo al piede, specie negli ingranaggi aventi moduli piccoli, limita le dimensioni dei mezzi impiegati per la pallinatura. Nel seguito viene presentato un nuovo concetto di utensile per il miglioramento delle prestazioni meccaniche delle superfici, basato su un adattamento della rullatura profonda del piede dente che avviene durante il processo di skiving degli ingranaggi. Si è sviluppata una simulazione per calcolare la traiettoria di contatto ed i parametri per l’ottimizzazione del processo e dell’utensile. Successivamente, il sistema di utensili è stato testato praticamente in diverse condizioni di velocità e avanzamento. Il nuovo processo ha mostrato un significativo potenziale per una produzione altamente produttiva di ingranaggi con prestazioni maggiorate.
Introduzione
Le nuove soluzioni di mobilità richiedono unità di azionamento sempre più potenti con proprietà vibro-acustiche sempre maggiori. Grazie all’elevata densità di potenza e alla buona efficienza anche con rapporti di trasmissione elevati, nei nuovi progetti di gruppi propulsori per aviazione e mobilità elettrica spesso vengono impiegati riduttori epicicloidali [1, 2].
Gli ingranaggi a modulo ridotto riducono le perdite di potenza dipendenti dal carico [3]. Le prestazioni di questi ingranaggi sono in gran parte determinate dalla resistenza al piede del dente. Per gli ingranaggi esterni, è noto come la pallinatura del piede del dente aumenti la capacità di carico dal 42% al 66% [4].
Per gli ingranaggi a modulo ridotto, tuttavia, il problema della bassa profondità di penetrazione dell’effetto della pallinatura rappresenta ancora una sfida irrisolta. Ciò limita considerevolmente la capacità di carico a flessione degli ingranaggi a piccolo modulo che, in altre condizioni, potrebbe essere aumentata mediante pallinatura.
Un altro metodo per aumentare la resistenza alla fatica è la laminazione profonda. Nella laminazione profonda, la superficie è rinforzata da un elemento volvente caricato [5] che porta ad una plasticizzazione locale del materiale ed alla formazione di tensioni residue di compressione anche a profondità maggiori rispetto a quelle raggiungibili dalla pallinatura [6]. Tuttavia, il metodo viene utilizzato principalmente per componenti assialsimmetrici. Il trasferimento di questa tecnologia agli ingranaggi è stato studiato solo a livello teorico [7, 8]. Il processo di laminazione profonda viene eseguito utilizzando strumenti complessi e richiede un ciclo di lavorazione dedicato. Un’integrazione di tale processo direttamente nel ciclo produttivo attuale degli ingranaggi potrebbe essere possibile se combinato con lo skiving ed opportunamente adattato. Ciò avrebbe del potenziale per una manifattura altamente produttiva e flessibile. In tal senso, questo lavoro mira allo studio della combinazione della cinematica dello skiving + laminazione profonda in un nuovo processo per il trattamento meccanico delle superfici.

Lo skiving degli ingranaggi
Lo skiving è diventato, negli ultimi 15 anni, uno dei processi produttivi più utilizzati per la produzione di ingranaggi. Combina un’elevata produttività con un alto grado di flessibilità, mantenendo allo stesso tempo bassi i costi di produzione.
Lo skiving degli ingranaggi è un processo con assi incrociati in cui l’utensile ed il pezzo ingranano continuamente. Il potenziale per la lavorazione sia di sgrossatura, sia di finitura di ingranaggi con elevate produttività, in particolare per ingranaggi interni e ingranaggi con errori di passo minimi, ha portato ad una rapida diffusione della tecnologia nella produzione di componenti per trasmissioni per propulsori elettrici aventi tipicamente ingranaggi a modulo ridotto. Il calcolo dettagliato e la caratterizzazione del processo e dello strumento sono spiegati in [9]. Per la simulazione dei processi geometrici è disponibile una soluzione open source: OpenSkiving [10].
