Attualmente la produzione additiva (o Additive Manufacturing, AM) è una delle principali novità nel campo delle tecnologie di produzione manufatturiera di stampo industriale. I componenti vengono realizzati in modo additivo, ovvero la loro costruzione avviene attraverso l’aggiunta di materiale strato su strato fino al raggiungimento della forma finale. Questa è la principale differenza rispetto alle tecnologie convenzionali di produzione, che operano principalmente per asportazione di materiale partendo da un massello iniziale fino all’ottenimento della forma e dimensione finale. Queste tecnologie di AM hanno avuto la loro origine a partire dalla prototipazione rapida ma negli ultimi anni si sono sviluppate a livello industriale con lo scopo di produrre componenti. Tra le tecnologie di AM diffuse a livello industriale, quella maggiormente diffusa è la fusione selettiva mediante fascio laser a letto di polvere (Selective Laser Beam Melting – SLBM). In questo articolo si riporterà inizialmente una breve descrizione del sistema SLBM con riferimento al suo principio di funzionamento, saranno poi riportati degli accenni relativi alla progettazione dei componenti ed infine saranno presentati alcuni esempi applicativi, realizzati mediante questa tecnologia.
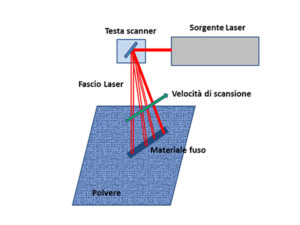
Produzione additiva mediante fusione laser selettiva: descrizione del sistema
La tecnologia SLBM è attualmente la tecnologia additiva maggiormente impiegata a livello industriale per la realizzazione di componenti in materiale metallico; il componente viene costruito in modo tridimensionale attraverso la sovrapposizione di successivi strati di polvere, che viene portata a fusione mediante una sorgente di calore ad alta densità di energia (in questo caso, un fascio laser). Per questo motivo, si parla di tecnologia che opera su letto di polvere per differenziarla rispetto alla deposizione laser diretta (o laser cladding), in cui la polvere viene depositata in modo locale attraverso un ugello coassiale al fascio laser. Nella tecnologia SLBM il fascio laser viene messo in movimento su uno strato di polvere in modo selettivo. Il percorso del fascio laser viene predefinito da un software CAD/CAM 3D, che genera un file rappresentativo della geometria del componente da realizzare; in particolare, tale file contiene il disegno 3D del componente, suddiviso in slice che rappresentano i singoli strati di polvere che verranno prodotti durante il processo additivo. La polvere viene di conseguenza portata a fusione solamente in alcune zone strategiche, indicate dal file CAD/CAM, in cui si deve ottenere del materiale compatto a seguito della sua fusione per la costruzione del componente tridimensionale. Lo schema, che mostra il principio di funzionamento del sistema SLBM, è illustrato in Figura 1-2. La sorgente laser, utilizzata nei sistemi SLBM presenti attualmente in commercio, è una sorgente in fibra attiva ad Itterbio con potenze che variano tra 200 W fino ad un massino di 1 kW. Una volta generato dalla sorgente, il fascio laser viene trasportato fino alla zona immediatamente al di sopra della camera di lavoro, dove è posizionato un sistema galvanometrico (vedi Figura 1). Tale sistema viene utilizzato sia per la focalizzazione del fascio laser (su dimensioni da 50 mm e 200 mm) che per muoverlo con elevate velocità di scansione (da 1 m/s fino a circa 10 m/s ).
