Con l’affermarsi della mobilità elettrica, il problema del rumore generato dalle trasmissioni è diventato sempre più pressante. Una corretta finitura contribuisce a vincere la sfida.
Nell’industria dell’autotrazione, minor rumore è quasi sinonimo di migliore qualità. È sostanzialmente per questi motivi che la lotta al rumore è proseguita con ritmo incessante per molti anni, con risultati eccellenti.
L’origine e la trasmissione del rumore prodotto da una coppia di ingranaggi, o più precisamente, il rumore che esce da una scatola cambio o da un riduttore o da un ruotismo qualsiasi, è un fenomeno tra i più studiati e analizzati nel settore della meccanica.
In effetti, bisognerebbe più propriamente parlare di rumore delle trasmissioni piuttosto che rumore degli ingranaggi, perché le vibrazioni indotte da un imperfetto ingranamento sono trasmessi, amplificate o attenuate attraverso i corpi degli ingranaggi, ai supporti degli alberi, ai cuscinetti e infine alla carcassa della scatola cambio.
Quindi, è tutto il sistema che viene coinvolto in questo fenomeno e, schematizzando, si può affermare che la strada che il rumore segue sia la seguente:
- eccitazione da ingranamento;
- vibrazioni torsionali e laterali e risonanza del corpo degli ingranaggi;
- forze dinamiche di ingranamento e sui cuscinetti;
- interazione tra cuscinetti e scatola;
- vibrazioni della scatola;
- superfici radianti e altri percorsi delle vibrazioni;
- rumore finale generato e percepito.
Molta importanza ha l’analisi delle frequenze che compongono il rumore.
L’onda sonora percepita dall’orecchio umano è composta da una serie di frequenze che si sovrappongono alla frequenza primaria; si tratta delle varie armoniche di intensità più o meno grande, che possono venire rappresentate da una serie di Fourier. Esse determinano il carattere del suono trasmesso.
La frequenza primaria (o frequenza di ingranamento), è funzione del numero di denti dei due ingranaggi e dalla velocità di rotazione (numero di giri); essa si calcola con le seguenti formule:
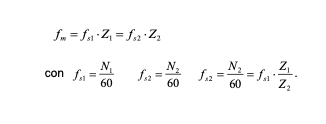
dove:
fs1 = frequenza dell’albero conduttore
fs2 = frequenza dell’albero condotto
fm = frequenza di ingranamento
N1 , N2 , Z1 , Z2 = sono rispettivamente il numero di giri ed il numero di denti della ruota conduttrice e di quella condotta.
L’analisi delle armoniche permette di individuare, in certi casi, l’origine delle vibrazioni.
Se per esempio il rumore ha origine da un errore su un singolo dente, la frequenza della vibrazione sarà definita dal numero di giri dell’ingranaggio con errore, mentre se il rumore dipende da una imperfezione su tutti i denti dell’ingranaggio, la frequenza delle vibrazioni sarà Z volte maggiore.
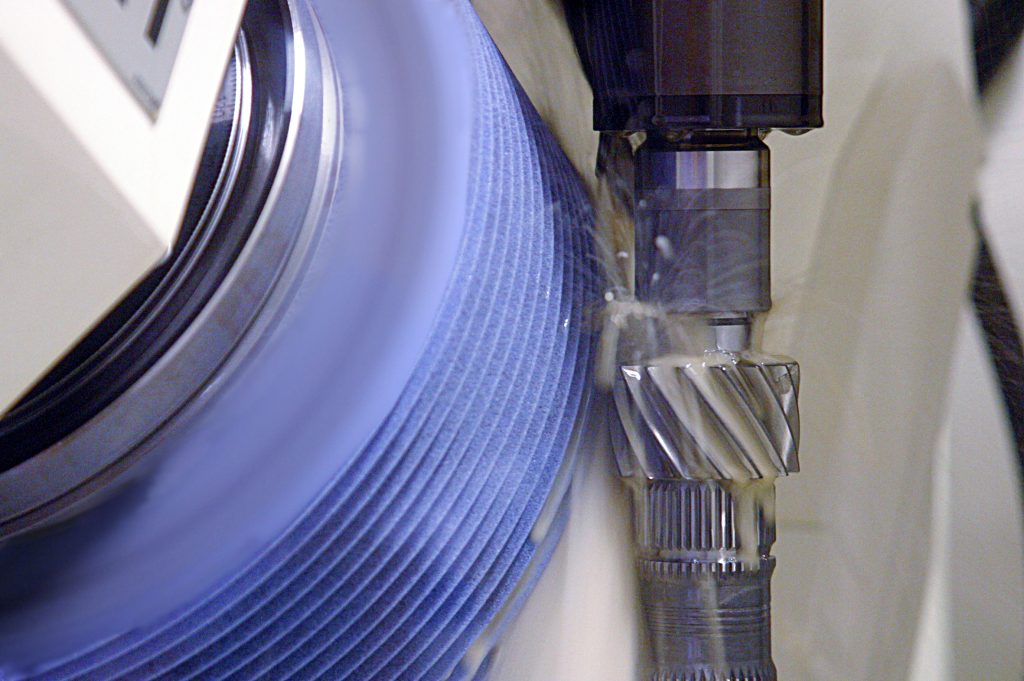
Principali cause di generazione del rumore
Gli elementi più importanti che generano rumore durante il funzionamento di un accoppiamento tra due ingranaggi sono abbastanza bene individuati e sono i seguenti.
