La pallinatura è, in genere utilizzata per migliorare le prestazioni meccaniche di elementi strutturali metallici sollecitati a fatica. Rare sono le applicazioni a materiali a matrice polimerica. Nel presente lavoro si presenta un nuovo approccio applicativo della pallinatura finalizzato all’ottenimento di texture superficiali controllati per la funzionalizzazione delle superfici.
di A. Heydari Astaraee, S. Bagherifard,* E. A. Rajme López, M. Guagliano, Dipartimento di Meccanica, Politecnico di Milano
La pallinatura (o shot peening, SP) è un trattamento superficiale ampiamente utilizzato in diversi settori industriali, che induce una deformazione plastica non uniforme nello strato superficiale di un componente metallico mediante impatti ripetuti di piccole sfere metalliche, ceramiche, o di vetro. A seguito delle deformazioni plastiche indotte, vengono generate delle tensioni residue di compressione in prossimità della superficie pallinata. Tali sforzi residui sono il principale effetto del trattamento e sono in grado di migliorare le prestazioni meccaniche dei materiali e dei componenti metallici, in particolare per quanto riguarda la fatica. La deformazione plastica induce anche modifiche microstrutturali, con un incrudimento ed indurimento negli strati di materiali prossimi alla superficie e, con opportuni parametri la riduzione delle dimensioni dei grani. Un altro effetto dovuto alla pallinatura, considerato collaterale e, in genere, non voluto, è la modifica della rugosità superficiale e della morfologia della superficie, le quali, se non adeguatamente considerate e controllate, possono indurre una riduzione dei benefici indotti dalla pallinatura se non, in casi estremi, un peggioramento delle prestazioni meccaniche dei materiali trattati. La pallinatura è, nella grande maggioranza dei casi, applicata ai materiali metallici, mentre non sono molti i riferimenti bibliografici relativi ad applicazioni sui materiali polimerici, con risultati a volte contrastanti. Relativamente alla resistenza a fatica, non sempre i risultati pubblicati permettono di concludere che, anche nei casi dei materiali polimerici o dei compositi a matrice polimerica, si abbia un beneficio tale da giustificare l’applicazione di questo trattamento. A volte, anche a causa della difficoltà di scegliere i corretti parametri applicativi, il comportamento a fatica peggiora, in genere per un danneggiamento dovuto alla eccessiva energia cinetica del flusso di sfere e alla conseguente formazione di cricche microscopiche che, propagando, causano la rottura precoce del componente trattato. In un altro studio, invece, la pallinatura è stata applicata a un composito di resina epossidica rinforzato con fibre di vetro: i risultati indicano che la resistenza alla trazione e alla fatica dei substrati migliora di circa il 30-60% con determinati valori di copertura. Ancora, la pallinatura è stata applicata come processo interstrato per la produzione additiva (AM) di acrilonitrile butadiene stirene (ABS): i risultati hanno mostrato che questo approccio di fabbricazione è efficace per migliorare le proprietà dinamiche testate con test tipo Charpy o di caduta del peso. Tuttavia, ha causato una riduzione della rigidezza del materiale. In sintesi, a causa della natura stessa di questi materiali, non si può affermare che gli effetti indotti su di essi siano comparabili a quelli ottenibili su materiali metallici. Tuttavia, le caratteristiche intrinseche di questi materiali portano anche a pensare che la pallinatura possa essere comunque utilizzata per modificare la loro morfologia superficiale. In altre parole, quello che viene usualmente considerato un effetto collaterale, la modifica della rugosità e della morfologia della superficie, può diventare il motivo per cui eseguire la pallinatura sui materiali polimerici, per generare un “pattern” superficiale controllato, in grado di funzionalizzare la superficie rispetto a predefinite applicazioni in vari settori industriali che fanno riferimento alla ingegneria delle superfici. Il che vuol dire che la pallinatura potrebbe essere utilizzata per definire “texture” superficiali con caratteristiche che migliorano le funzionalità superficiali. Queste possono includere, ad esempio, la resistenza ai graffi e all’abrasione, le proprietà tribologiche, le caratteristiche biologiche, la bagnabilità e la capillarità, l’estetica e la lucentezza. Attualmente ci sono diverse tecniche utilizzate allo scopo; tra questa l’incisione a fascio ionico, la lavorazione elettrochimica, la microfresatura, la litografia, la lavorazione laser. L’idea alla base di questo studio è valutare il potenziale della pallinatura come trattamento da utilizzare per il texturing meccanico della superficie dei polimeri, inducendo deformazioni plastiche superficiali tramite pallini con una superficie personalizzata. A differenza di molte altre tecniche, la pallinatura non comporta la rimozione di materiale, non richiede alte temperature o pressioni, ed è relativamente veloce, economica e sostenibile, con un alto potenziale di industrializzazione. La necessità di personalizzare i pallini potrebbe aumentare i costi complessivi, ma esistono macchine utilizzate per la pallinatura alternative, che possono mitigare questo aspetto. Nel presente studio, si sono esplorate le potenzialità della pallinatura in questo contesto, valutando la possibilità di realizzare il texturing superficiale dell’ABS utilizzando pallini personalizzati realizzati tramite produzione additiva (AM). Vengono proposti diversi design, e le texture superficiali create sono studiate sia numericamente che sperimentalmente in termini di morfologia e rugosità superficiale standard.
