Le leghe di titanio sono ampiamente utilizzate nell’industria automobilistica, chimica, aerospaziale, biomedica e in molte altre applicazioni avanzate per via delle eccellenti caratteristiche di resistenza specifica, resistenza alla corrosione, elevato punto di fusione e biocompatibilità.
di Sergio Curioni
Una diffusione ancora più ampia delle leghe di titanio è limitata dalle proprietà tribologiche non eccellenti, soprattutto relative ad una usura adesiva severa e ad una bassa resistenza all’abrasione.
Per affrontare questa sfida, l’ingegneria delle superfici ha sviluppato diverse tecniche di modifica superficiale, tra cui trattamenti di conversione, termochimici e rivestimenti che hanno effettivamente portato a migliorare le proprietà tribologiche delle leghe di titanio. Tra queste, l’ossidazione elettrolitica al plasma (PEO) ha dimostrato, soprattutto di recente, di riuscire a restare al passo come anche ad essere più efficiente di altri trattamenti quali, ad es., la deposizione fisica da vapore (PVD). La PEO offre infatti una combinazione ottimale tra proprietà meccaniche, di resistenza alla corrosione e biocompatibilità che appaiono adattarsi perfettamente al caso delle leghe al titanio.
Nelle leghe leggere, la PEO opera accrescendo un film anodico attraverso microscariche ad arco all’interno di un bagno galvanico, la cui composizione influenza strettamente l’efficacia del rivestimento. In particolare, si utilizzano spesso elettroliti a base di silicati, fosfati e alluminati, che arrivano a produrre una forte passivazione del titanio, rendendoli adatti al trattamento PEO. Gli strati prodotti in questo genere di bagni di elettroliti misti sono caratterizzati da una microstruttura densa e uniforme, che permettono di raggiungere un ottimo compromesso tra spessore, durezza e adesione. Questo trattamento è rapido ed economico, adatto per componenti dalle forme complesse, come anche per ottenere una gamma ampia di spessori. Inoltre, con particolari accorgimenti, può rappresentare una alternativa eco-sostenibile ai trattamenti tradizionali.
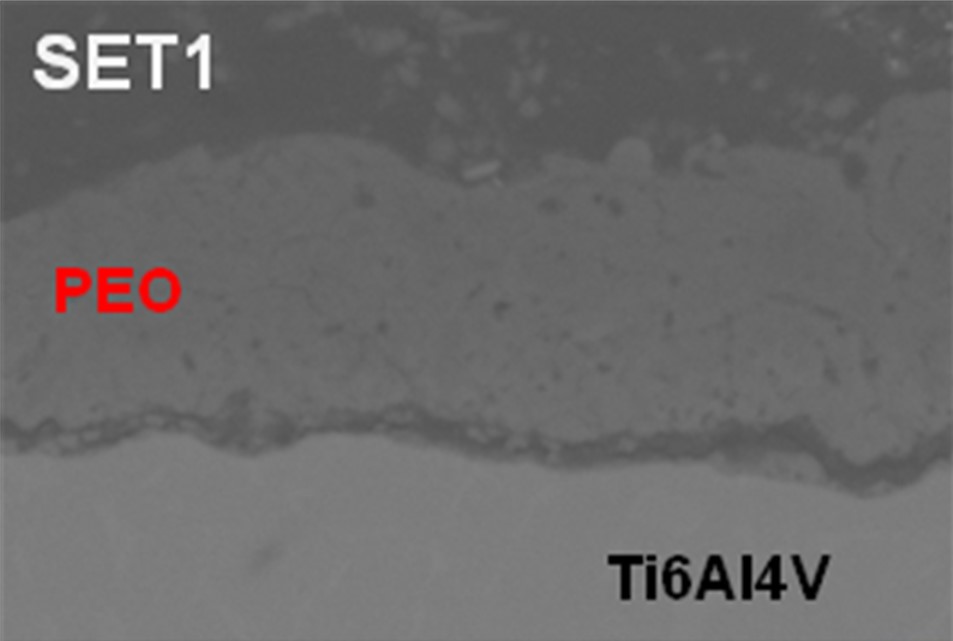
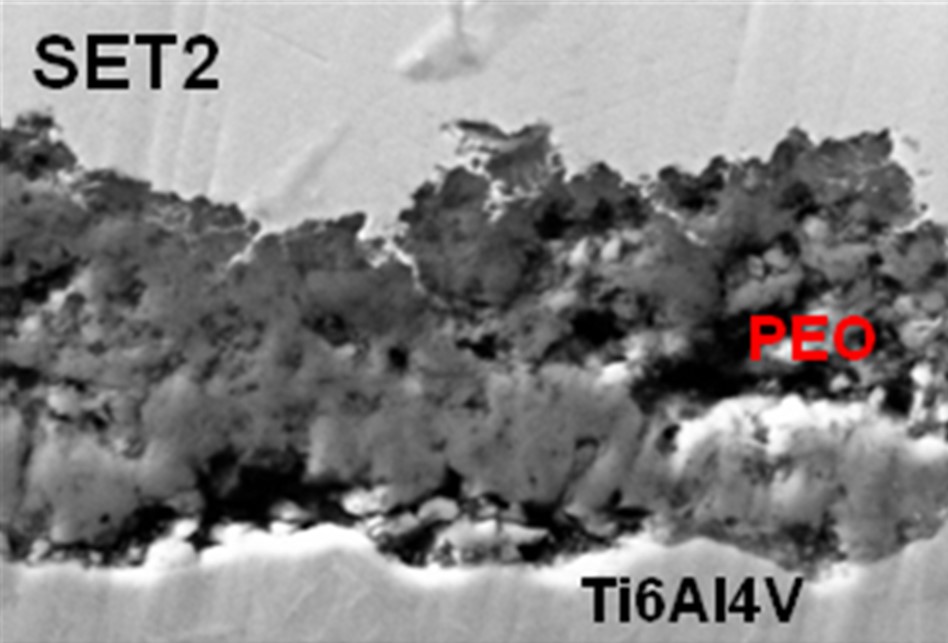
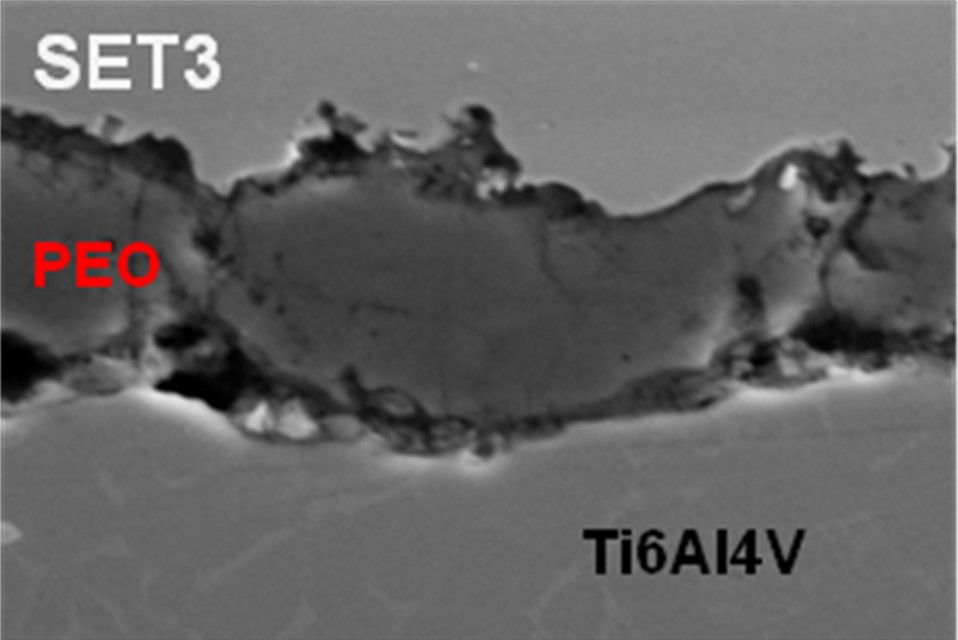
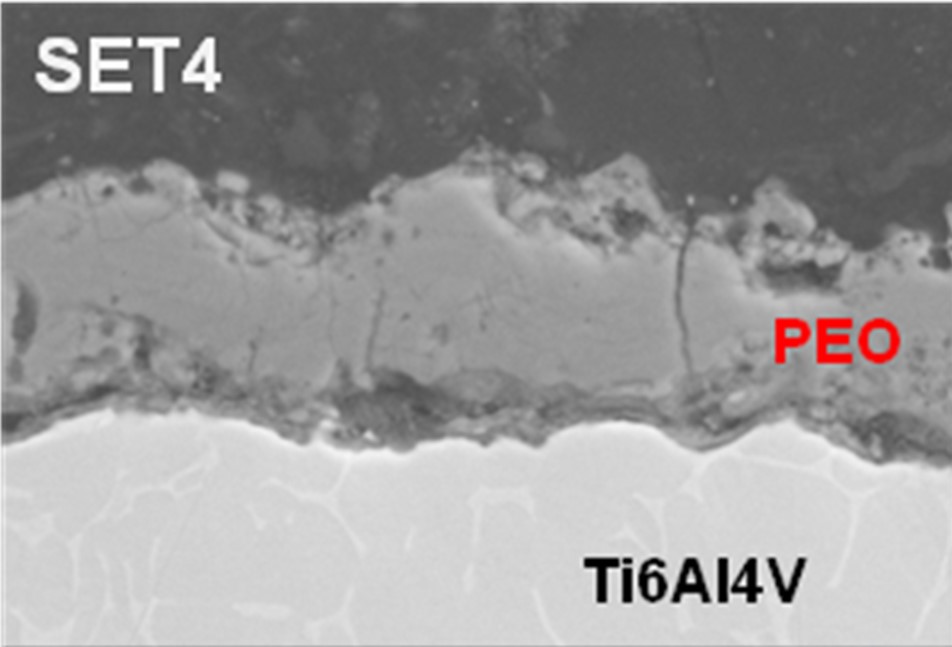
Materiali e metodi
Il presente studio ha avuto l’obbiettivo di valutare l’influenza di alcuni dei parametri di processo sulla resistenza del rivestimento finale nel caso di una lega Ti6Al4V. Il trattamento è stato eseguito in regime di corrente alternata, utilizzando bagni misti di alluminati e fosfati, andando poi ad analizzare la morfologia superficiale degli strati prodotti. Le funzionalità del rivestimento sono state verificate studiando il loro comportamento tribologico in condizioni di strisciamento. Nello specifico, sono state eseguite prove di strisciamento a secco contro acciaio (EN100Cr6), variando i carichi di prova da 5 a 120 N. Considerando poi come il contatto PEO/acciaio, in condizioni di strisciamento a secco, generi coefficienti di attrito piuttosto elevati (µ > 0.6), è stata anche analizzata l’utilità di depositare un sottile strato di PTFE sul rivestimento.
