Grazie all’utilizzo di mole combinate con larghezza fino a 200 mm per applicazioni di rettifica di superfinitura o di polishing, Kapp Niles è in grado di lavorare in modo efficiente ingranaggi di grandi dimensioni, impiegati su veicoli commerciali pesanti.
Dopo le automobili, anche i veicoli commerciali pesanti stanno diventando elettrici. La trasformazione della tecnologia di trasmissione richiede ingranaggi con diametri maggiori, moduli più grandi e rugosità più fini. È proprio questa la sfida che gli utilizzatori (costruttori di ingranaggi) e i fornitori di attrezzature (costruttori di macchine) stanno affrontando allo stesso modo.
Il mercato dei veicoli commerciali pesanti
Il mercato dei veicoli commerciali pesanti sta subendo una trasformazione. Questo ha un impatto anche sulle trasmissioni. A differenza delle autovetture, le emissioni sonore giocano solo un ruolo minore, ma ci sono molte altre sfide, come i frequenti cambi di carico nella trasmissione dovuti all’utilizzo dell’energia di frenata per il recupero. Di conseguenza, la trasmissione è sottoposta a carichi diversi rispetto al passato e deve essere realizzata in modo molto più preciso. Allo stesso tempo, l’efficienza della trasmissione è una priorità assoluta: basse perdite, cioè basso attrito, per ridurre al minimo il consumo di energia e massimizzare l’autonomia del veicolo.
Macchine per specialisti dell’heavy-duty
Le rettificatrici di Kapp Niles sono in uso dagli anni ’80 nello stabilimento di trasmissione di Rastatt, che fa parte dello stabilimento Mercedes-Benz di Gaggenau. Nei prossimi anni, i processi qui saranno caratterizzati da un funzionamento misto, cioè la varianza aumenterà. Da un lato si continuerà a produrre cambi a combustione, dall’altro si assisterà a una trasformazione verso nuove tecnologie di azionamento, come i veicoli elettrici.
Per la lavorazione di precisione fine viene utilizzata un’intera serie di rettificatrici per ingranaggi Kapp Niles. Per gli ingranaggi di grandi dimensioni è stata acquistata una nuova macchina KNG 350 flex. Grazie al concetto di macchina compatto e ottimizzato, è adatta sia per un impiego nei settori dei prototipi fino alla produzione di grandi serie. Con l’opzione di ampliamento della zona di lavoro e all’utilizzo di mole combinate con larghezza fino a 200 mm per applicazioni di rettifica di superfinitura o di polishing, è possibile lavorare in modo efficiente ingranaggi di grandi dimensioni per la mobilità elettrica.
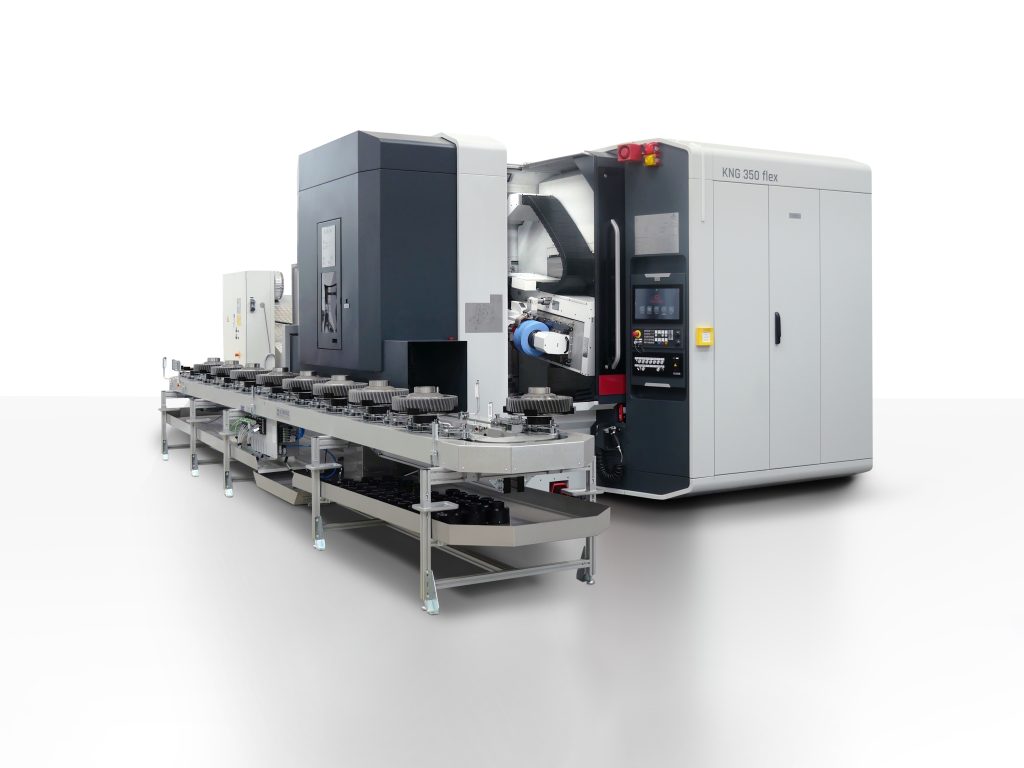
Le macchine KX 260 TWIN e KX 260 TWIN HS con utensili piccoli sono utilizzate per gli alberi degli ingranaggi. Consentono la rettifica a generazione in continuo con utensili ravvivabili e non. Il concetto prevede due mandrini portapezzo identici disposti uno di fronte all’altro su una tavola rotante. Parallelamente alla lavorazione di un pezzo, avviene il carico e lo scarico, compreso l’allineamento di un altro pezzo sul secondo mandrino.