Trattamento superficiale all’avanguardia
Hoffmeister ed Hermes hanno dimostrato come un aumento della resistenza alla fatica fino al 65% sia per gli ingranaggi pallinati [11]. Ciò è giustificato dalle tensioni residue di compressione tra -900 e -1200 MPa ad una profondità fino a 50 µm. Tuttavia, gli ingranaggi a modulo ridotto limitano il diametro massimo del media da utilizzare per la pallinatura. Secondo [12], la profondità di penetrazione delle tensioni residue di compressione da pallinatura su S330 (0,8 mm) e S110 (0,3 mm) risulta raggiungere, utilizzando gli stessi parametri di Hoffmeister ed Hermes, solo profondità 0,1 mm (vs. 0,2 mm). Quando si effettua la pallinatura di provini induriti e intagliati, l’effetto della profondità raggiungibile viene ulteriormente ridotto con l’aumentare della durezza [13].
Rispetto alla pallinatura, la laminazione profonda è caratterizzata da un maggiore effetto penetrante delle tensioni residue di compressione [6]. Oltre all’introduzione di sollecitazioni residue, durante la laminazione profonda la superficie viene anche levigata [14]. Questo processo è attualmente utilizzato soprattutto per componenti assialsimmetrici [15, 16]. Il primo studio di applicazione della laminazione profonda agli ingranaggi è da attribuire a Liebisch [7]. Il piede del dente degli ingranaggi cilindrici è stato trattato, su un solo lato, utilizzando rulli speciali in una configurazione sperimentale appositamente sviluppata. Sebbene attraverso la laminazione profonda sia stato possibile ottenere un aumento delle tensioni residue di compressione, la resistenza a fatica è risultata minore. Un singolo passaggio di laminazione ha portato ad aumenti contenuti; con dieci passaggi, gli effetti sono stati invertiti. In [8] viene mostrato un concetto simile, in cui però il dente viene laminato in profondità su entrambi i lati. Inoltre, il piede del dente viene rinforzato tramite un sistema a dieci rulli disposti uno dietro l’altro mentre l’ingranaggio è bloccato da un sistema autocentrante. Attraverso tale lavorazione, la sollecitazione nominale permanentemente sopportabile dal piede del dente è stata aumentata del 12,5% rispetto agli ingranaggi pallinati. Non viene fatta alcuna dichiarazione circa le limitazioni del sistema di utensili in relazione a moduli piccoli, ingranaggi interni o angoli dell’elica più grandi.
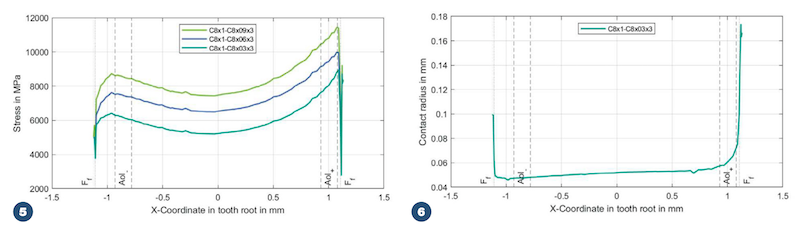
di contatto ao con diametro della punta del perno d=1,60 mm.
Obbiettivo
L’obiettivo principale di questo lavoro è mostrare il grande potenziale di un adattamento della laminazione profonda nel processo di skiving degli ingranaggi per il trattamento meccanico dei piedi dei denti. Poiché l’utensile deve compensare le deviazioni geometriche dovute alle distorsioni della tempra, questo è progettato con controllo della forza utilizzando molle a tazza. Su questa base è sviluppata una simulazione per meglio comprendere la condizione di contatto ed identificare strategie di processo adeguate. Dopo la valutazione basata sulla simulazione, si è passati alla validazione pratica mediante la caratterizzazione delle superfici trattate attraverso topografie e micro sezioni.