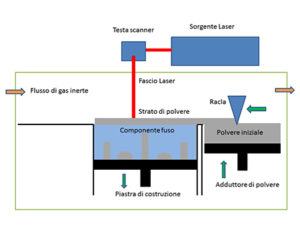
Dopo la sua focalizzazione, il fascio laser passa attraverso una finestra di protezione, che ha il compito di sigillare la zona di trasporto ottico dalla camera di lavoro, in cui avviene il processo di fusione della polvere. La camera di lavoro è la zona in cui avviene il processo di fusione della polvere sotto l’azione di un’atmosfera inerte. La configurazione classica del sistema prevede la presenza di due piastre, la prima di costruzione e la seconda per l’adduzione della polvere: le due piastre si muovono lungo l’asse verticale in senso opposto una all’altra, come se fossero parte di un unico bilanciere, come mostrato in Figura 2. La polvere viene trasferita da una racla dalla piastra di adduzione a quella di costruzione per la costruzione del singolo strato. Successivamente a questa fase, il fascio laser viene messo in movimento sullo strato di polvere in modo da poter fondere in modo selettivo solo la zona in cui è previsto l’ottenimento di materiale denso, come schematizzato in Figura 1. Una volta terminata la fusione sul singolo strato di polvere, la piastra di costruzione viene abbassata di una distanza pari allo strato di polvere da depositare e le precedenti fasi del processo vengono ripetute per un numero di volte pari al numero di slice in cui il modello 3D del componente è stato suddiviso.
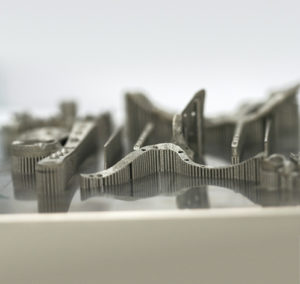
con tecnologia SLBM, supportati con elementi
che garantiscano il sostegno adeguato
alla struttura prodotta.
Le zone colorate in grigio di Figura 2 rappresentano la polvere allo stato iniziale mentre quelle in colore azzurro indicano la polvere che è stata colpita dalla radiazione laser e che è stata quindi portata a fusione, ottenendo materiale compatto. Secondo questa modalità di costruzione, il componente tridimensionale viene realizzato, vincolato sulla piastra di costruzione ed sostenuto da supporti in corrispondenza di superfici inclinate, come illustrato in Figura 3. Al termine del processo, i componenti devono essere separati dalla piastra di costruzione e dai supporti; inoltre, essi devono essere sottoposti anche a trattamenti termici di distensione per eliminare le tensioni residue, che potrebbero compromettere la loro integrità strutturale. Infine, nella maggior parte dei casi sono previste operazioni di finitura superficiale, in quanto la rugosità ottenibile con il processo SLBM (4-6 mm) è raramente entro le specifiche del prodotto.
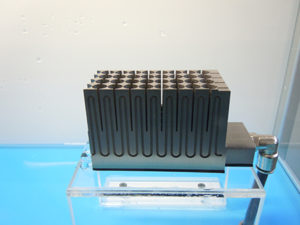
Progettazione di componenti
L’aspetto di maggiore importanza è quella riguardante la riprogettazione del componente in funzione della specifica tecnologia di produzione: date le peculiari caratteristiche legate alla deposizione di materiale strato su strato, il componente deve essere riprogettato in modo tale da sfruttare al massimo i vantaggi della tecnologia additiva. Non ha alcun senso pensare di realizzare in modo additivo dei componenti progettati per essere realizzati mediante processi di casting tradizionale, come ad esempio la pressofusione: al contrario, la geometria del nuovo componente dovrà essere ottimizzata per liberarsi dai vincoli tecnologici del processo di fonderia convenzionale. Per questo motivo, esistono dei software commerciali, come ad esempio Inspire di Solid Think, che consentono di effettuare ottimizzazioni topologiche con diversi scopi, quali ad esempio: il miglioramento del comportamento termico e dinamico, la riduzione del peso, l’aumento della resistenza meccanica e l’integrazione di funzioni differenti. Altri aspetti da considerare legati alla fase di progettazione di componenti riguardano le caratteristiche meccaniche del componente finale e la possibilità di soddisfare le tolleranze richieste da progetto. Le caratteristiche meccaniche del materiale, prodotto con tecnologia SLBM, sono diverse se valutate nel piano di costruzione oppure lungo l’asse verticale di costruzione: questo rende il materiale prodotto anisotropo, aspetto dunque da considerare nella fase di progettazione. Inoltre, il materiale solidificato proviene da pozze fuse di piccole dimensioni e raffreddate molto