- Variazione della rigidezza di ingranamento. Per rigidezza di ingranamento si intende il rapporto tra la forza tangenziale lungo la retta d’azione e la flessione del dente in quella direzione. Bisogna notare che la forza applicata su un dente è variabile come intensità, come direzione e come punto di applicazione. Ne consegue che la flessione del dente è continuamente variabile. Il caso più eclatante si verifica negli ingranaggi a denti dritti, con rapporto di condotta inferiore a 2. In questo caso si alternano due coppie di denti in presa con una sola coppia; si può facilmente intuire la forte variazione di carico e di flessione su ogni singolo dente.
Questa condizione è evidentemente da evitare. Normalmente essa può verificarsi solo con accoppiamenti di ingranaggi a denti dritti, mentre sugli ingranaggi a denti elicoidali il rapporto di condotta totale è generalmente superiore a 2, per cui si hanno sempre almeno due coppie di denti in presa.
Si distinguono quindi gli ingranaggi LCR (Low Contact Ratio), cioè ingranaggi con un rapporto di ricoprimento inferiore a 2, e gli ingranaggi HCR (High Contact Ratio), cioè ingranaggi con rapporto di ricoprimento superiore a 2.
- Errore di trasmissione. È la differenza tra la posizione effettiva dell’ingranaggio condotto e la posizione che esso occuperebbe nel caso di una coniugazione perfetta. È il fattore principale nella generazione del rumore. Si può misurare come deviazione angolare o come spostamento lineare lungo la linea d’azione. Esso si distingue inoltre in due componenti: errori di costruzione ed errori generati dal carico.
- Urti fra i denti. Si verificano quando le deformazioni o gli errori di passo provocano un contatto prematuro con il dente che sta per entrare in presa. Il contatto avviene fuori dalla retta d’azione e può risultare di una forza dinamica elevata che oltre ad elevare il livello della pressione sonora alla frequenza di ingranamento, può ridurre la vita dell’ingranaggio.
- Forze dinamiche di ingranamento. Sono il risultato delle variazioni di rigidezza di ingranamento e degli errori di trasmissione. Queste forze, variabili nel corso della rotazione, attraverso i cuscinetti ed i supporti eccitano delle vibrazioni nella carcassa. Queste vibrazioni, se hanno frequenza uguale o prossima a quella di risonanza propria della carcassa, vengono amplificate e costituiscono una fonte importante di rumore.
- Forze di attrito. Come è noto, l’accoppiamento di due profili ad evolvente è un puro rotolamento solo in corrispondenza del diametro primitivo. Nelle zone sopra e sotto il diametro primitivo si ha uno strisciamento in direzione dell’altezza del dente, in un senso sopra e nel senso opposto sotto. Quando la direzione della forza d’attrito si inverte si può innescare una vibrazione che è più evidente negli ingranaggi a denti dritti. Negli ingranaggi elicoidali, questo fenomeno è, in genere, trascurabile.
- Air Pocketing (soffi d’aria). È il rumore generato dalla rapida compressione dell’aria provocata dai denti durante l’ingranamento. Per ingranaggi veloci, la velocità dell’aria si può avvicinare a quella del suono, provocando rumori di forte intensità alla frequenza di ingranamento.