La Ti6Al4V è una lega piuttosto comune, con applicazioni frequenti in ambito aerospaziale (parti strutturali, carrelli di atterraggio, parti di motori), automobilistico (componenti di motori e sistemi di scarico ad alte prestazioni), industriale (parti di pompe, valvole, e strumenti per l’industria chimica), medicale (impianti ortopedici, come protesi articolari).
Conosciuta anche comunemente come Titanio Grado 5, la Ti6Al4V è caratterizzata da un alto contenuto in Titanio (Ti), pari a circa 90%, Alluminio (Al) al 6%, Vanadio (V) al 4% e tracce minori di altri elementi (es. Ferro). Ciò fornisce una lega ad alta resistenza alla trazione (circa 895-930 MPa), alla fatica, buona tenacità a frattura, e soprattutto elevato rapporto resistenza/peso.
Fornita qui in barre estruse, come di frequente in ambito industriale, la Ti6Al4V è stata solubilizzata a 900°C per 30min, temprata in acqua e invecchiata a 515°C per 510 min, ottenendo una durezza di 35HRC.
In Tabella 1 e 2 sono riportate la composizione chimica e le principali caratteristiche meccaniche della Ti6Al4V utilizzata, nonché i limiti previsti dalla specifica normativa (ASTM B348). Comparandone i valori appare confermata l’ottima qualità della lega oggetto di studio, da cui poi sono stati ricavati campioni per le successive analisi.
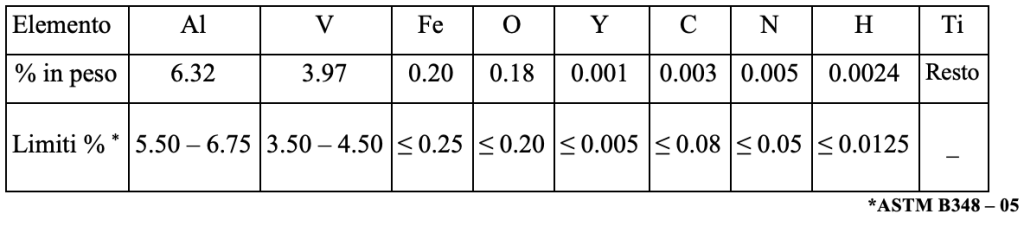
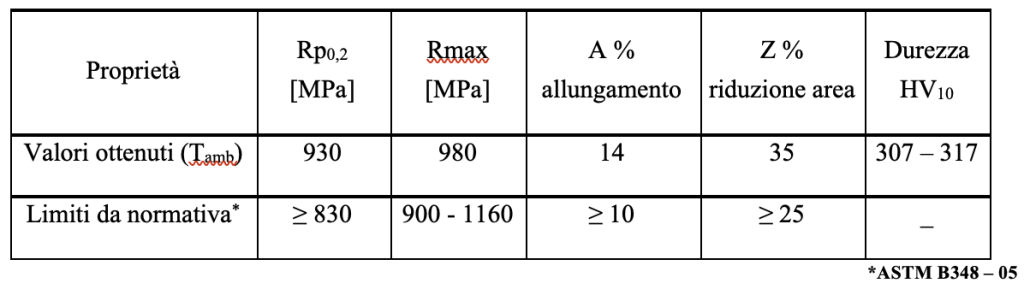
Questi provini, di 5×5 mm2 di sezione e 70 mm di lunghezza (Figura 1) sono stati trattati con PEO considerando differenti composizioni dell’elettrolita e generando quattro set distinti. Per il Set1 è stata utilizzata una procedura di trattamento coperta da brevetto di Keronite Ltd, UK (di cui per questo motivo non è possibile specificare le condizioni). I Set2, 3, 4 , sono stati realizzati presso il laboratorio del Department of Materials Science and Metallurgy dell’Università di Cambridge, UK, applicando le seguenti condizioni:
- tempo di trattamento: 60 min;
- densità di corrente iniziale: 20 A dm-2
- densità di corrente finale: 4 A dm-2
- potenza: 1 kW (costante durante il trattamento)
e con composizioni dell’elettrolita riportate in Tabella 3.
Nello specifico, si può osservare come il bagno del Set2 sia più ricco di alluminati, mentre il bagno da cui derivano i Set3 e Set4 presenti una maggiore quantità di fosfati. A questo proposito, va chiarito che entrambi i Set3 e Set4 sono stati ottenuti utilizzando le medesime condizioni del bagno, ma, nel caso del Set3, dopo il trattamento, è stato applicato uno strato di PTFE (topcoat). La deposizione è stata eseguita in due passate da 2 sec ciascuna di MOLYKOTE PTFE-N-UV (prodotto Dow Corning), una sospensione in aerosol a base di solvente organico.
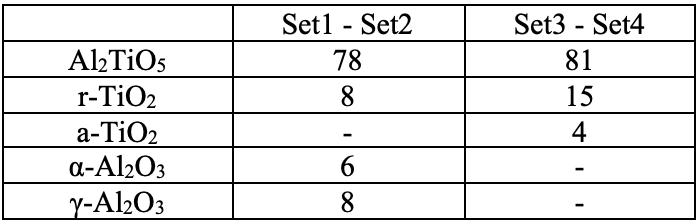
Risultati e discussione
Composizione di fase
Quale primo passo, sempre presso l’Università di Cambridge, è stata effettuata una analisi Rietveld degli spettri di diffrazione RX allo scopo di identificare le diverse fasi presenti negli strati depositati (Tabella 4). L’analisi conferma innanzitutto come le composizioni di partenza non fossero troppo diverse tra loro, e quindi neppure i rivestimenti finali. La fase maggiormente presente ora è il titanato di alluminio (Al2TiO5), derivato dalla incorporazione diretta degli elementi disciolti nell’elettrolita (vedi Tabella 3). È presente poi la fase di rutilo (r-TiO2), in quantità maggiore soprattutto nei Set 3 e 4, in quanto provenienti da bagni elettrolitici costituiti prevalentemente da fosfati. Per i Set 1 e 2 sono invece anche presenti le fasi α-Al2O3 (più dura, compatta e stabile) e γ-Al2O3 in conseguenza della prevalenza di alluminati nell’elettrolita (vedi Tabella 3).
Caratterizzazione microstrutturale
L’analisi è andata avanti attraverso osservazioni SEM sulle sezioni trasversali che hanno permesso di analizzare nel dettaglio la microstruttura del rivestimento (Figura 2). Le micrografie mostrano, in particolare, come per tutti i set lo strato di PEO presenti una morfologia irregolare, per quanto il Set4 presenti una morfologia a rientranze più accentuata (soprattutto rispetto al Set3). Nel Set2, nella porzione più esterna del rivestimento, la microstruttura risulta essere più frastagliata e porosa rispetto agli altri casi, caratterizzati da una microstruttura più densa e compatta.

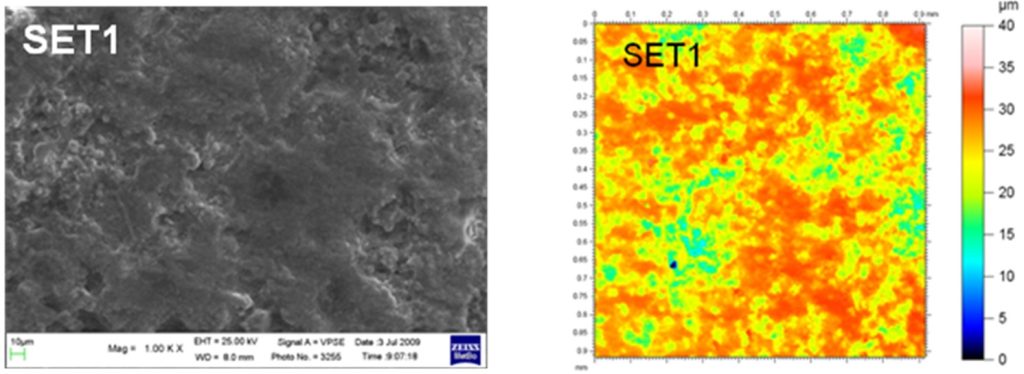
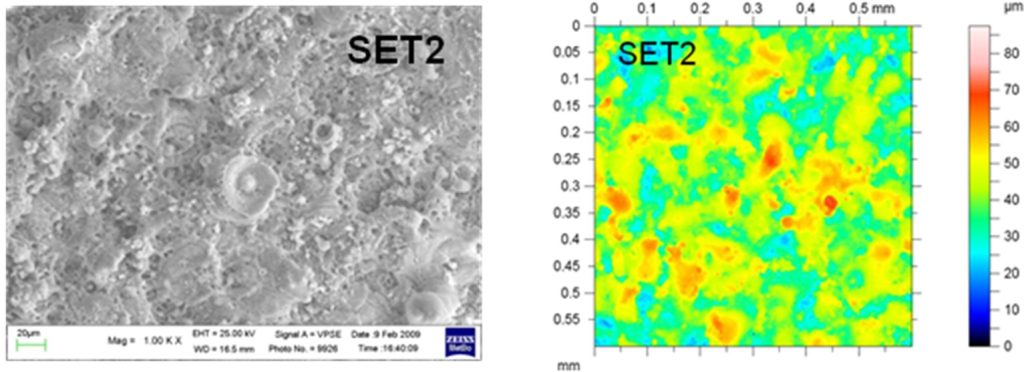
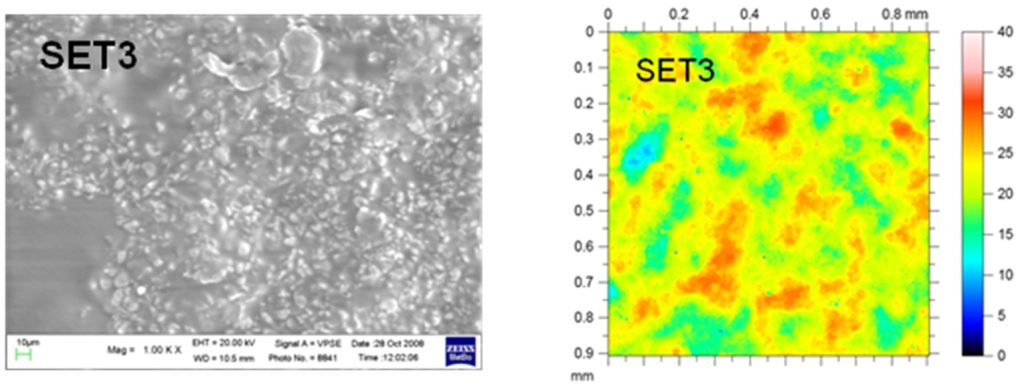
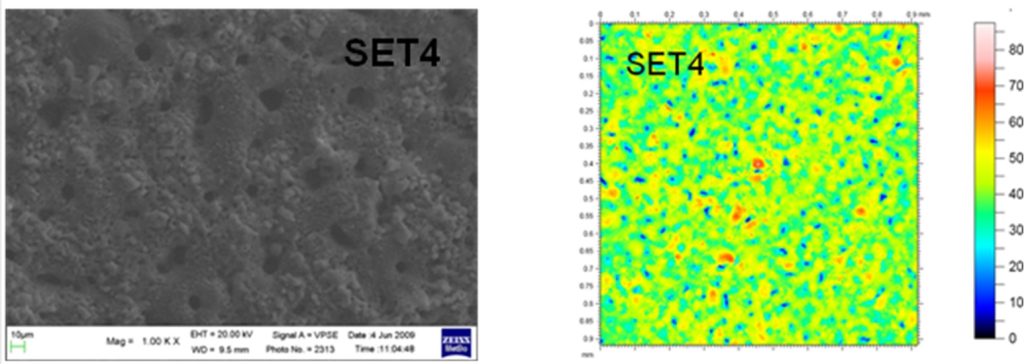
Partendo poi dalle micrografie, e grazie all’utilizzo di un software di analisi di immagine (Image Pro-Plus), è stato anche possibile ricavare lo spessore dei diversi rivestimenti, inteso come valore medio fra più osservazioni (Tabella 5). Si è potuto notare, ad esempio, come lo spessore del rivestimento creato nel caso del Set1 sia del tutto comparabile con quelli ottenuti nel Set3 e Set4. Il Set2 invece, risulta avere uno strato di rivestimento più spesso del 30% o 40% rispetto agli altri casi. Il fatto poi che gli spessori rilevati per Set3 e Set4 siano quasi coincidenti è correlato al fatto che l’applicazione del PTFE avviene rispetto ad una scala micrometrica.