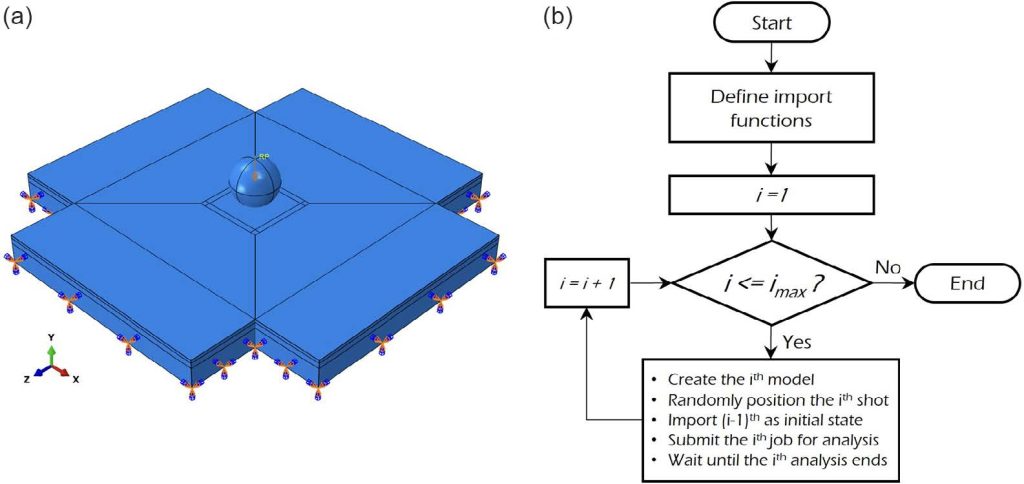
Progettazione delle sfere
Tradizionalmente, per la pallinatura si utilizzano pallini sferici, semisferici o in filo tranciato (cilindrici) con dimensioni tipiche inferiori a 1 mm. Più di recente, pallini più grandi (da 1 a 10 mm di diametro) sono stati impiegati in tecniche di nanostrutturazione superficiale derivate dalla pallinatura, come la pallinatura ultrasonica (USP), nota anche come trattamento meccanico di attrito superficiale (SMAT). Poiché nella pallinatura è l’energia cinetica del flusso di sfere a deformare la superficie, per creare texture superficiali personalizzate è necessario progettare pallini 3D con pattern complessi. In questo studio sono stati sviluppati e applicati diversi design di pallini personalizzati. L’idea è quella di indurre una deformazione superficiale gerarchica, creando piccoli avvallamenti all’interno di una più grande indentazione sferica. A tal fine, sono state aggiunte caratteristiche innovative, come protuberanze o incavi, ai pallini sferici di base. I design proposti sono stati testati tramite modelli agli elementi finiti (FE) per garantire che la superficie polimerica venisse lavorata in modo omogeneo, senza deformazioni eccessive. Le forme di base erano sferiche, con caratteristiche geometriche aggiunte sulla superficie. I nomi dei pallini proposti si ispirano al risultato atteso, come sfera, pallone da calcio, multibumps, pallina da golf, icosaedro, reticolo e quadrato (Figura 1). La fusione laser a letto di polvere (LPBF) è considerata la tecnica candidata per la produzione di questi “pallini personalizzati”. Pertanto, durante la progettazione delle geometrie delle sfere, si sono presi in considerazione i limiti di produzione del processo di fusione laser a letto di polvere (LPBF). Tutti i design proposti avevano un diametro complessivo di circa 8 mm. Il design del pallone da calcio, che era un icosaedro troncato, aveva un diametro interno di 7 mm e un raggio di raccordo di 0,1 mm. Il pallino multibumps era costituito da protuberanze con un diametro e un’altezza massima rispettivamente di 1,3 mm e 0,25 mm. Il pallino da golf era una variante del pallino multibumps, costituito da un nucleo sferico solido con fossette sulla sua superficie. Questo pallino era pensato per creare piccoli rigonfiamenti sulla superficie polimerica trattata. Il nucleo sferico aveva un diametro di 8 mm, e le fossette erano posizionate a 3,8 mm dal centro della sfera, con un diametro di 1,7 mm e un raggio di raccordo di 0,25 mm. Il pallino a reticolo aveva una transizione geometrica lungo le