Concetto di nuovo utensile per la lucidatura nella cinematica della smussatura degli ingranaggi
Nello skiving degli ingranaggi, la traiettoria di contatto (Figura 1a) dipende soprattutto dall’angolo di incrocio degli assi e dal diametro dell’utensile. Poiché lo scopo è quello di integrare l’utensile di lucidatura nell’utensile da taglio, l’angolo ed il diametro vengono scelti analogamente al processo di skiving. L’utensile contiene un perno con un diametro definito per la lucidatura; quello dell’utensile può essere regolato (Figura 1b). Le molle a tazza vengono utilizzate per compensare le deviazioni geometriche dell’ingranaggio. Inoltre, la scelta della tecnica di montaggio delle molle a tazza è libera; in linea teorica risulta possibile impilare fino a quattro molle a tazza. Viene utilizzato un ingranaggio elicoidale esterno, β=28,5°, con modulo normale m=1,75 mm e diametro primitivo d=45,8 mm.
Simulazione del processo di lucidatura
Poiché la lucidatura viene eseguita direttamente sfruttando la cinematica dello skiving, le condizioni di contatto sono complesse. Per meglio comprenderne tutti gli aspetti, è stata sviluppata una simulazione basata su OpenSkiving. Questo calcolo è adattato ad un’analisi del contatto in cui viene analizzata l’interazione tra l’utensile ed il vano tra i denti. Pertanto, devono essere studiate le traiettorie di contatto, le velocità, gli angoli e altri parametri caratteristici.
Come prima cosa è stata scritta una procedura per determinare il diametro della punta del perno e le combinazioni di molle da utilizzare. Successivamente è stata determinata la corsa richiesta per i diametri selezionati delle punte dei perni in modo che l’utensile inizi e termini il contatto sul diametro di piede dFf.
Considerando la corsa della molla in combinazione con gli angoli di contatto, sono state simulate diverse combinazioni (di molle). È stata anche condotta un’ottimizzazione iterativa finché lo strumento non ha raggiunto le forze massime possibili nel punto di interesse (Pol). Il Pol per la lucidatura è specificato nel punto di massima sollecitazione sotto carico del piede del dente in corrispondenza della retta tangente a 30°, sulla base di una simulazione 2D-FEM preliminare.
Quando l’attrito è predominante, il punto di massima sollecitazione si trova davanti al punto di contatto nella direzione del movimento. Il Pol è stato quindi esteso ad un’Area di Interesse, o Aol (Figura 2).
Per la progettazione dell’utensile, sono calcolati (mediante simulazione) la pressione hertziana (vedere [17, 18, 19]) e il raggio di contatto risultante tra l’utensile e il pezzo.
A questo punto si libera il perno e si stabilisce l’equilibrio delle forze in funzione dell’angolo di contatto φ, (Figura 3). FF è la forza generata dalle molle, FK è la forza di contatto sul perno. La forza centrifuga FZf è stata trascurata in luce della massa ridotta del perno mpin ≈ 15 g, della bassa velocità di rotazione di 200 1/min e della conseguente bassa velocità periferica. Lo stesso vale per la forza d’inerzia FT che si genera durante l’entrata e l’uscita.
Il modello di attrito utilizzato è quello di Coulomb con coefficiente di attrito µ = 0,1, valore tipico per l’accoppiamento di materiali lubrificati acciaio-acciaio. La forza di attrito FR viene calcolata moltiplicando la forza normale FN nella direzione x e il coefficiente di attrito µ.
Come descritto, viene valutata l’influenza del diametro della punta. Il diametro della punta influisce sulla corsa richiesta, (Figura 4). Poiché l’angolo di contatto raggiunge quasi 80° a Ff, la forza della molla deve essere bassa. La forza dovrebbe essere elevata nell’Aol; uno spostamento troppo elevato porta ad una forza massima al piede del dente.
Entrambi i raggi più grandi non soddisfano i requisiti, così come i raggi troppo piccoli. Questo porta a tempi di lavorazione antieconomici a causa delle velocità di avanzamento inferiori. Pertanto, viene scelto un diametro della punta di 1,60 mm.