Analisi morfologica superficiale
In Figura 3, la morfologia superficiale dei quattro rivestimenti, osservata tramite SEM (a sinistra delle immagini), è posta a confronto con la sua topografia, derivata attraverso profilometria ottica bidimensionale (a destra). Questa seconda tecnica permette di quantificare quanto magari già rilevato attraverso l’osservazione SEM.
Il Set1 risulta avere una morfologia superficiale regolare e livellata, caratteristica da aspettarsi per una procedura ormai messa a punto industrialmente. Il Set2 presenta al contrario una topografia spessa e irregolare, caratterizzata dalla presenza di porosità e, nella zona di scarica elettrica, da alcuni ampi crateri con fori centrali di ritiro. Anche il Set4 ha una morfologia superficiale piuttosto irregolare, contraddistinta da rientranze, poi totalmente livellate, nel caso del Set3, dallo strato di PTFE aggiuntivo. In Figura 4 si evidenzia proprio questo effetto, di come il PTFE vada ad ancorarsi sullo strato del rivestimento, sfruttandone la morfologia irregolare, per poi procedere a livellarla (Figura 4). Tornando invece alle depressioni (pit) del Set4, esse si distinguono ancora più chiaramente passando alla topografia bidimensionale, che ne stima le dimensioni in circa 10µm.
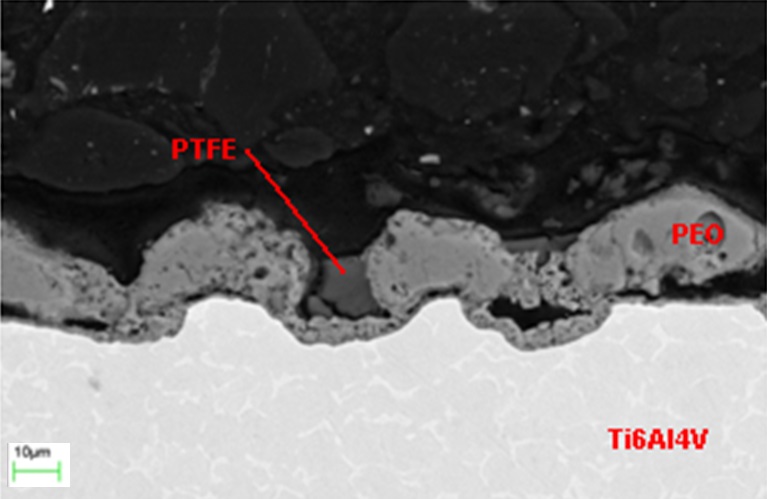
Analisi di rugosità
Sono state quindi eseguite misurazioni di rugosità superficiale, ottenute mediante profilometria a stilo. Ai quattro set considerati, sono state affiancate misure di comparazione su provini Ti6Al4V non rivestito. Le misure sono state effettuate tanto in direzione longitudinale che trasversale, elaborando i valori in termini di rugosità media aritmetica (Ra) e profondità media (Rz), come riportato in Tabella 6.
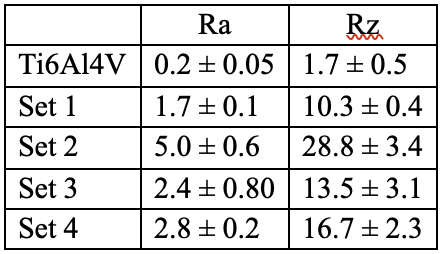
Si nota come i valori di Ra e Rz siano inferiori per il Ti6Al4V non rivestito, risultato plausibile considerato che il rivestimento PEO è ottenuto inducendo la crescita di ossidi in condizioni relativamente turbolente. Inoltre, i valori determinati confermano l’analisi topografica precedente, con il Set2 che presenta valori di rugosità maggiori e, come già segnalato in precedenza, il Set1 che risulta avere una finitura superficiale migliore. Torna infine ad emergere l’effetto “livellante” del PTFE del Set3 rispetto al Set4 con valori di Ra di 2.4 vs 2.8 e Rz di 13.5 vs 16.7.
Caratterizzazione tribologica
In Figura 5a sono messi a confronto gli andamenti dei coefficienti di attrito (µ) in funzione del carico applicato per i quattro set a confronto. Rispetto al sostrato non rivestito in Ti6Al4V, i Set 1, 2 e 4, mostrano valori di µ più elevati (compresi tra 0,6 e 1,0) e fra loro confrontabili, le cui cause sono da imputare a:
- Fenomeni di tribossidazione a carico dell’antagonista: l’azione abrasiva delle microasperità dure del rivestimento PEO porta all’asportazione di materiale dal cilindro, per effetto del calore sviluppato dall’attrito, il materiale asportato viene quindi ossidato e compattato sulle superfici a contatto, formando strati a base di ossidi di ferro e cromo.
- Fenomeni di adesione tra le superfici rivestite dagli strati di trasferimento precedentemente descritti: le superfici accoppiate, ricoperte da tali strati, infatti, acquistano caratteristiche di compatibilità chimica che danno luogo ad un aumento della componente adesiva della forza di attrito.
- Fenomeni di abrasione, dovuti alla presenza di frammenti duri dal rivestimento PEO usurato, che entrano a far parte dello strato di trasferimento incrementando la componente abrasiva della forza di attrito.
- Fenomeni di oscillazioni di µ, dovuti probabilmente al variare del carico applicato, da attribuire alle variazioni di stabilità degli strati di riferimento.
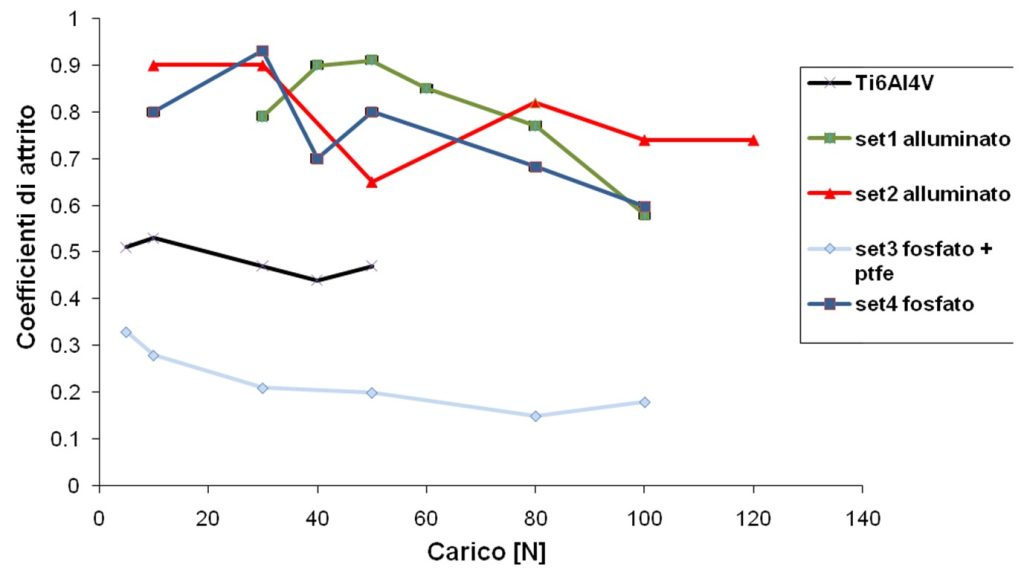

I rivestimenti considerati, presentano coefficienti di attrito elevati, in quanto gli strati PEO devono esplicare finalità prevalentemente antiusura. Tuttavia, l’applicazione di un sovra-strato in PTFE, che esercita un’efficace azione di lubrificazione solida, ha prodotto risultati interessanti anche in termini di riduzione del coefficiente di attrito, il Set 3, che presenta il più basso coefficiente di attrito tra tutti i set considerati.