- Compressione del lubrificante. Se i giochi tra i fianchi e sul fondo dente non sono sufficienti, il lubrificante può rimanere compresso tra i due ingranaggi. Quando viene espulso genera rumore, specie se colpisce le pareti della carcassa.
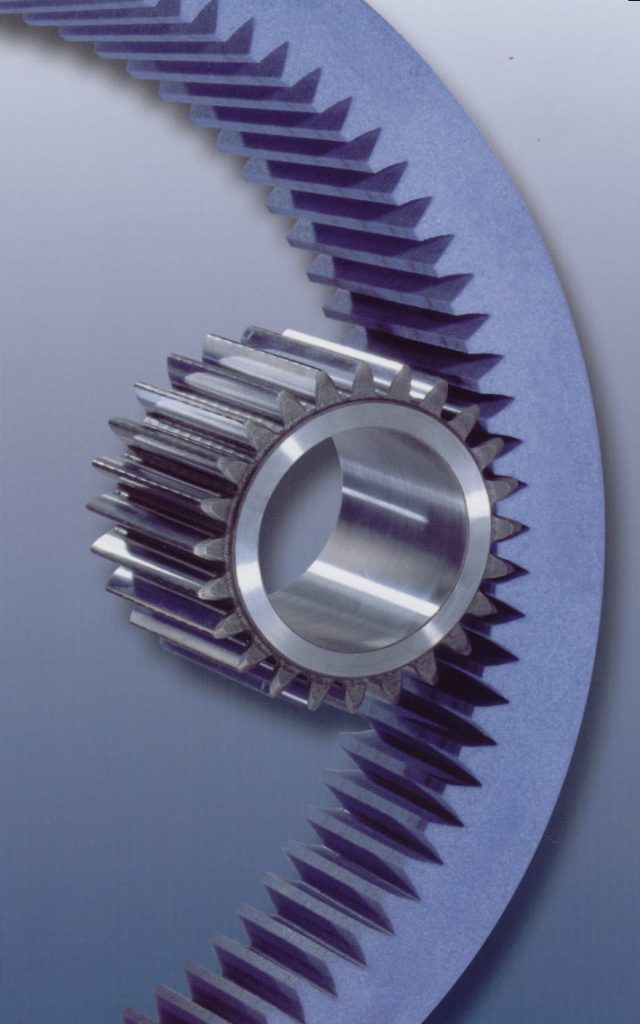
Considerazioni sulla potenza trasmessa
In una certa misura il rumore generato da una trasmissione, per esempio un riduttore di grosse dimensioni, dipende dalla potenza trasmessa.
La potenza irradiata sotto forma di rumore, è accertato sperimentalmente, è di circa 10-9 della potenza trasmessa; questo a patto che il riduttore sia perfetto, cioè che sia progettato in modo corretto e che i denti siano opportunamente modificati per rendere minimo l’errore di trasmissione. Si può definire l’efficienza acustica con:
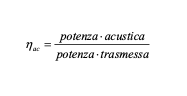
Quando si raddoppia la potenza trasmessa si ha un aumento di circa 3 dB del rumore.
Però la potenza si può aumentare o aumentando la velocità o aumentando la coppia.
Molti ricercatori sono concordi nel dire che un raddoppio della velocità aumenta il rumore di 5-7 dB (mediamente).
È necessario però che la frequenza di ingranamento non coincida con la frequenza di risonanza del sistema, molto meglio se essa coincide con la frequenza di antirisonanza. Nel primo caso si avrebbe un forte aumento della rumorosità, mentre nel secondo ci sarebbe una forte riduzione.
Il raddoppio della coppia fa crescere il livello sonoro di 3 dB (ma per alcuni ricercatori l’aumento può arrivare a 5-6 dB).
Si è detto che per effetto degli errori di costruzione e del carico, che il più delle volte è variabile, si hanno forti errori di ingranamento.
Questi errori possono essere attenuati con opportune modifiche del profilo e dell’elica, rendendo l’accoppiamento più silenzioso.
Considerazioni sugli ingranaggi ad alto rapporto di ricoprimento (HCR)
Con questo tipo di ingranaggi il carico sui singoli denti è molto più costante e quindi, complessivamente, la trasmissione risulta più silenziosa.