Processi combinati: rugosità ai limiti delle possibilità tecniche
Il polishing si è sempre più affermato negli ultimi anni. Nei veicoli commerciali, l’attenzione si concentra su una maggiore capacità di carico laterale degli ingranaggi e sul miglioramento dell’efficienza. Sulle macchine Kapp Niles vengono utilizzati speciali mole a vite con due aree, una per la rettifica convenzionale e una per la rettifica di polishing. Ciò consente di produrre ingranaggi con rugosità fino a Rz < 1 μm in un’unica presa. Ormai il polishing è stato implememtato su tutta la linea delle trasmissioni elettriche. Negli ultimi anni, insieme a Kapp Niles, il processo è stato sviluppato e approfondito.
La sfida più grande è mantenere stabile la qualità della rugosità nella produzione in serie. Esistono parametri fissi per la rettifica con utensili in corindone a legame ceramico. Tuttavia, la sezione per la rettifica di polishing è a legame polimerico e quindi deformabile. Ciò la rende più sensibile in termini di tecnologia di processo e richiede una maggiore attività di misurazione. Inoltre, i due segmenti richiedono cambi utensili più frequenti. Nel complesso, il processo è molto più veloce di un processo separato.
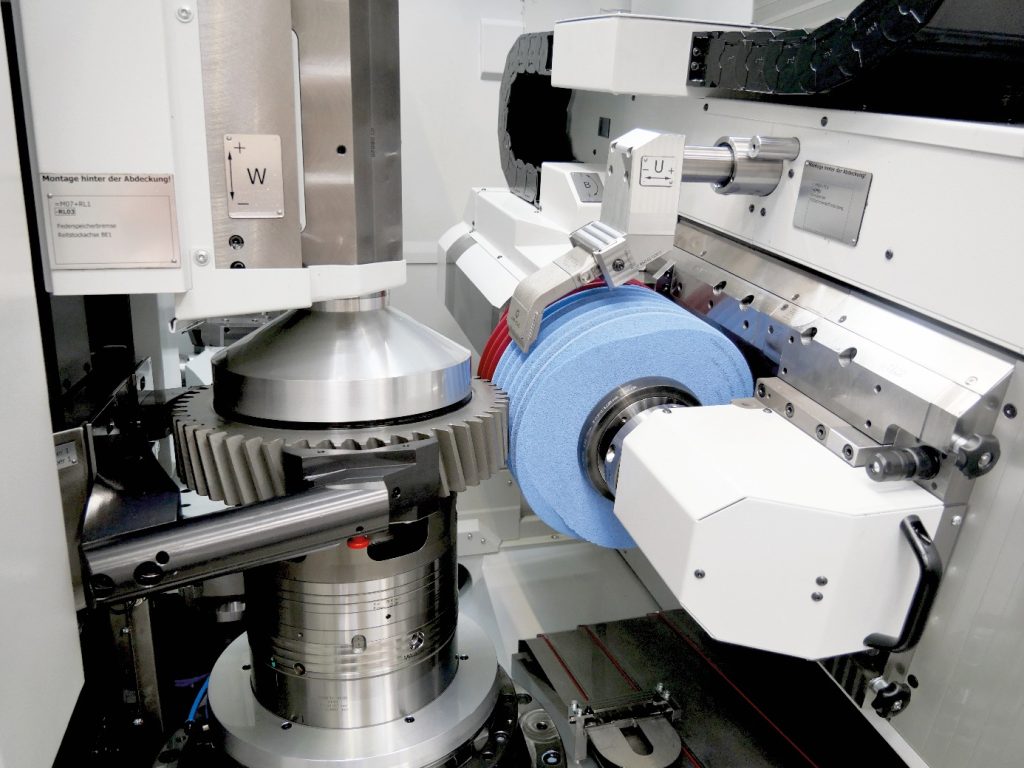
Una questione non da poco: i componenti più grandi
La possibilità di implementare l’area di lavoro della KNG 350 flex è già stata menzionata. Tuttavia, questo richiede molto di più del semplice potenziamento della tecnologia esistente. Markus Reißenweber, responsabile vendite Europa e America di Kapp Niles, ricorda che: «Quando è stato sviluppato il progetto per la KNG 350 flex, l’attenzione era già rivolta ai componenti di grandi dimensioni per le trasmissioni dei camion, ma all’epoca si trattava di componenti con un diametro di circa 300 mm. Con la trasmissione elettrica, sono improvvisamente comparsi ingranaggi fino a quasi 400 mm di diametro. Ciò influisce sia sullo spazio di lavoro che sull’area di movimentazione». Con un peso di circa 30 kg, i componenti hanno un peso maggiore e un modulo più grande. Si tratta di una nuova dimensione per Daimler Truck e per Kapp Niles. È necessario installare nuovi processi, come la rettifica di polishing, e prepararli per la produzione in serie, in modo che possano funzionare senza problemi su tre turni. È stato necessario un lavoro di sviluppo congiunto per poter produrre in serie la qualità richiesta a disegno.
Successo con partner forti
Le sfide non sono certo mancate ma le macchine funzionano e i processi sono stabili. La facilità di impostazione delle macchine Kapp Niles gioca un ruolo particolarmente importante. Il set up delle macchine cambia quotidianamente perché la produzione di cambi per i camion non è un classico processo di produzione ad alto volume. Il concetto macchina supporta lavoratori e operatori in molti modi.