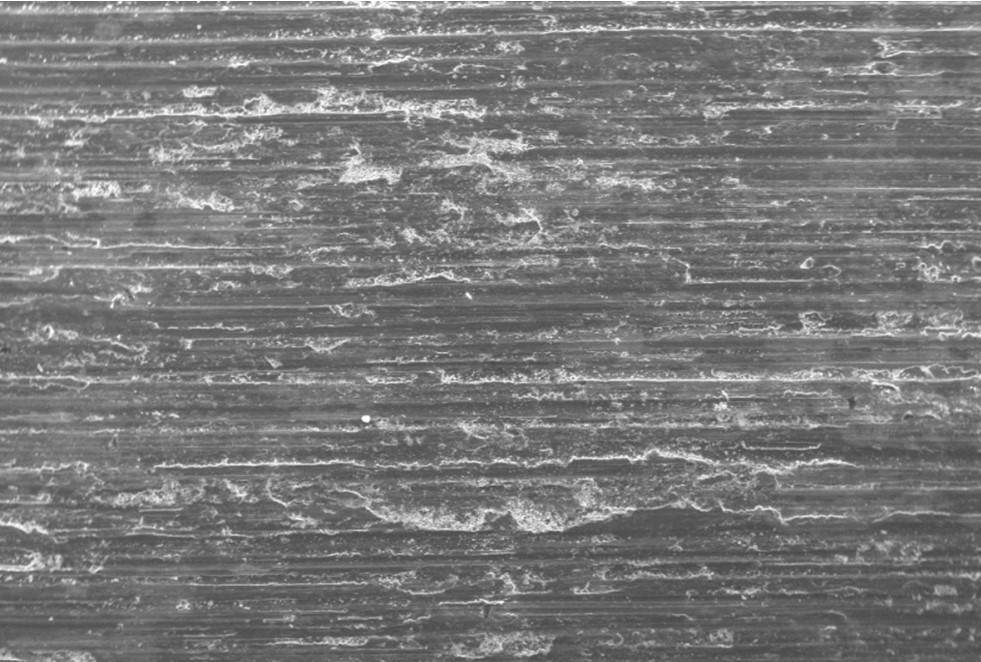
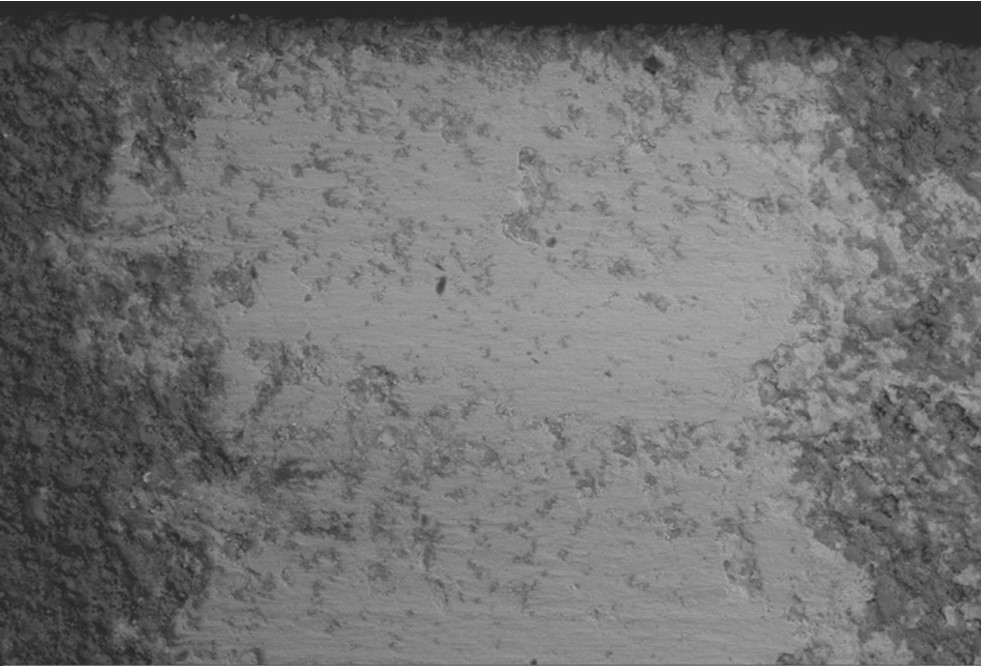
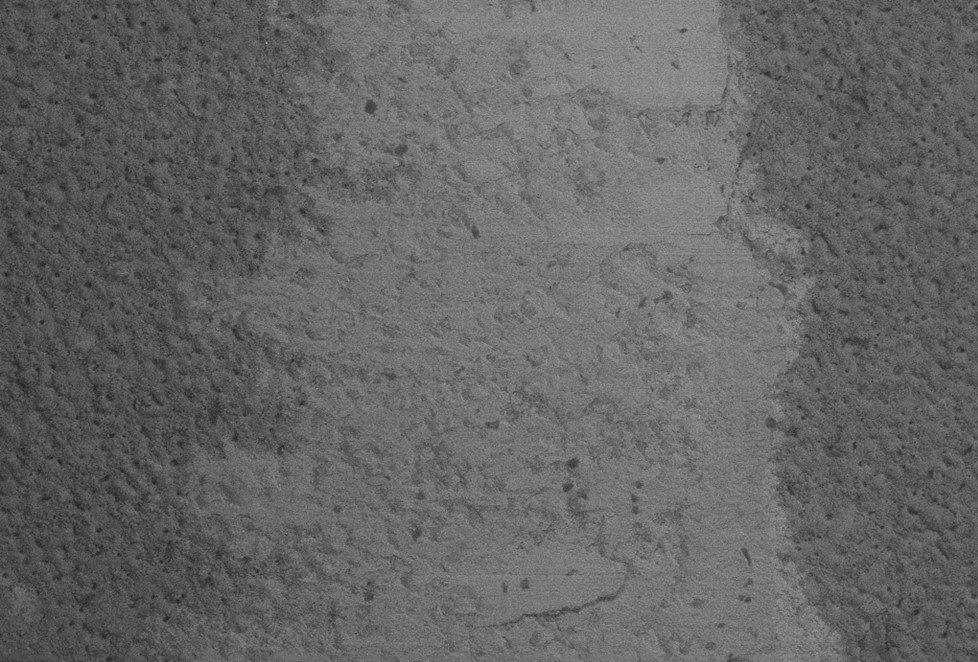
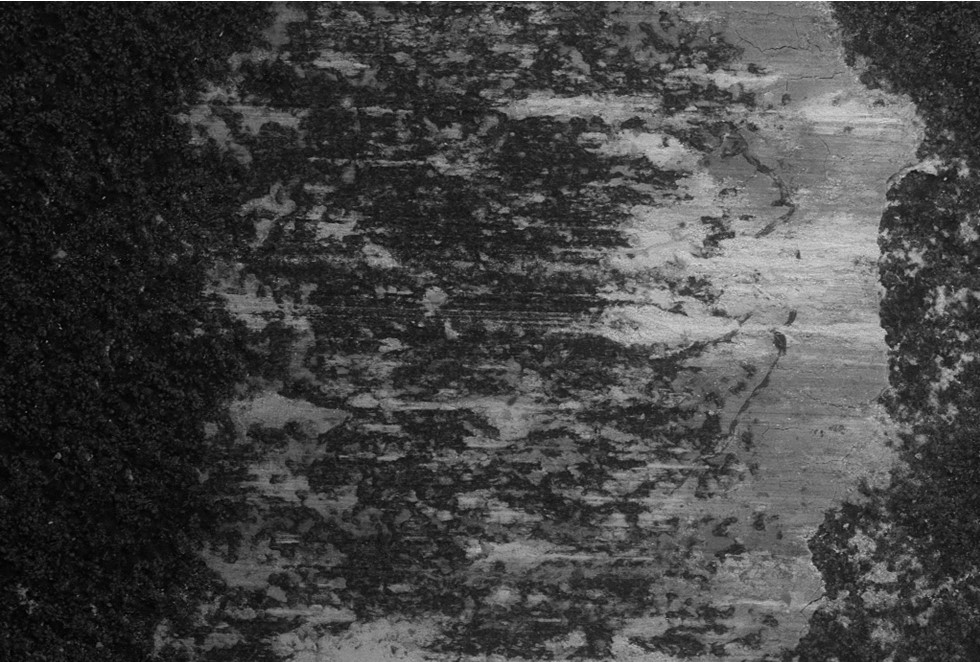
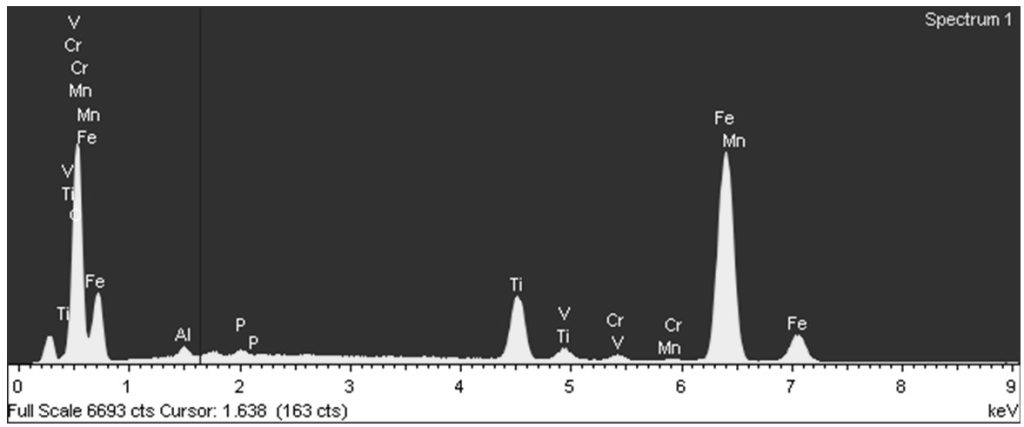
Volumi di usura
In Figura 5b sono riportati gli andamenti dei volumi di usura (in mm3) in funzione del carico applicato (tra 5 e 120 N). Si evidenzia, soprattutto, come qualsiasi sia il rivestimento scelto, è comunque in grado di garantire un’efficace azione antiusura. La lega in titanio Ti6Al4V non rivestita, infatti, risulta soggetta a tassi di usura molto elevati anche a fronte di bassi carichi di prova. Ciò appare legato ad interazioni tanto abrasive che adesive, che portano ad un’aratura profonda dalla lega di titanio con distaccamento ed asportazione di ampi frammenti del materiale.