Per ottenere l’allungamento della linea d’azione si può aumentare il diametro di fine evolvente, cioè aumentando il diametro esterno e diminuendo l’angolo di pressione normale. Se è possibile bisognerebbe ridurre anche il modulo.
Tutte queste modifiche del progetto dell’ingranaggio, se è vero che riducono il carico su ogni singolo dente, è anche vero che hanno qualche effetto negativo.
In primo luogo, se il dente si allunga e si assottiglia, riduce la sua resistenza alla flessione.
Uno degli svantaggi degli ingranaggi ad evolvente è la rapida diminuzione del raggio di curvatura del profilo in prossimità del cerchio di base.
Così, la sollecitazione di contatto tra i denti in presa è inversamente proporzionale al raggio di curvatura e subisce un rapido incremento quando questo diventa piccolo
Non solo la sollecitazione di contatto aumenta a mano a mano che il punto di contatto si avvicina al cerchio di base, ma anche la velocità di strisciamento aumenta, aumentando il rischio di “scoring”, che è funzione della pressione di contatto e della velocità di strisciamento.
Tutto ciò comporta un maggiore rischio per gli ingranaggi HCR che non per le dentature con dimensionamento normale.
Un’ultima osservazione: questi ingranaggi sono più sensibili agli errori di costruzione, e quindi le tolleranze di fabbricazione devono essere più strette.
Esaminiamo ora la relazione esistente tra gli errori di trasmissione e il rumore.
Gli errori di trasmissione si possono dividere in due categorie:
- MTE: Manufactured Transmission Error
- LTE : Loaded Transmission Error
Gli MTE sono gli errori di trasmissione indotti dagli errori di profilo, di passo, di eccentricità e, in minor misura, di elica.
Questi errori, che sono lo scostamento dei parametri effettivi da quelli teorici, dipendono dall’ovvia impossibilità pratica di ottenere in costruzione un ingranaggio teoricamente perfetto.
Il rilievo di questi errori, presi singolarmente, si fa in genere con un apparecchio a CN che fornisce i grafici ed i valori di tutti i parametri.
L’errore di ingranamento, preso nel suo insieme e generato dalle imperfezioni geometriche di cui sopra, si può rilevare invece con un ingranometro monofianco senza carico.
Questo tipo di apparecchio, che fornisce un diagramma del tipo di figura 3, permette di individuare anche il maggiore tra gli errori di passo, l’eccentricità e la presenza di eventuali ammaccature.
Oltre all’assenza del carico, i limiti sono costituiti dal fatto che o si usa un ingranaggio master che accoppia con l’ingranaggio da controllare o si usa una controruota.
In entrambi i casi si sommano i loro errori a quelli della ruota che si vuol controllare.
È ben vero che ci sono dei software che permettono di separare in qualche modo gli errori della ruota da quelli della controruota, ma i risultati sono sempre un po’ approssimati e soggetti a qualche limitazione.
La norma DIN 3960 definisce gli errori di ingranamento rilevati con l’ingranometro con un singolo fianco a contatto.
Alcuni ricercatori hanno dimostrato che c’è una relazione diretta tra l’errore di trasmissione di costruzione e il rumore e, in generale, è stato trovato che un raddoppio del MTE provochi un aumento del rumore di 6-8 dB.
Effetto del profilo dei denti
L’errore di profilo è uno dei principali motivi dell’errore di trasmissione e quindi del rumore.
Il salto f’k , (figura 3), è principalmente il risultato degli errori di contatto di una singola zona dei denti. Tuttavia bisogna osservare che non sarebbe corretto addebitare la rumorosità solo a questa imperfezione in quanto in realtà diventa importante la flessione del dente sotto carico che, in un certo senso, cambia le carte in tavola.
In ogni caso l’errore di profilo aumenta l’intensità del livello sonoro alle frequenze di ingranamento ed alle sue armoniche.
Bisogna infine notare che è generalmente ritenuta molto dannosa una concavità del profilo, specie se questa si trova in prossimità del diametro primitivo.