Dopo aver determinato il diametro della punta dell’utensile, viene analizzato il pacchetto di molle a tazza. Nel contatto sono state calcolate le sollecitazioni hertziane (Figura 5). I valori raggiungono un massimo all’ingresso dell’utensile, che risulta pari a 9000 MPa anche per la combinazione di molle più flessibili. Questo valore sale oltre 11000 MPa all’aumentare del numero di molle a tazza.
Considerando i valori comparativi della sollecitazione massima calcolati con le formule hertziane [15, 16, 20], le prove sono state effettuate con la combinazione di molle più morbida C8x1-C8x3-C8x3-C8x3, in breve C8x1-C8x3x3.
La Figura 6 mostra il raggio di contatto hertziano per la combinazione di molle selezionata. Poiché il fianco del dente sopra Ff è convesso e i raggi di contatto risultano maggiori sebbene le forze di contatto siano inferiori. A causa del raggio quasi costante al piede del dente, quello di di contatto cambia solo a causa della forza di contatto leggermente decrescente.
Ancora una volta, a causa dell’attrito nel sistema, il raggio di contatto risulta maggiore all’ingresso dell’utensile rispetto all’uscita. Nell’Aol+ il raggio ao è compreso tra 0,056 mm e 0,071 mm, nell’Aol- il valore è solo 0,048 mm. Poiché nella scelta dell’avanzamento è determinante il raggio più piccolo, per l’ulteriore selezione si assume questo valore.
Prima della lucidatura, gli ingranaggi sono stati tagliati mediante skiving. Ulteriori informazioni sulla configurazione e sul processo possono essere trovate in [21]. Per la lucidatura è stata utilizzata la stessa cinematica del processo di skiving. Il materiale utilizzato è un acciaio 16MnCr5 (1.7131). La lucidatura è stata eseguita allo stato di materiale non indurito. La macchina sperimentale è una Sonder Index V300, ottimizzata per la lavorazione degli ingranaggi.
Dopo la pre lavorazione è stata effettuata la lucidatura. A tale scopo, è stato installato il prototipo. In precedenza, le molle a tazza desiderate venivano integrate nel sistema e il diametro dell’utensile veniva impostato su un pre-setting utensile. Dopo l’installazione, è stata validata la curva caratteristica della molla calcolata per via teorica. Il perno, in carburo di tungsteno K30, è stato cambiato dopo ogni ingranaggio lavorato senza presentare però alcuna usura.
Basato sul diametro di contatto simulato, l’avanzamento assiale è stato scelto per ottenere una sovrapposizione (teorica) così da aumentare il numero di lucidature fino a 8 volte (Tabella 1). L’utensile installato e gli vani tra i denti con diverse condizioni di lavorazione sono illustrati nella Figura 7.
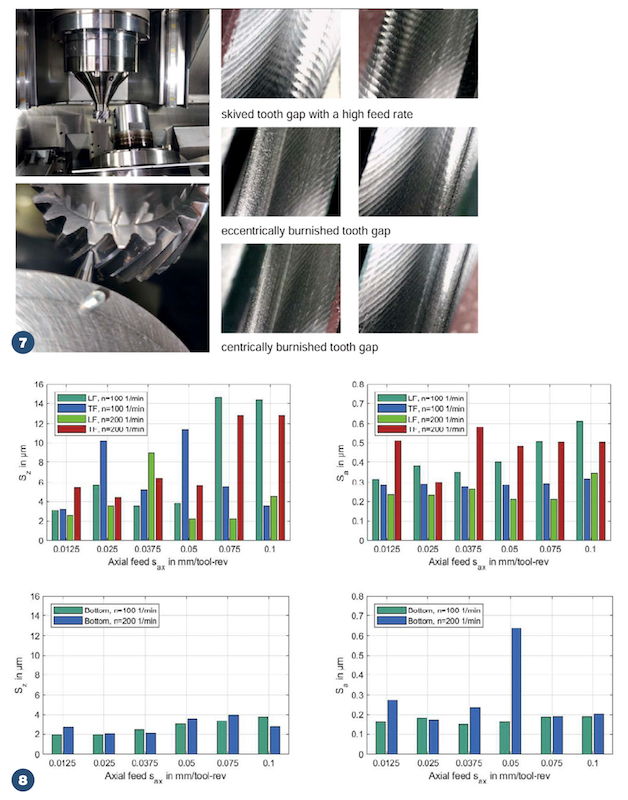
Risultati
Rugosità
I risultati della valutazione della rugosità superficiale sono riassunti nella Figura 8. Poiché l’accessibilità al punto di misura poteva essere resa possibile solo rimuovendo segmenti di dente, la rugosità è stata misurata (otticamente) solo nei vani tra i denti. Pertanto non è possibile indicare l’incertezza della misura. Tuttavia, una valutazione della rugosità superficiale è meno soggetta a errori rispetto alla valutazione con profili bidimensionali. I valori della rugosità nell’Aol sono mostrati in alto in Figura 8, i valori al piede del dente in basso.