diverse zone, partendo da triangoli, passando per rombi curvi e terminando con quadrati. La sua geometria era costituita da un nucleo sferico solido di 7,6 mm e una serie di anelli incrociati sulla superficie con un raggio di 0,5 mm. Tutti i raccordi avevano un raggio di 0,1 mm. Infine, anche nel pallino con motivo a quadrati, è stata sfruttata la transizione tra figure geometriche. Tuttavia, invece di utilizzare un reticolo di anelli, linee nette definivano la transizione dai triangoli nella parte superiore ai quadrati nella parte centrale. Questo design era costituito da un nucleo simile a una gemma con tagli in bassorilievo e angoli smussati di 75°.
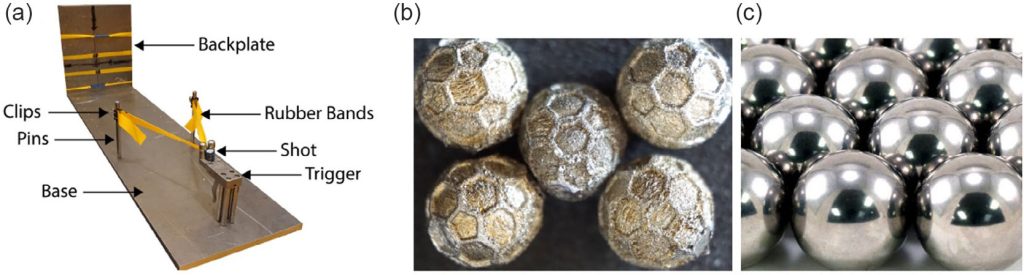
Analisi numerica
Le simulazioni numeriche sono state eseguite utilizzando il software Abaqus, con una procedura dinamica esplicita che consente di analizzare brevi eventi dinamici transitori con risultati accurati. Le caratteristiche geometriche del modello sono mostrate nella Figura 2a. Le geometrie dei pallini sono state create utilizzando SolidWorks e importate in Abaqus. Successivamente, sono state convertite in solidi rigidi per ridurre i tempi di calcolo. Questa ipotesi è valida a causa della grande differenza di rigidità tra i pallini in acciaio e il substrato polimerico. Il substrato è stato modellato usando una lastra con dimensioni di 40 × 40 × 5 mm³. Lo spessore è stato assegnato in base allo spessore del foglio di materiale reale utilizzato negli esperimenti. L’area d’impatto è stata selezionata per essere pari a 10 × 10 mm² ed è posizionata al centro del modello di substrato. Sono stati introdotti elementi semi-infiniti nelle quattro facce laterali del substrato per modellare un corpo di grandi dimensioni e ridurre l’effetto delle onde elastiche di sforzo riflesse dai bordi, mentre tutte le condizioni al contorno traslazionali e rotazionali della faccia inferiore sono state fissate. Il bersaglio è stato modellato utilizzando elementi 3D di tipo C3D8R ed elementi infiniti di tipo CIN3D8, mentre i pallini sono stati modellati utilizzando elementi S4R. Dopo uno studio di convergenza della mesh, la dimensione degli elementi sui pallini e nell’area d’impatto è stata selezionata pari a 0,04 mm. La massa dei pallini è stata definita utilizzando una densità di 7,8 g/cm³. Il comportamento viscoplastico del polimero ABS è stato implementato utilizzando il modello di plasticità di Johnson–Cook, come elencato nella Tabella 1. Le velocità di impatto dei pallini, sia nella pallinatura pneumatica c nella pallinatura centrifuga, sono comunemente selezionate nell’ordine