Entrando in dettaglio nei rivestimenti, i Set 1 e 2 mostrano un comportamento del tutto analogo, per quanto il Set2 presenti una maggiore resistenza all’usura. Questa differenza è riconducibile alla diversa microstruttura a fronte di una composizione chimica che conosciamo come molto simile. Sempre riguardo al Set 2, sappiamo già dalle analisi precedenti come sia caratterizzato da una maggiore porosità (Figura 3B) che potrebbe dare luogo ad una maggiore capacità di tollerare deformazioni in campo elastico e, quindi, ad una maggiore resistenza all’usura. Dall’analisi del Set3 e 4 si deduce invece come il trattamento favorisca la formazione di strati di trasferimento, a seguito di fenomeni di abrasione dell’antagonista ed ossidazione e successiva compattazione dei detriti, che conducono a regimi di usura moderata tribossidativa.
Carico di transizione
Per ciascun Set è stato infine identificato un carico di transizione definito come il carico per cui avviene la completa asportazione del rivestimento. In corrispondenza, si passa da un regime di usura moderata ad usura severa, per via del coinvolgimento del sostrato nel contatto. In Tabella 7 sono riportati questi carichi di transizione. In via generale, incrementando il carico di prova, la transizione appare evidente sia nell’andamento del coefficiente di attrito (Figura 5a), che nell’andamento dell’usura in termini di volume (Figura 5b): il coefficiente di attrito cala attestandosi ai valori tipici della coppia titanio/acciaio, e l’usura di sistema incrementa, data la formazione di dedriti fortemente abrasivi. Dal momento con carichi eguali e maggiori del carico di transizione si ha il coinvolgimento del sostrato nel contatto, si determina un incremento notevole del volume di usura.

Rispetto ai rivestimenti, i primi tre set hanno un carico di transizione confrontabile, confermato anche da volumi di usura ed andamenti in funzione del carico del tutto paragonabili, mentre il Set 4 risulta dotato di minore resistenza all’usura, probabilmente per via dello spessore più sottile. Il carico di transizione si attesta infatti a 40N per il Set4 ed a 80N per il Set3, confermando attraverso le analisi condotte l’importanza dell’applicazione del PTFE sullo strato PEO, sia per esplicare la funzione antiattrito, sia per incrementare notevolmente la resistenza all’usura e la vita dello strato di PEO.
Meccanismi di usura
In Figura 6 sono poste a confronto le piste di usura per condizioni di carico normale di 10N. La pista di usura del Ti6Al4V non trattato (Figura 6a) è caratterizzata da arature profonde e solchi evidenti, risultato di fenomeni di usura severa di tipo abrasiva e adesiva. Al contrario, le piste di usura dei provini trattati, in particolare del Set2 e Set4, presentano tracce meno evidenti (Figura 6b-c). Inoltre, risultano ricoperti da strati di trasferimento costituiti da elementi provenienti sia dal materiale dell’antagonista (Fe, Cr) che provenienti dal rivestimento stesso (Ti, Al, V), come mostra l’analisi EDS effettuata (Figura 6e) e di cui si parlerà meglio in seguito. Per ora è sufficiente notare come la formazione di strati di trasferimento, per bassi carichi di prova, è imputabile a fenomeni tribossidativi a carico dell’antagonista, dovuta per l’azione combinata di carichi meccanici e termici, determinati dalle condizioni di strisciamento.
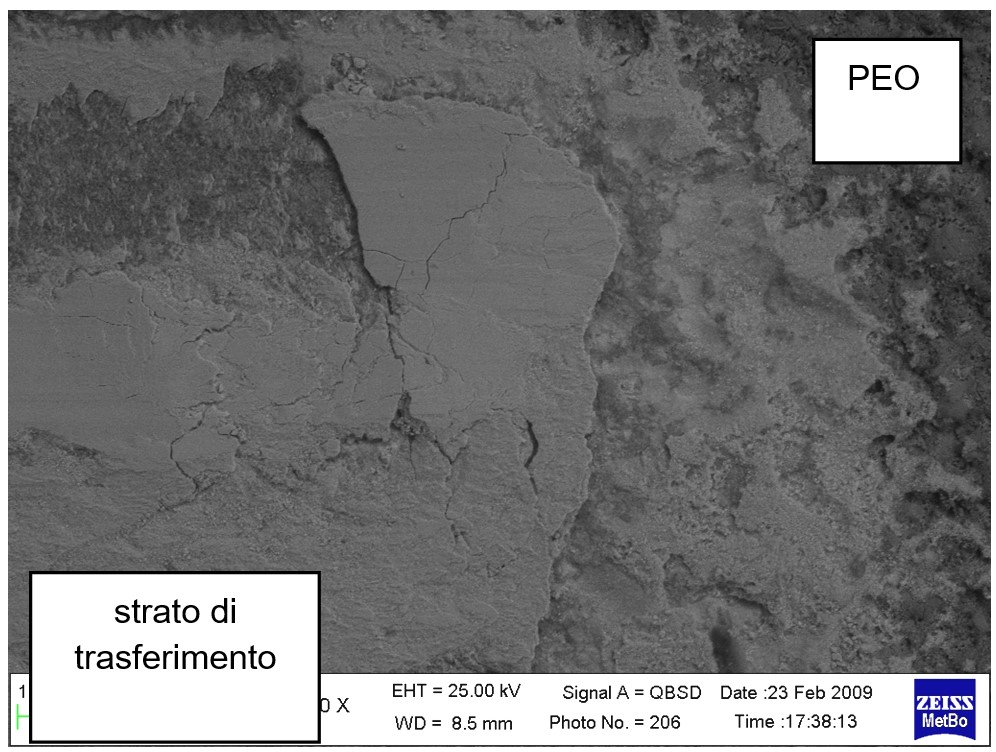
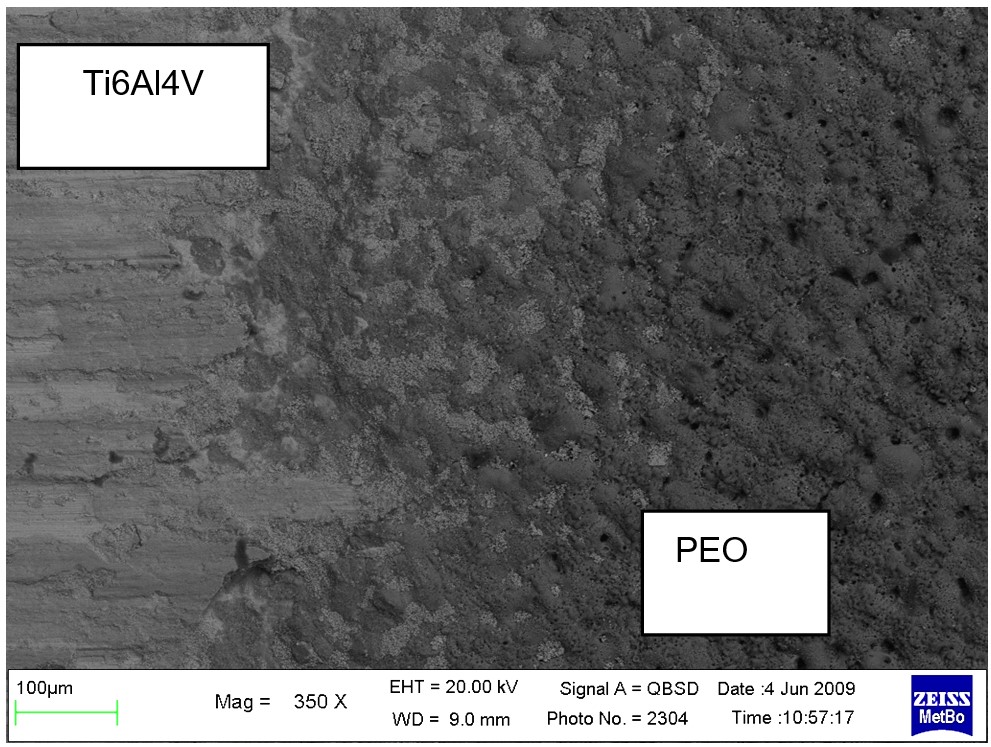
Strati di trasferimento
La presenza di strati di trasferimento, durante lo strisciamento nel sistema PEO/acciaio, è responsabile dell’incremento del coefficiente d’attrito (µ), in quanto il sistema tribologico PEO/acciaio diventa acciaio/strati di trasferimento; le superfici accoppiate, ricoperte da tali strati, acquistano quindi caratteristiche di compatibilità chimica e si incrementa la componente adesiva della forza di attrito. Il nuovo sistema tribologico acciaio/strati di trasferimento, le fluttuazioni di µ, sono imputabili a fenomeni di stick-slip, mentre le fluttuazioni dell’usura di sistema, sono causate dai dedriti che vengono inglobati ed espulsi durante la formazione dello strato di trasferimento.
Si è accennato in precedenza al fatto che gli strati di trasferimento contengono anche frammenti, finemente macinati, provenienti dallo strato PEO, che risulta essere soggetto ad usura moderata da micropolishing, proprio per l’azione abrasiva dei dedriti presenti nello strato di trasferimento. Lo strato PEO, infatti, durante la prova di strisciamento a secco, si usura gradualmente, mantenendo la sua morfologia originale, esente da cricche e da distacco di frammenti di grandi dimensioni. È possibile verificare l’usura moderata da micropolishing in Figura 7 in cui sono riportate le micrografie di PEO usurato, in condizione di elevati carichi di prova, prima (Figura 7a) e dopo (Figura 7b) il coinvolgimento del sostrato nel contatto.
Finora si è discusso come i frammenti duri, provenienti dallo strato PEO e in seguito intrappolati negli strati di trasferimento, contribuiscano ad incrementare la componente abrasiva dell’attrito, mentre il trasferimento di materiale fra le superfici accoppiate, incrementi la componente adesiva. Anche se la formazione di questi strati per la coppia PEO/acciaio comporta elevati valori del coefficiente di attrito µ, risulta pertanto benefica per incrementare la resistenza all’usura del PEO. Infatti, solo per elevati carichi di prova, questi strati diventano instabili, dal momento che l’equilibrio fra inglobamento/espulsione di dedriti si sposta verso l’espulsione e lo strato stesso si cricca e delamina; senza lo strato di trasferimento il tasso di usura dello strato PEO aumenta fintanto che il rivestimento stesso viene rimosso.