Le scale dei rispettivi parametri di altezza (sinistra SZ, destra Sa) sono mantenute fisse per una migliore comparabilità. All’interno della figura, l’avanzamento assiale aumenta da sinistra a destra. L’andamento generale della rugosità superficiale in funzione dell’avanzamento assiale è visibile nel Pol. Tuttavia l’andamento della rugosità varia a seconda della velocità di rotazione e del lato su cui viene effettuata la relativa misurazione. Si osserva una chiara tendenza per l’entrata dell’utensile ad una velocità di 100 1/min. SZ, aumenta di un fattore 4, Sa raddoppia da 0,3 a 0,6. Sul lato d’ingresso, a questa velocità SZ, fluttua mentre Sa è costante (0.3).
Il valore di SZ si comporta in modo opposto con una velocità utensile aumentata a 200 1/min. A 200 1/min, infatti, il valore misurato su TF (ndr. fianco posteriore) oscilla, mentre su LF (fianco anteriore, ndr) il valore peggiora con l’aumentare della velocità di avanzamento assiale da ca. 5 a 13 µm. La misurazione di Sa dà come risultato (su TF) valori simili a quelli con una velocità di 100 1/min. Sul lato uscita utensile (LF) il valore è permanente a ca. 0,5 µm.
Al piede del dente la rugosità è minore rispetto alla zona attorno al Pol. Ciò è dovuto ai diametri di contatto maggiori rispetto a quelli simulati e alla conseguente elevata sovrapposizione dei singoli overroll. La differenza massima tra valori di SZ, è di soli 2 µm con un avanzamento di 0,0125 mm/giro ed assume un valore massimo di 4 µm con un avanzamento di 0,1 mm/giro. Anche la media aritmetica Sa è molto bassa, inferiore a 0.3 µm, con un valore anomalo (outlier).
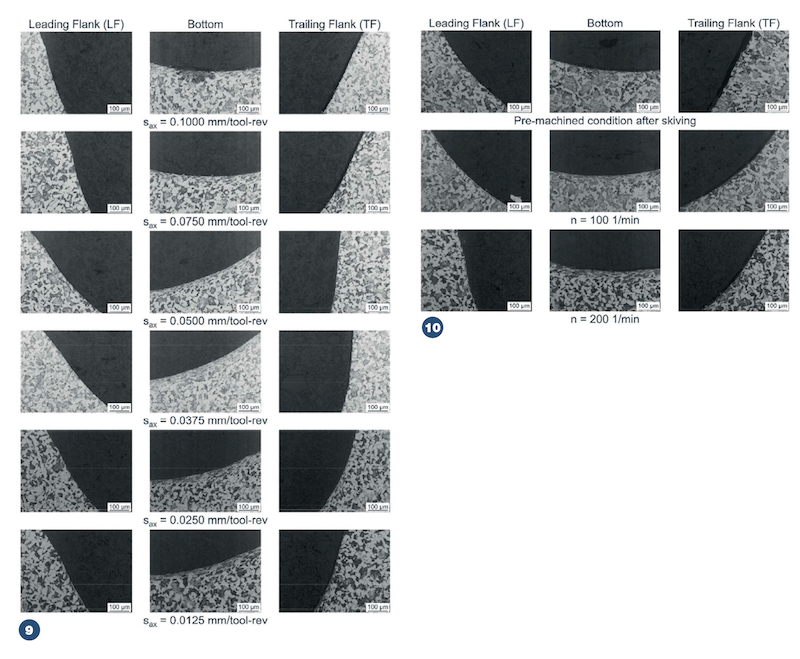
Microsezioni
La Figura 9 mostra l’andamento del cambiamento microstrutturale dovuto alla lavorazione in funzione dell’avanzamento assiale selezionato. Nelle immagini mostrate la velocità dell’utensile era di 200 1/min.