di 20–150 m/s a seconda del materiale del mezzo e del substrato e dell’intensità di Almen desiderata. Tuttavia, i pallini grandi (8 mm di diametro) considerati nello studio attuale non possono essere utilizzati nella pallinatura classica e la velocità imposta deve essere adattata alle dimensioni dei pallini. La dimensione del pallino selezionata è più adatta per i casi di USP e SMAT, che utilizzano pallini nel range di 1–10 mm di diametro per trattare il materiale e indurre il raffinamento dei grani nello strato superficiale. La velocità media dei pallini in questi processi è stata stimata essere nell’intervallo di 1–10 m/s a seconda dei parametri di lavorazione. Basandosi su quanto descritto nelle righe precedenti, è stata selezionata una velocità costante dei pallini pari a 10 m/s, assegnata ai pallini come condizione al contorno iniziale nelle simulazioni. Inoltre, per esplorare l’effetto di una velocità inferiore sulla rugosità e sulla texture superficiale, sono state effettuate simulazioni per due dei pallini personalizzati (reticolo e motivo quadrato) utilizzando anche una velocità di impatto di 5 m/s. L’angolo di impatto è stato impostato a 90° rispetto all’area d’impatto in tutti i casi, come è tipico per la pallinatura. Per ottenere un’idea riguardo al numero di impatti richiesti e alla sua relazione con la copertura della pallinatura, è stato utilizzato il modello di Kirk–Abyaneh.
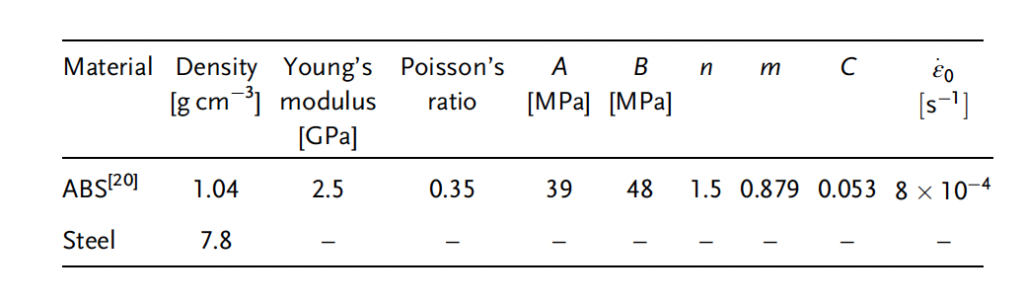
Questo modello utilizza la dimensione delle fossette prodotte da un singolo impatto di pallino sulla superficie del bersaglio per stimare il numero necessario di impatti per raggiungere la copertura di pallinatura desiderata (i dettagli dei calcoli possono essere trovati in uno studio precedente). Il modello di impatto multiplo è stato creato utilizzando uno script Python, il cui schema è indicato nella Figura 2b. In questo script, è stato creato un modello di impatto a singolo pallino con un pallino posizionato casualmente, e i risultati dell’impatto precedente sono stati importati in questo modello. Ogni modello a singolo impatto è stato eseguito fino al completamento dell’impatto e al distacco del pallino dal substrato dopo il rimbalzo. Questo ciclo è stato continuato fino a simulare il numero necessario di impatti per raggiungere una copertura superficiale prestabilita. Per una simulazione realistica del processo di pallinatura, oltre a considerare le posizioni di impatto casuali dei pallini definendo le coordinate sulla superficie d’impatto, è stata considerata anche una rotazione angolare casuale attorno ai loro assi.