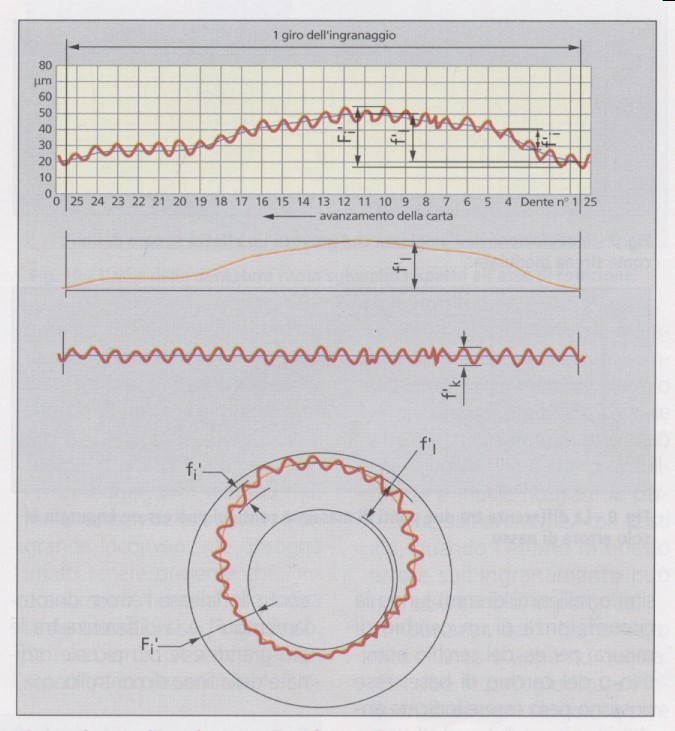
Figura 3 – Diagramma dell’errore di trasmissione ottenuto con un ingranometro monofianco
- Errori di rotolamento di un fianco F’iErrore somma di rotolamento f’lErrori singolo di rotolamento f’kSalto di rotolamento f’i
Errore di passo singolo
L’errore di passo singolo si manifesta con un salto a gradino dell’errore di trasmissione per un determinato dente.
Non ha quindi un andamento regolare e progressivo, ma ha una distribuzione casuale.
È tipico il caso di un ingranaggio che accumula un piccolo errore di divisione su ogni dente arrivando all’ultimo dente con un errore cumulato notevole.
Questo tipo di errore non produce un incremento del rumore sulla frequenza di ingranamento, né sulle sue armoniche, esso provoca un secco rumore per ogni giro, analogamente al caso di un ingranaggio con un dente rotto o con una grave anomalia.
Un rumore analogo è provocato da un’ammaccatura sugli spigoli laterali o su quello di testa. Questo problema è abbastanza frequente.
Errore di eccentricità
L’eccentricità causa una frequenza di eccitazione con un ciclo per ogni giro della rotazione della ruota. Presa a sè stante questa frequenza non è udibile, ma essa spesso causa una modulazione dell’ampiezza della frequenza di ingranamento, provocando un fastidioso “effetto sirena”.
Disallineamento ed errori di elica
Il disallineamento dell’albero e l’errore dell’angolo dell’elica hanno come effetto di spostare il contatto all’estremità dei denti. In questo caso la larghezza della fascia dentata effettiva si riduce, causando la riduzione della somma delle lunghezze delle linee di contatto con un conseguente aumento dell’errore di trasmissione.
Questo effetto è più marcato nel caso degli ingranaggi elicoidali in quanto il loro comportamento si avvicina a quello degli ingranaggi a denti dritti.
Se l’errore di allineamento è grave si ha uno spostamento del carico all’estremità del dente con conseguenze pesanti sulla rumorosità e gravi pericoli di rottura o riduzione della durata.
È raro che gli errori totali di allineamento, considerando i due ingranaggi, siano inferiori a 10 micron.
Per annullare gli effetti di questi errori su usa modificare l’elica eseguendo la cosiddetta
bombatura dell’elica.
Gli LTE sono errori di trasmissione attribuibili al carico. Si possono considerare due componenti di questo errore:
- una componente costante dovuta al cedimento medio del dente. Questa componente determina in gran parte le modifiche di profilo, ma non è molto significativa agli effetti del rumore alla frequenza di ingranamento.
- una componente variabile nel tempo in funzione della geometria del dente, della variazione della rigidezza d’ingranamento e degli errori di costruzione. Influisce molto sulla rumorosità alla frequenza di ingranamento.
Negli ingranaggi a denti dritti la rigidezza d’ingranamento è circa proporzionale al numero di coppie di denti in contatto. Se nella rotazione cambia il numero di punti di contatto, cambia la rigidezza e quindi anche l’errore di trasmissione.