Per il Set3 (PEO+PTFE), gli strati di trasferimento sono costituiti oltre dagli elementi provenienti dall’antagonista, anche da lamine di PTFE che si spalmano sulle superfici dei corpi a contatto. Per bassi carichi di prova (5÷10 N) frammenti di PTFE si formano e distribuiscono sulla pista di usura, agendo quindi da lubrificante solido, ma non rimangano fra le superfici a contatto fino alla fine della prova, in quanto espulsi. Tutto ciò ha un grande effetto sulle condizioni di attrito.
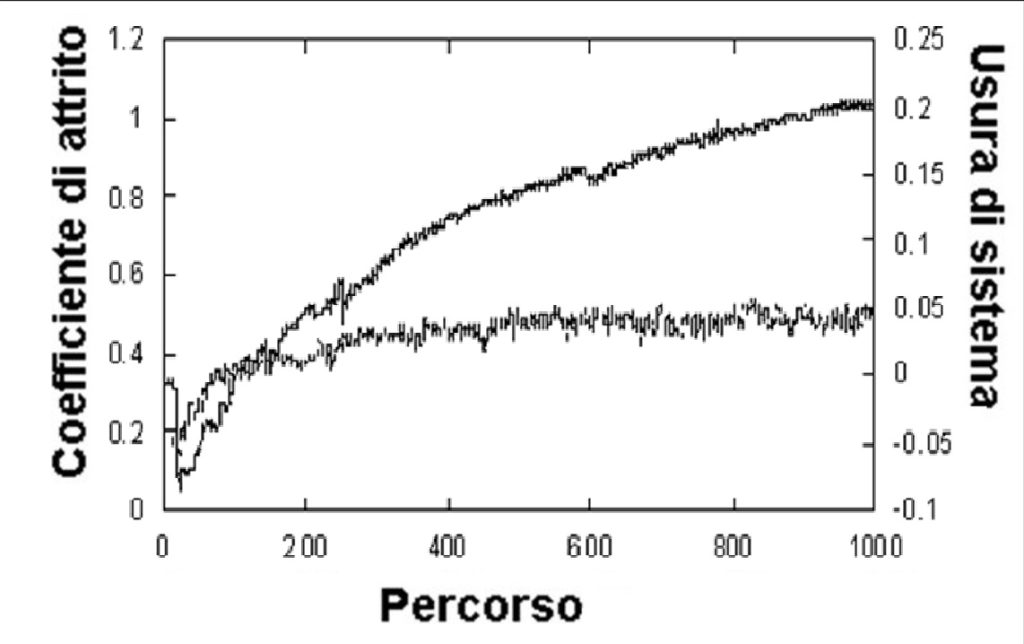
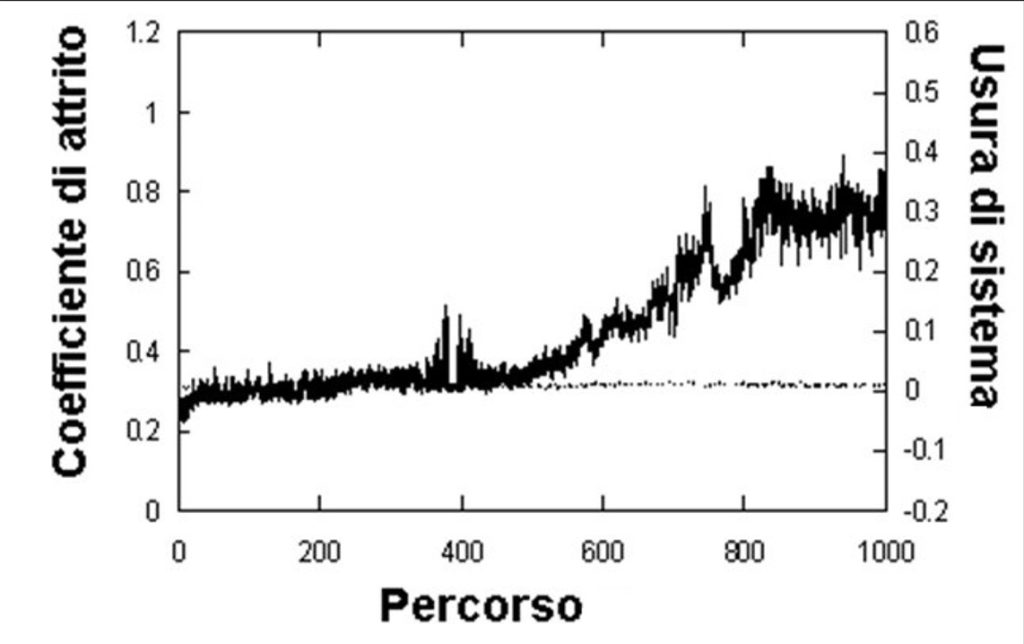
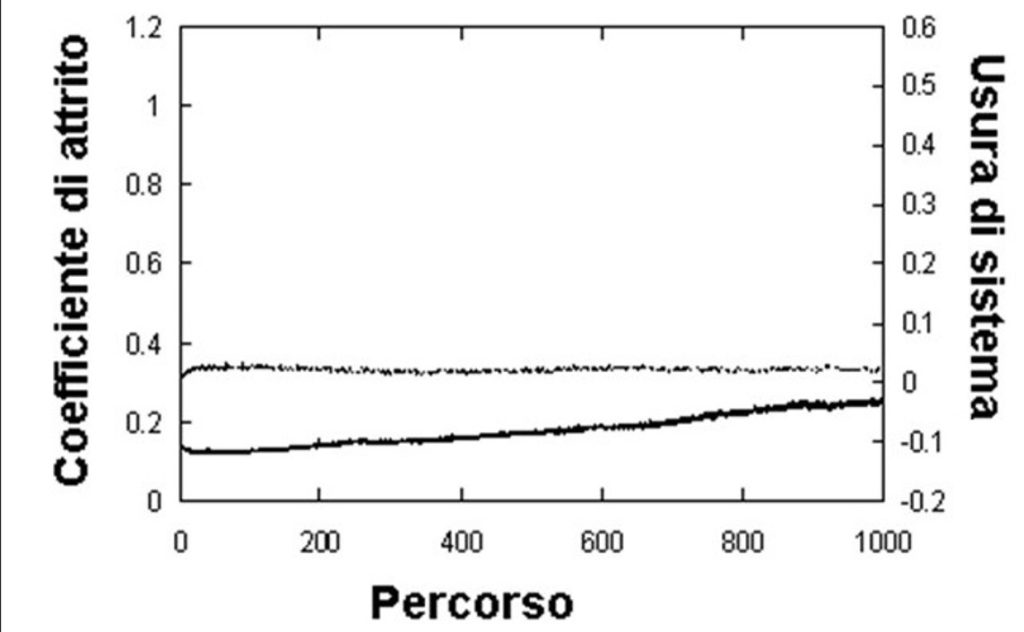
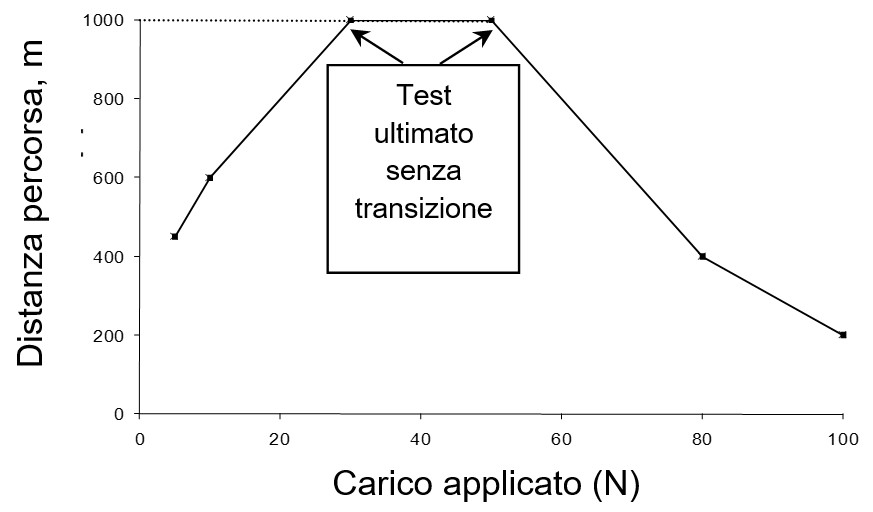
Coefficiente di attrito
In Figura 8 sono mostrati alcuni dei risultati ottenuti nello studio dell’attrito: si tratta di prove di strisciamento a secco della lega contro un acciaio 100Cr6 da cui sono stati determinati il coefficiente di attrito (µ) e l’usura di sistema in funzione della distanza di prova (fissata a 1000m) per un determinato carico. In Figura 8a, che rappresenta la prova di riferimento, gli andamenti sono mostrati nel caso di Ti6Al4V non trattato e carico di 30N. In generale, è possibile tornare ad osservare come il comportamento del rivestimento è molto influenzato dal carico, con una sostanziale discontinuità se si resta al di sotto o meno del carico di transizione. In corrispondenza di questo carico, il rivestimento presenta un cedimento che porta la lega ad entrare in diretto contatto con l’antagonista acciaio, con effetti di evidente accelerazione del tasso di usura (come mostrato in Figura 8b e Figura 8c). Nello specifico, il Set4 manifesta alti valori di µ, pari a 0.65÷0.93, comportamento giustificato dall’azione abrasiva dello strato PEO. Per il Set3 si ottengono valori di µ inferiori, compresi fra 0.18 e 0.33, che evidenziano l’azione di lubrificante solido del PTFE. In tal senso, la Figura 8d mostra il percorso di strisciamento critico (indice della “vita” dello strato di PTFE) in funzione del carico di prova applicato. Il grafico evidenzia chiaramente la peculiarità del PTFE che, per quanto riguarda le prove a 30 e 50N, mostra una sopravvivenza che coincide con l’intero percorso di strisciamento (1000m). Si può quindi definire questo range come il “range ottimale” di esercizio dello strato di PTFE nelle condizioni di strisciamento testate. In condizioni di regime (30N di carico) la coppia titanio/acciaio, presenta un valore di coefficiente attrito medio pari a circa a 0.5.