L’immagine a destra mostra la zona di ingresso dell’utensile (fianco posteriore, TF), al centro la radice del dente e l’immagine a sinistra mostra la zona di uscita dell’utensile (fianco anteriore, LF). A destra le immagini della zona ingresso utensile. Con una velocità di avanzamento di 0,1 mm/giro utensile non si nota alcuna influenza sulla microstruttura. I primi grani deformati sono visibili sul bordo inferiore dell’immagine con una velocità di avanzamento di 0,05 mm/giro utensile.
Un effetto di maggiore profondità della lucidatura può essere osservato ad una velocità di avanzamento ancora più lenta e già pari a 20 µm con una velocità di avanzamento di 0,0125 mm/giro utensile. Uno sviluppo simile della deformazione del grano può essere visto nelle immagini dell’uscita dell’utensile (colonna di sinistra).
In queste immagini è da sottolineare l’accumulo materiale, riconoscibile come un piccolo picco. Ciò si verifica già con velocità di avanzamento di 0,1 mm/giro utensile. Si può osservare un aumento dell’effetto di profondità, ma meno pronunciato rispetto all’entrata dell’utensile. Pertanto, è possibile affermare che la deformazione dei grani avvenga solo fino ad una profondità inferiore al 10 µm. L’influenza sulla zona marginale è particolarmente marcata alla base del dente. Già con una velocità di avanzamento di 0,1 mm/giro utensile si ottiene un effetto di profondità di ca. 30 µm, e i grani appaiono fortemente deformati.
Con velocità di avanzamento inferiori aumentano la deformazione e l’effetto di penetrazone in profondità. Alla velocità di avanzamento più lenta di 0,0125 mm/giro utensile, i grani si deformavano in lunghe strisce trafilate, l’effetto scende fino ad profondità di ca. 50 µm. La differenza tra la deformazione e l’effetto di profondità è marginale alle velocità di avanzamento di 0,0375, 0,0250 e 0,0125 mm/giro utensile. Anche in caso di grandi distorsioni della microstruttura non si notano rotture, crepe o altri danneggiamenti.
Le micrografie con diverse velocità dell’utensile e avanzamento assiale costante sono mostrate in Figura 10. La microstruttura dopo lo skiving è mostrata nella prima riga. Nella foto in alto a destra sono visibili le rotture del grano dovute alla prelavorazione. Questo danno allo strato superficiale, che si manifesta come micro intagli, generalmente riduce la resistenza alla fatica. Le altre immagini mostrano uno sviluppo simile della microstruttura influenzata sia dalla velocità che dall’avanzamento. I grani al piede del dente vengono deformati meno durante il processo di lucidatura con una velocità dell’utensile di 100 1/min che con una velocità crescente. Tuttavia, l’aumento tra 200 e 400 1/min è inferiore a quello tra 100 e 200 1/min. L’effetto di profondità è di circa 30 µm alla velocità di 100 1/min e fino a 50 µm al doppio della velocità.
Nella zona marginale la variazione della microstruttura è minore in funzione delle velocità di 100 e 200 1/min. Pertanto, ad una velocità di 100 1/min, l’area di deformazione del grano è inferiore a 10 µm, ad una velocità di 200 1/min, la profondità di deformazione arriva fino a 20 µm.