Se, per esempio, il rapporto di condotta è 1,60, si ha per il 60% un contatto su 2 coppie e per il 40% il contatto su una coppia.
Il carico ammesso su ogni singolo dente è approssimativamente di 100 N per ogni mm di modulo e per ogni mm di larghezza della fascia dentata.
Se consideriamo un ingranaggio a denti dritti con modulo 4 mm e larghezza fascia di 25 mm il carico totale ammesso sarà quindi di 10.000 N (1000 kg).
In queste condizioni la flessione del dente può arrivare fino a 28 micron, solo per effetto del carico.
Se il carico resta costante è possibile, con opportune modifiche del profilo, compensare questa flessione, ma se il carico su ogni dente è variabile, ciò diventa alquanto problematico.
Quali sono allora i sistemi per eliminare o almeno ridurre questi inconvenienti?
Il primo, lo si è già detto, è quello di aumentare il rapporto di condotta in modo che le coppie di denti in contatto siano sempre almeno due.
Questo si può fare o con l’aumento dell’altezza del dente e la contemporanea riduzione dell’angolo di pressione, ottenendo le dentature ad alto rapporto di ricoprimento (HCR: High Contact Ratio) oppure, caso di gran lunga più frequente, con l’adozione di ingranaggi elicoidali che, tra l’altro, hanno anche altri vantaggi rispetto a quelli a denti dritti.
Negli ingranaggi a denti elicoidali, il rapporto di condotta (o di ricoprimento) è uguale alla somma del rapporto di condotta relativo al profilo e a quello relativo all’elica.
Per compensare le flessioni dovute al carico si eseguono le spoglie in testa del dente.
Si tratta di togliere materiale in prossimità della testa del dente in modo da evitare l’urto tra i denti quando questi stanno per entrare in presa.
Si possono distinguere due tipi di spoglia:
1. Long relief (Spoglia lunga).
Se si suppone che con una coppia di denti in contatto la rigidezza d’ingranamento sia metà rispetto a due coppie di denti in contatto si può trovare una modifica del profilo che renda minimo l’errore di trasmissione per un determinato carico. La modifica si può applicare solo sul profilo in prossimità della testa dell’ingranaggi o scegliere di modificare il profilo un po’ verso la testa ed un po’ verso il piede. Si ottiene così il classico profilo a K, come indicato nella figura 4. Le applicazioni indicate sono per carichi abbastanza costanti: pompe, compressori, ventilatori, convogliatori, ecc.
- Short relief (Spoglia corta).
Si utilizza quando i problemi di rumorosità sorgono con carichi molto minori del carico nominale. Spostando l’inizio della modifica verso la testa (o verso il piede), si può scegliere come carico ottimale (rumore minimo) un carico a scelta tra zero ed il massimo. Nel caso di carichi fortemente variabili (ad esempio, i cambi automobilistici) si deve procedere per tentativi avvicinandosi gradualmente alle modifiche che rappresentano un accettabile compromesso per tutti i carichi.
Per concludere la trattazione di questo argomento, si può esaminare l’influenza delle lavorazioni e delle relative precisioni sulla rumorosità degli ingranaggi.
Da quanto esposto si può capire che, quasi sempre, l’ingranaggio con un profilo teorico non va bene. È richiesta sempre una modifica del profilo e dell’elica per ottimizzare il rumore, cioè per compensare sia gli errori di fabbricazione (profilo, passo, eccentricità, elica e allineamento), sia per compensare le flessioni del dente dovute al carico.