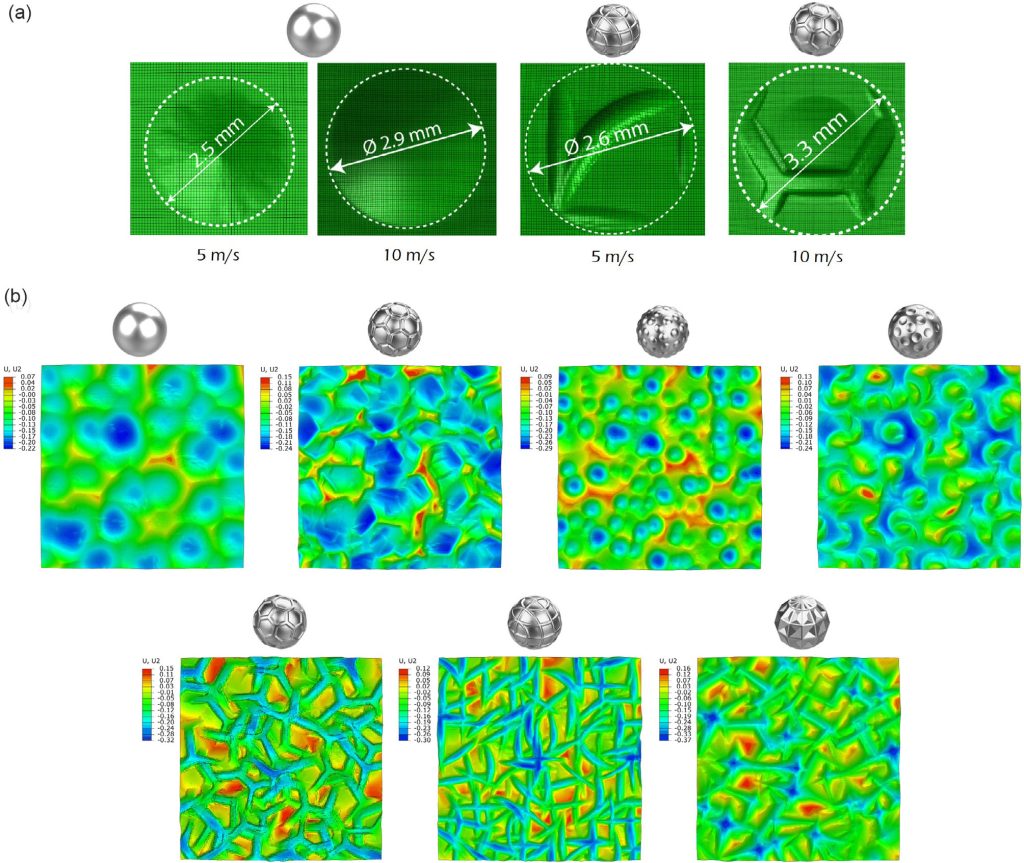
Prove sperimentali
Sono stati eseguiti una serie di test sperimentali preliminari basati su un semplice sistema a fionda per verificare la correttezza concettuale di quanto proposto. La Figura 3a mostra l’allestimento del banco prova e i componenti correlati. La fionda utilizzava una piastra in alluminio come base per fissare i perni e il grilletto. L’elastico era posizionato attorno ai perni e tenuto in posizione con clip.
Una piastra posteriore è stata installata alla fine della base dove il bersaglio polimerico (spessore di 5 mm) era posizionato e fissato. Sono state considerate due geometrie di pallini diverse: pallini personalizzati a forma di icosaedro realizzati con tecnologia LPBF utilizzando polvere di acciaio inox 316 e sfere di cuscinetti a sfere in acciaio inox AISI 316 di 8 mm di diametro, come riferimento (Figure 3b, 3c).
Il principio di conservazione dell’energia è stato utilizzato per stimare la velocità di impatto del pallino. Sono state considerate alcune ipotesi, come l’assenza di resistenza aerodinamica, nessun cambiamento nella posizione verticale e nessuna perdita di calore, per facilitare i calcoli. L’energia totale del sistema è la somma dell’energia potenziale immagazzinata nell’elastico e dell’energia cinetica del movimento. Il fenomeno può essere suddiviso in due stati: il primo è il pallino immobile (energia cinetica zero) tirato all’indietro a una distanza determinata, che crea tensione nell’elastico, e il secondo è il pallino in volo completamente staccato dagli elastici (energia potenziale zero). La conservazione dell’energia meccanica afferma che l’energia nello stato uno è, a meno delle dissipazioni, equivalente all’energia meccanica nello stato due. Sono stati utilizzati un dinamometro e un metro a nastro per determinare sperimentalmente la relazione tra forza e l’allungamento dell’elastico.