Il forte aumento della deformazione all’uscita dell’utensile a 400 1/min è evidente dalla fotografia a sinistra nella Figura 10. Il materiale è deformato in modo inaccettabile; la superficie risulta gravemente danneggiata.
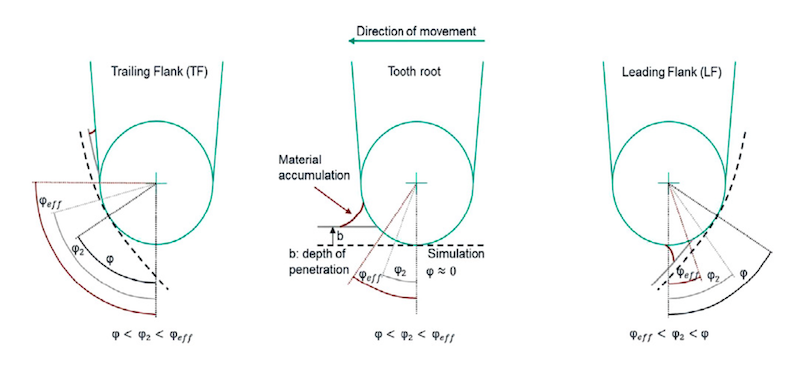
Discussione e valutazione
In [7, 22] sono stati identificati problemi dovuti a gradienti di sforzo molto elevati. In alcuni casi, questi hanno causato solo uno spostamento del cedimento, ma non un numero maggiore di cicli di carico nella prova di resistenza alla fatica. Questi gradienti di sollecitazione si verificano durante i trattamenti nella transizione tra la superficie lavorata e quella temprata. Sfortunatamente, a causa della mancanza di misurazioni delle tensioni residue, non è possibile effettuare alcuna analisi in questo lavoro.
Aumentando la forza nell’area di entrata e uscita dell’utensile, è possibile introdurre tensioni residue costanti nei vani tra i denti. Tuttavia, così fanceno, esiste il rischio di aumentare il gradiente di sollecitazione. Inoltre, una forza crescente aumenta l’accumulo o la deformazione del materiale all’ingresso e all’uscita dell’utensile. Ciò aumenta l’effetto di intaglio locale.
L’influenza dei gradienti di sollecitazione sulla durata in combinazione con l’effetto intaglio dovuto all’ingresso dell’utensile o al di materiale “appuntito” all’uscita dell’utensile richiede ulteriori indagini.
L’angolo di contatto tra la punta del perno di lucidatura e la superficie è inferiore a quello calcolato nella simulazione a causa del comportamento elasto-plastico del materiale. A causa della forza di contatto, la punta del perno penetra nel materiale, determinando un angolo di contatto più piccolo φ2.
L’attrito esistente tra il perno e la superficie del campione induce l’accumulo di materiale del provino da laminare in profondità (nella direzione del movimento) davanti al perno. Ne risulta un nuovo angolo di contatto effettivo φeff, che è inferiore all’angolo φ calcolato nella simulazione. Di conseguenza anche l’attrito nella guida viene ridotto, poiché la componente x della forza è inferiore a causa del minore angolo di contatto. Questa relazione spiega la minore influenza della microstruttura nell’area di ingresso dell’utensile.
L’angolo di contatto φ all’uscita dell raccordo di piede del dente nella simulazione si avvicina a 0°. Anche questo valore non corrisponde alla realtà, poiché la punta del perno penetra e davanti al perno si va a formare un accumulo di materiale in direzione del movimento. Ciò si traduce in un angolo di contatto maggiore, che porta ad un maggiore attrito nei cuscinetti del perno e quindi all’applicazione di una forza di contatto maggiore.