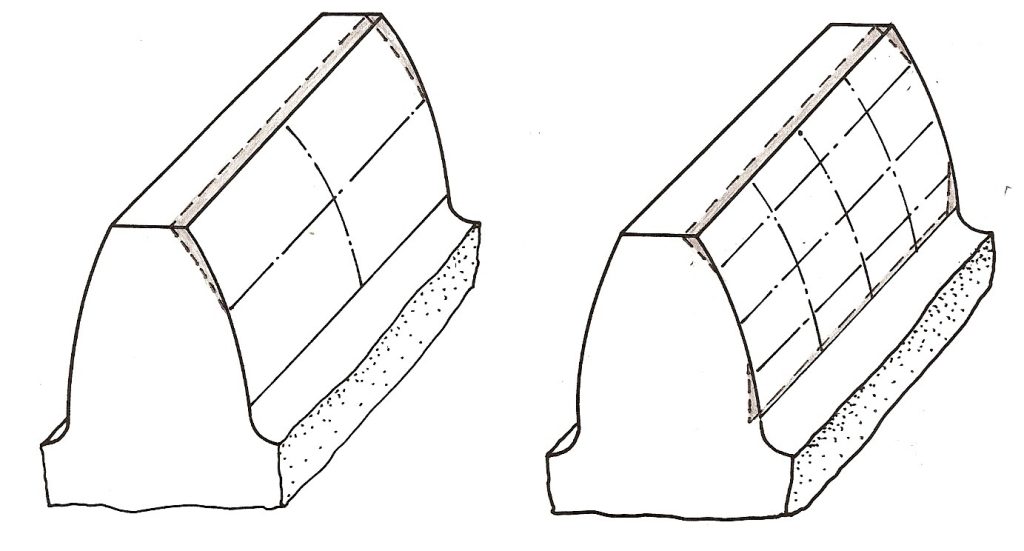
Poiché gli errori di fabbricazione, anche se restano dentro a determinate tolleranza, sono del tutto casuali, costituiscono un fattore di incertezza nel risultato che una determinata modifica di profilo può avere.
Ne consegue che più l’ingranaggio, nel suo insieme, è preciso, più probabilità ci sono di “centrare” le modifiche del profilo ottimali.
Il discorso a questo punto sembrerebbe esaurito, ma se quanto detto potrebbe essere sufficiente per una buona parte di ingranaggi di modulo medio-piccolo usati dall’autotrazione e in molti riduttori ed in altri impieghi non particolarmente impegnativi, non è certo sufficiente se si considerano ruotismi di grosso modulo che devono trasmettere potenze elevate, magari a forte velocità o che lavorino in ambienti in cui sono richiesti livelli di rumorosità molto bassi.
In questi casi affermare che è sufficiente rettificare gli ingranaggi per risolvere il problema è sbagliato.
Infatti, le semplici modifiche relative al profilo (spoglia di testa e di piede) e dell’elica (bombatura) si avvicinano solamente alle condizioni ottimali.
Se si pensa che le forze che agiscono su ogni singolo dente cambiano durante la rotazione, in intensità, direzione e punto di applicazione, si può capire che la flessione di questo dente sarà continuamente variabile.
In teoria in ogni sezione normale del dente si dovrebbe avere una diversa correzione di profilo. Questo introduce il concetto di modifica topologica della superficie del dente.
Considerazioni sullo stato delle superfici
Agli effetti della rumorosità, una certa importanza hanno le tracce lasciate dall’operazione di rettifica, cioè la loro profondità e la loro direzione. In genere, la rettifica fornisce una rugosità di Ra = 0,4 – 0,6 micrometri.
Si è già detto che durante l’accoppiamento, all’infuori del diametro primitivo, si hanno degli strisciamenti tra le superfici dei denti della ruota e della controruota.
Questi strisciamenti, in direzione radiale, hanno senso opposto a seconda che il contatto sia sopra o sotto il diametro primitivo e sono tanto più intensi quanto maggiore è la distanza dal primitivo.
Dove c’è strisciamento c’è una forza d’attrito e questa forza, quando inverte il senso, può innescare vibrazioni.
Le tracce lasciate dalla rettifica di forma, attraversano tendenzialmente in modo longitudinale il dente e sono quindi all’incirca ortogonali alla direzione di scorrimento dei profili. Cioè è la condizione peggiore agli effetti dell’attrito.
In alcune circostanze, dove la rugosità è più alta e dove le pressioni sono forti, si può arrivare alla rottura del film di lubrificante con conseguenze gravi anche per la vita dell’ingranaggio.
Sotto questo punto di vista è preferibile rettificare con il metodo per generazione, specie se è con mola a vite.
È per questi motivi che attualmente anche nelle produzioni di grande serie, si preferisce finire i denti con un’operazione di rettifica, anche se più costosa della rasatura.
Le moderne rettificatrici oggi sono in grado sia di eseguire le modifiche topologiche delle superfici attive dei denti e anche di variare la disposizione delle tracce di rettifica (modifica della texture).