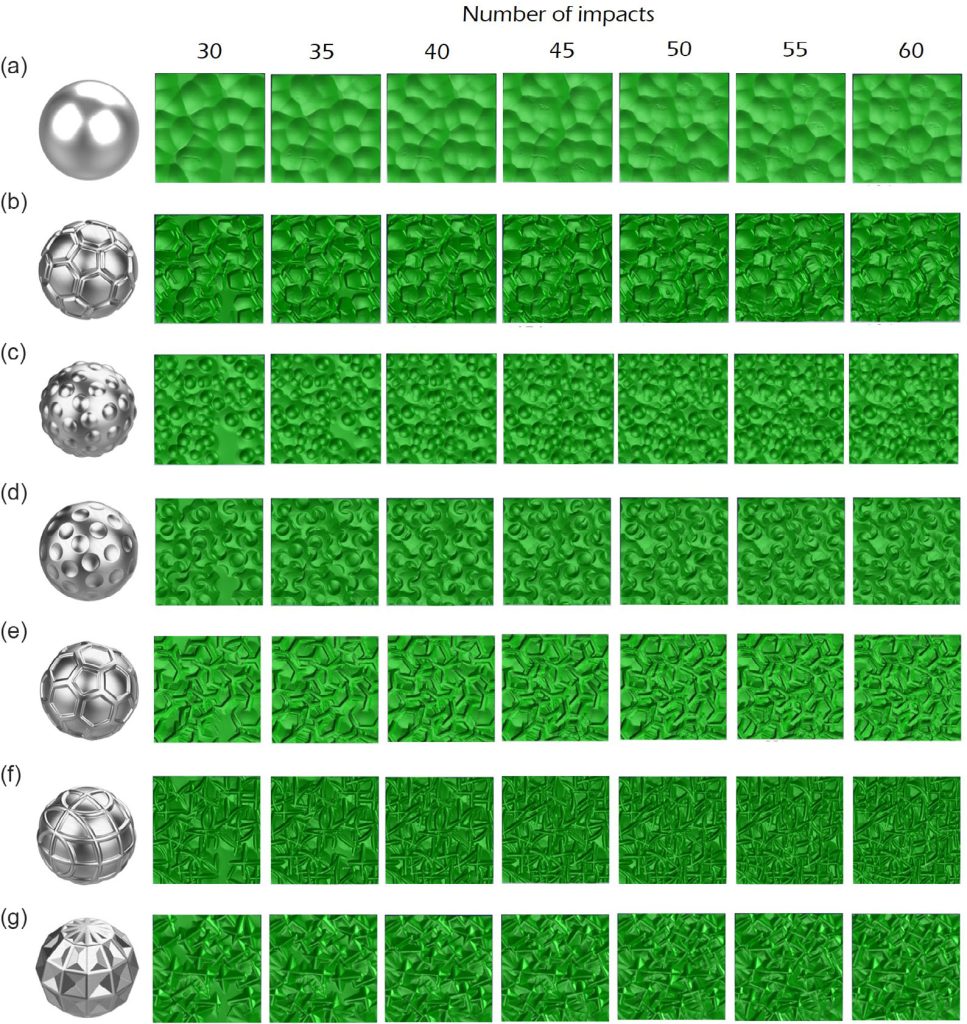
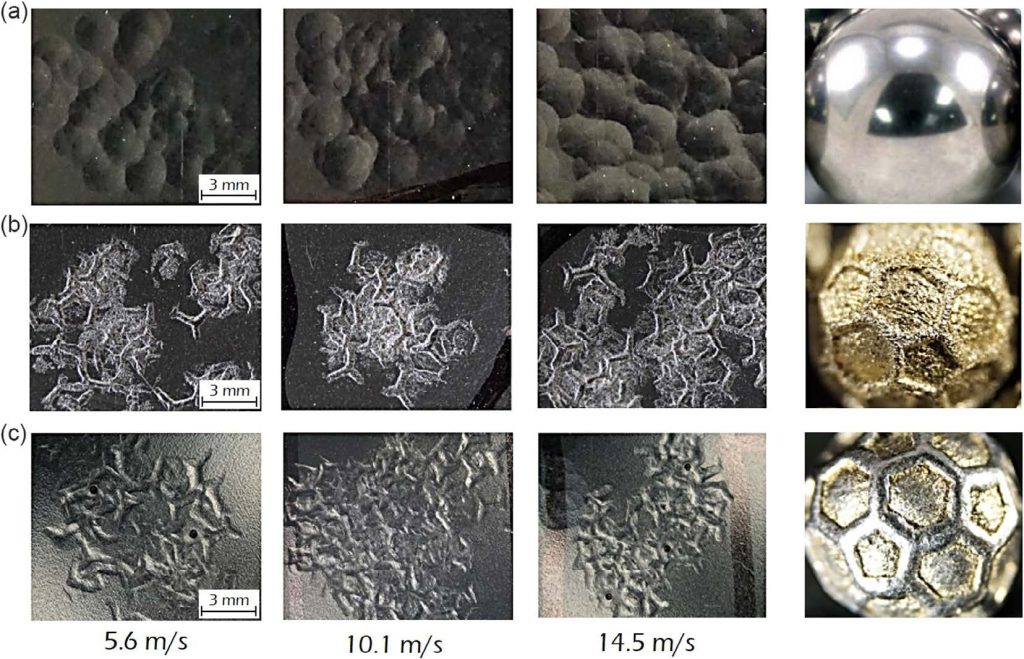