Gli accumuli di materiale davanti alla punta del perno provocano effetti opposti sul lato di uscita rispetto a quello di entrata. All’ingresso, l’angolo di contatto aumenta e, quindi, una forza maggiore viene trasmessa dal perno alla superficie del campione. Maggiore è la quantità di materiale accumulata, maggiore diventa l’angolo effettivo e maggiore è la quantità di materiale spostata dalla forza crescente. Inoltre, lo spazio per il materiale spostato tra il perno e la superficie del campione (Figura 11 a sinistra) è limitato. Dalla crescente influenza della microstruttura nelle micrografie si può concludere che gli accumuli di materiale crescano all’aumentare della velocità dell’utensile.
Gli effetti osservati con gli ingranaggi lavorati sul tenero diminuiranno in presenza di materiale indurito. A causa dello strato superficiale cementato e, quindi, della maggiore resistenza, la punta del perno solitamente non penetra così profondamente nel materiale, ma leviga preliminarmente i picchi di rugosità. Pertanto non è previsto un grande spostamento di materiale durante la lavorazione e l’angolo di contatto calcolato nella simulazione risulterà più realistico per gli ingranaggi temprati.
Conclusioni
Lo scopo del lavoro era quello di dimostrare la fattibilità della lucidatura del piede del dente sfruttando la cinematica del processo di skiving. Un diametro di contatto maggiore durante la lavorazione ha permesso di ottenere una qualità superficiale molto elevata. Ciò si ottiene non solo al piede del dente, ma anche nell’AoI. Questo riduce l’effetto intaglio causato dalle micro fessure e, quindi, ostacola l’innesco di cricche.
La misura in cui la lavorazione meccanica provoca effetti di chiusura della cricca dopo la nucleazione, grazie alle tensioni residue di compressione nel Pol, può essere valutata solo con i risultati della misurazione delle tensioni residue. Tuttavia, durante il rodaggio del sistema di utensili sono emersi non solo numerosi problemi, ma i risultati ottenuti dai test dimostrano anche la necessità urgente di ulteriori ricerche in tale ambito. In primis, l’obiettivo di avere una simulazione affidabile è stato raggiunto solo parzialmente. A causa delle complesse interrelazioni tra gli effetti del materiale e il sistema di utensili, al piede del dente si ottiene il massimo trattamento meccanico della superficie. I campioni mostrano però il grande potenziale del nuovo concetto lavorazione.
Riferimenti
[1] Mokhtari, N., Grzeszkowski, M., & Gühmann, C. (2017). Vibration signal analysis for the lifetime-prediction and failure detection of future turbofan components. Technische Mechanik-European Journal of Engineering Mechanics, 37(2-5), 422-431.
[2] Daniel, B., & Biermann, T. (2017). eAxle family in coaxial and offset arrangements. In 16th international CTI symposium automotive transmissions, Berlin.
[3] Hinterstoil3er, M., 2014, Zur Optimierung des Wirkungsgrades von Stirnradgetrieben,
Dissertation, Technische Universität München
[4] Güntner, C., Tobie, T., & Stahl, K. (2017). Influences of the residual stress condition on the load-carrying capacité of case-hardened gears. In AGMA 2017 Fall Technical Meeting (pp. 328-344).
[5] Broszeit, E., & Adelmann, J. (1996). Schwingfestigkeitssteigerung durch Festwalzen— Grundlagen und Anwendung. Mechanische Oberflächenbehandlung, 63-82.
[6] Altenberger, l. (2005, September). Deep rolling—the past, the present and the future. In Conf Proc: ICSP (Vol. 9, pp. 144-155).
[7] Liebisch, A. (1990), Einfllüsse des Festwalzen auf die Eigenspannungsverteilung und die Dauerfestigkeit einsatzgehärteter Zahnräder, Dissertation, Karlsruhe: Universität (TH) Karlsruhe.
[8] Schulze, S. (2022). Inline-Festwalzen zur Erhöhung der Zahnfu0tragfähigkeit. Shaker Verlag.
P. Fischmann, A. Hilligardt, V. Schutze, Institute of Production Science, Karlsruhe Institute of Technology