Per i provini appartenenti al Set3 e Set4, si è determinato come nelle medesime condizioni di carico, il coefficiente di attrito aumenti significativamente per il Set4, attestandosi ad un valore medio pari a 0.8±1, mentre per il Set3, lo strato di PTFE depositato sul PEO, esplica la funzione antiattrito, riducendo drasticamente il valore del coefficiente di attrito a 0.2÷0.3. Una volta esaurite le lamine di PTFE, il coefficiente di attrito µ da circa 0.3 si incrementa fino a ~0.8 (Figura 8b). Per carichi intermedi di prova (30÷50 N), abbastanza elevati per il distacco di frammenti di PTFE e per garantirne il contatto con le superfici, il coefficiente µ, rimane basso (µ < 0.3) durante l’intera durata del test, senza manifestare alcuna transizione (Figura 8c). Quindi si è determinato come lo strato di trasferimento contenente PTFE rimanga stabile, contrastando l’usura dello strato PEO, fino a 50 N di carico normale applicato. Per carichi maggiori, si forma la componente lubrificante degli strati di trasferimento, ma si esaurisce in tempi brevi a causa di fenomeni di tipo abrasivo (gli effetti termici sono probabilmente trascurabili per le basse velocità di prova adottate), comportando un generale incremento del coefficiente di attrito µ.
Microanalisi degli elementi
L’analisi degli elementi presenti sulle superfici mediante microsonda a dispersione di energia (EDS), già accennata in riferimento alla Figura 6e, permette di aggiungere quale considerazione in più alla discussione. Le immagini in Figura 9 mostrano solo alcuni esempi di questo genere di analisi con microanalisi effettuate sul Set3 e Set 4 rispetto ad una lunghezza pari alla linea orizzontale visibile.
Il Set4 è stato realizzato in un bagno ricco di fosfati, la cui composizione indicativa è Na3PO4 + NaAlO2; si nota come i conteggi dell’alluminio hanno un andamento crescente all’allontanarsi dal sostrato, poiché tale elemento viene incorporato dal bagno elettrolitico ricco di alluminati. Al contrario i conteggi del titanio hanno un andamento decrescente dal sostrato al rivestimento, in parte perché il titanio si è disciolto nell’ambiente di trattamento ed in parte perché ha formato il titanato di alluminio (Al2TiO5) e l’ossido (TiO2), come si evince dalla presenza dell’ossigeno all’interno del PEO. La presenza di fosforo, in quantità maggiori sulla zona superficiale, è giustificata da specie amorfe situate nelle rientranze della superficie. Nelle sporgenze superficiali, invece, si ha presumibilmente una prevalenza di titanato di alluminio (Al2TiO5). I rivestimenti PEO, ottenuti da bagni ricchi in fosfati, sembrano presentare una geometria irregolare, disomogenea e sottile, dovuti alla forte influenza degli elementi chimici dell’elettrolita, i quali interagiscono con il substrato nella reazione di ossidazione conferendo al rivestimento caratteristiche tribologiche particolari. Nel caso del Set3, che si ricorda essere identico al Set4 con l’aggiunta di uno strato di PTFE, la presenza del PTFE sul rivestimento può essere confermato dai conteggi rilevati dell’elemento fluoro, dalla sonda EDS, in corrispondenza dello strato superficiale. Nel rivestimento PEO, prodotto in un bagno ricco di fosfati si nota anche la presenza di alluminati, come verrà poi confermato anche in seguito dall’analisi XRD.
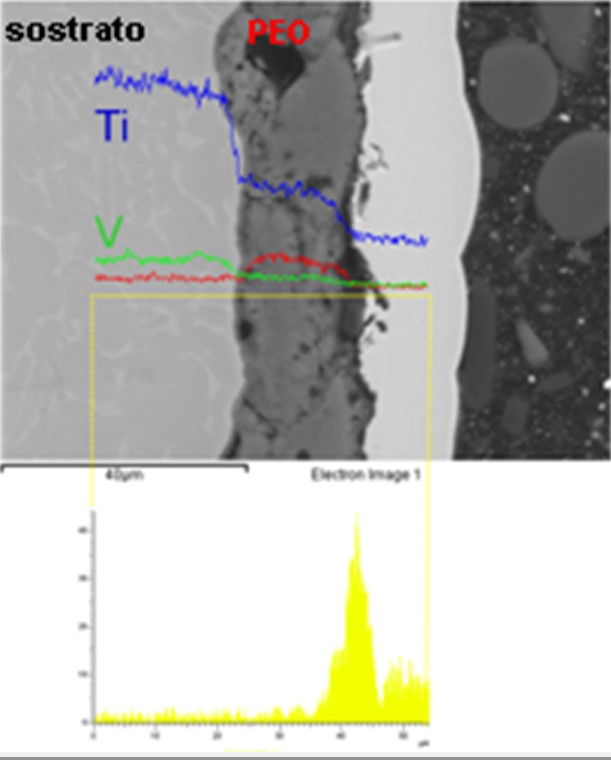
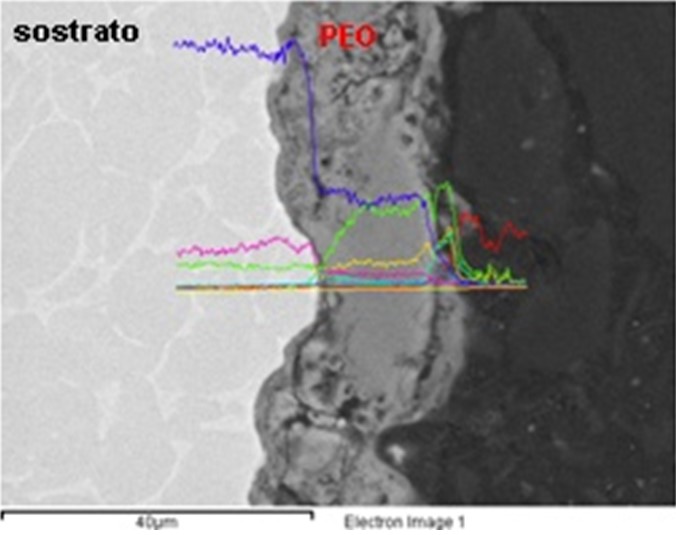
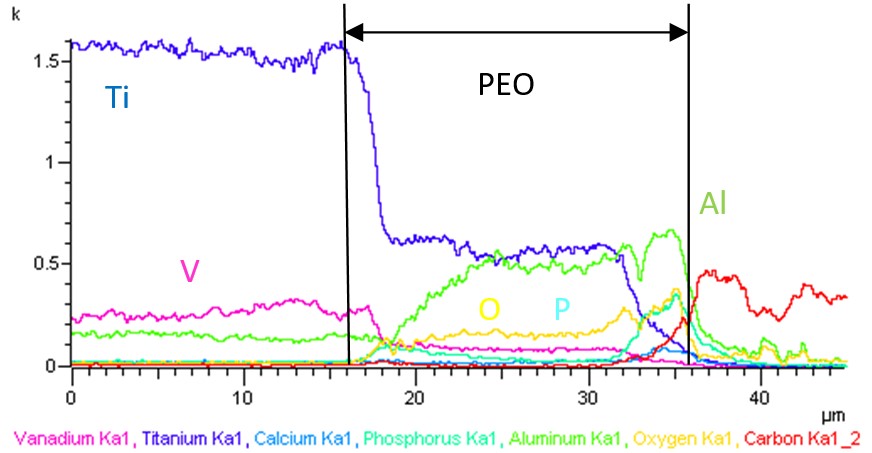
Analisi morfologica superficiale
L’analisi di profilometria ottica conferma i dati ottenuti dalle misure di rugosità, effettuate con profilometria a stilo, per il campione in Ti6Al4V non rivestito, in quanto dalla Figura 10 è visibile la notevole anisotropia delle caratteristiche rugosimetriche dovuta alla marcata direzionalità nelle lavorazioni di fresatura e rettifica finale. Dall’analisi della morfologia superficiale, della sezione trasversale e dalla caratterizzazione della rugosità si può evincere come la morfologia del Set4 sia particolarmente indicata per esplicare l’ancoraggio di uno strato sovrapposto di materiale come il PTFE.