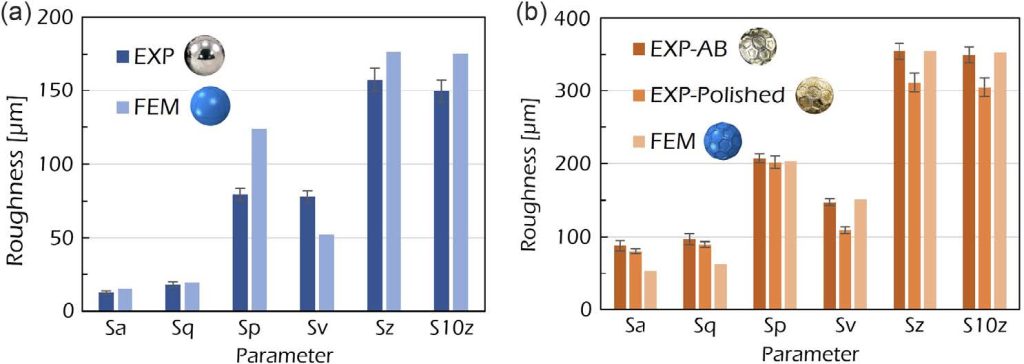
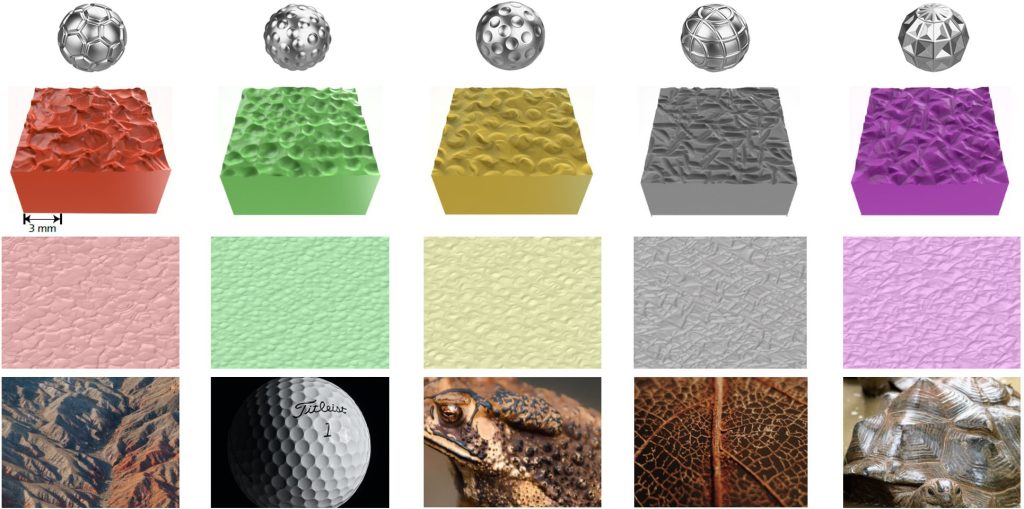