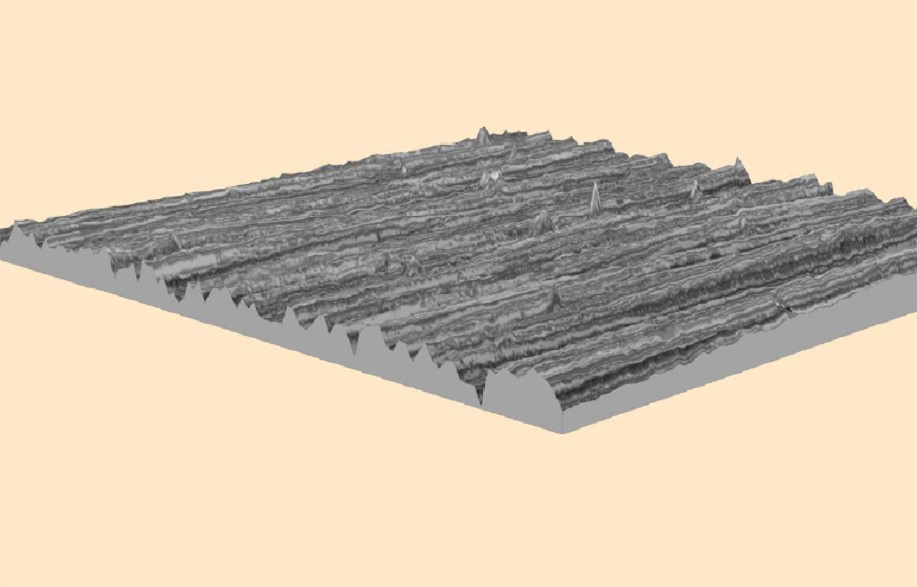
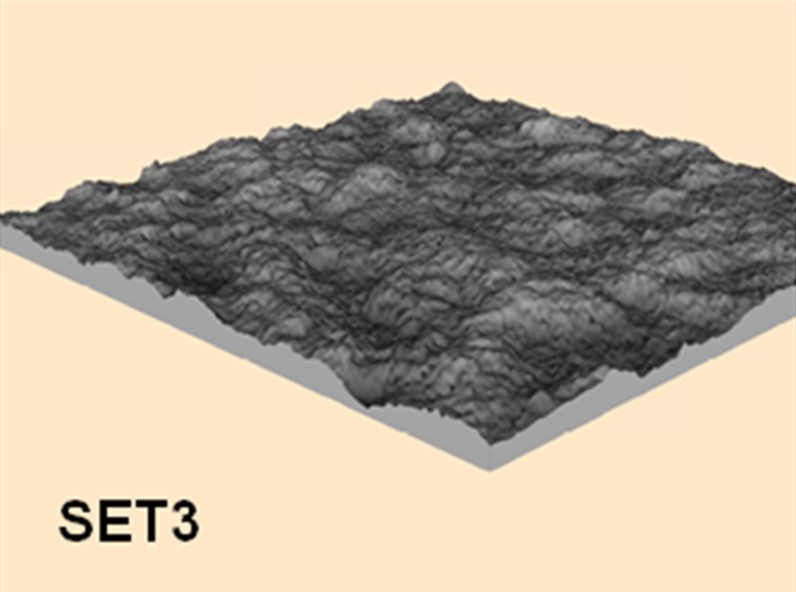
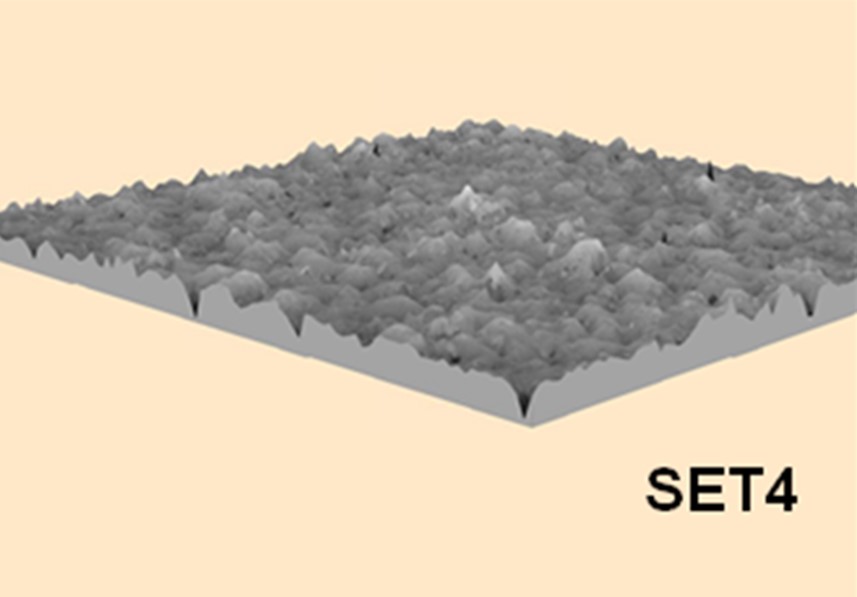
Analisi diffrattometrica delle fasi
L’analisi diffrattometrica delle fasi (XRD), finale in questo studio, è stata condotta sulla superficie di spezzoni di campione lunghi circa 25 mm, mediante diffrattometro Philips PW1720, con anodo di Cu e radiazione monocromatica K–α in modalità θ/2θ e parametri di generazione di 40 kV e 30 mA. L’analisi ha permesso di identificare le fasi in esso contenute e di avere un riscontro sulla natura dell’elettrolita che è stato utilizzato (Figura 11). Si può semplificare segnalando come, in generale, la composizione delle fasi è legata a due aspetti principali: la composizione del bagno e le temperature di lavoro. Lo spettro rivela che la fase predominante è il titanato di alluminio (Al2TiO5), che è un ossido misto di alluminio e titanio. La prevalenza di questa fase è dovuta all’impiego di un elettrolita contenente alluminio. Sono presenti, inoltre, il rutilo (TiO2 tetragonale ortorombico), tipico dei bagni contenenti fosfati e frequente quando si raggiungono alte temperature di processo, e l’anatasio (TiO2 tetragonale). Non si è stati in grado di rilevare ulteriori elementi presenti nell’elettrolita, quali silicio, fosforo, potassio, dato che essi non formano fasi cristalline.
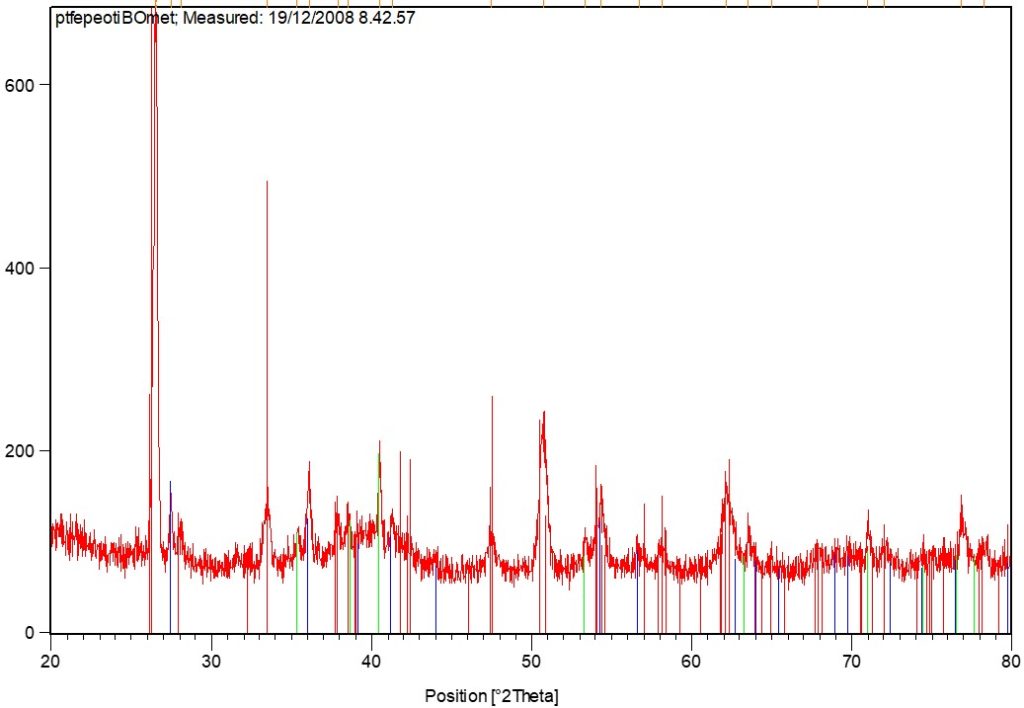
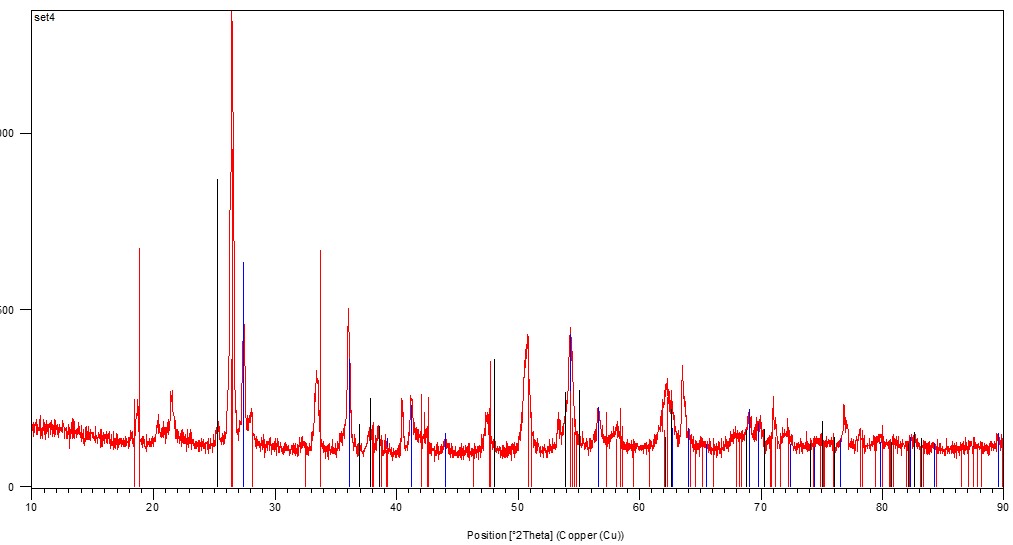
Conclusioni
Si è qui proceduto alla caratterizzazione microstrutturale e tribologica della lega Ti6Al4V, modificata superficialmente mediante ossidazione elettrolitica al plasma (PEO). Lo studio è stato condotto valutando e confrontando l’efficacia di diversi trattamenti PEO al fine di migliorare il comportamento tribologico della lega Ti6Al4V. La caratterizzazione microstrutturale ha permesso di identificare le fasi costituenti i diversi strati PEO (principalmente alluminato di titanio, rutilo ed anatasio), comparare la morfologia superficiale e gli spessori per i diversi strati PEO considerati.
La caratterizzazione tribologica, effettuata utilizzando un tribometro con geometria di contatto pattino su cilindro, in condizioni di strisciamento unidirezionale a secco, impiegando come antagonista un cilindro in acciaio 100Cr6, ha evidenziato come:
- In condizioni stazionarie, i rivestimenti PEO presentano valori medi del coefficiente di attrito superiori rispetto a quelli della lega di titanio non rivestita in tutto l’intervallo di carico considerato, a causa della formazione di strati di trasferimento costituiti da materiale derivante dall’usura tribo-ossidativa a carico dell’antagonista. Solo qualora allo strato PEO venga sovrapposto uno strato lubrificante di PTFE, si osservano valori del coefficiente di attrito inferiori rispetto alla lega Ti6Al4V non trattata.
- Per ciascun trattamento PEO è stato individuato un carico critico, in corrispondenza del quale si verifica il coinvolgimento del substrato nel contatto e quindi la fine della vita utile del rivestimento. In corrispondenza dell’affioramento del substrato, si osserva un innalzamento del tasso di usura ed un calo del coefficiente di attrito ai valori tipici della coppia Ti6Al4V/acciaio.
- In termini di resistenza ad usura, tutti i trattamenti PEO contribuiscono a migliorare le prestazioni della lega Ti6Al4V; tuttavia, data la gradualità del processo di usura (che si sviluppa senza cedimenti coesivi né adesivi dello strato PEO), si registra un significativo incremento della resistenza ad usura per lo strato PEO di maggiore spessore.
Riferimenti
Studio preliminare svolto all’interno del Dipartimento di Ingegneria Industriale dell’Università di Bologna (Rif. Prof.ssa L. Ceschini, Prof. A. Morri) per conto del MATMEC ATS, Laboratorio sui Materiali Avanzati della Rete ad Alta Tecnologia della Regione Emilia Romagna