velocemente, quindi la microstruttura che si genera è generalmente più fine rispetto a quella del corrispondente materiale prodotto per mezzo di un processo di fonderia convenzionale. Questo comporta che il materiale sarà meno duttile, ovvero sarà caratterizzato da un livello di sollecitazioni ammissibili maggiori nella curva sforzo-deformazione e con deformazioni inferiori a rottura. L’altro aspetto da considerare riguarda le tolleranze, intese come finitura superficiale ed il livello di precisione dimensionale: sono infatti richiesti processi di finitura superficiale che a seguito del processo SLBM. Questi influenzano i sovrametalli da utilizzare in funzione delle specifiche di prodotto. Il sovrametallo dipende principalmente sia dalla contrazione volumetrica da stato liquido a quello solido sia dal livello di precisione del processo di fusione laser, che non è elevato (±0.05 mm). Infine, come accennato precedentemente, è necessario prevedere l’utilizzo di supporti, che hanno la funzione di sostenere la struttura del componente durante la fase di produzione (vedi Figura 3). Tali supporti, anche se sembrano essere dei “semplici” elementi aggiuntivi, giocano un ruolo fondamentale nella corretta stampa del prodotto e devono soddisfare una serie di requisiti:
(i) sostegno meccanico della polvere fusa nel caso di angoli inclinati tra 0° e 45° rispetto alla piastra di costruzione;
(ii) una facile rimozione dei supporti al termine del processo produttivo, senza lasciare tracce evidenti della loro presenza su superfici di accoppiamento oppure estetiche;
(iii) modifica del fronte termico durante la lavorazione, in quanto i supporti sono dei pozzi di calore che asportano più velocemente il calore nel corso del raffreddamento della singola pozza fusa rispetto alla polvere non fusa che circonda il pezzo.
Nella maggior parte dei casi, non esistono delle formule empiriche che consentano di progettazione i supporti, come succede nei processi di fonderia convenzionali, ma è l’esperienza tecnica del progettista e dell’operatore che forniscono questo valore aggiunto.
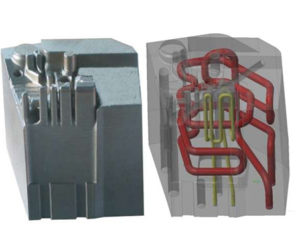
Esempi di componenti realizzati
In questo paragrafo si riporteranno degli esempi rappresentativi, principalmente dedicati al settore degli stampi ma non solo, che riassumono i concetti precedentemente descritti.
In generale, i principali campi di applicazione dei componenti prodotti per tecnologia SLBM spaziano dal campo biomedicale a quello aerospaziale, dalla gioielleria al racing fino a quello degli stampi, tutti campi in cui i lotti di produzione sono di dimensioni medio-piccole e la possibilità di personalizzazione del prodotto diventa un aspetto di notevole importanza.
A prescindere dal campo di applicazione, questi componenti rispecchiano in modo intrinseco le principali caratteristiche della tecnologia di produzione additiva; infatti, le forme, che possono essere ottenute mediante tecnologie additive oppure mediante quelle convenzionali di tipo sottrattivo, possono essere ben riconoscibili per l’elevato gradi di complessità presente in un unico prodotto, senza prevedere la fase di assemblaggi di sottoparti.
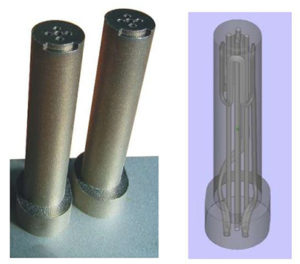
La costruzione del componente “strato su strato” consente di aumentare i gradi di libertà con cui il pezzo stesso può essere progettato e successivamente prodotto. Di conseguenza, geometrie complesse, come quelle caratterizzate dalla presenza di strutture interne come canali integrati per il passaggio di un fluido oppure l’alternanza di strutture a densità relativa variabile, possono essere realizzabili esclusivamente attraverso l’AM in un unico pezzo.
In Figura 4 si mostra un esempio di stampo realizzato con un sistema interno di canali di raffreddamento per garantirne l’aumento della vita a fatica termica. Questi circuiti di raffreddamento sono difficili da essere realizzati e quindi costosi, se non impossibili, se prodotti mediante tecnologie convenzionali di lavorazione. In questo caso specifico, la produzione additiva ha consentito di “annegare” nel volume del componente delle zone vuote che consentono di valorizzare le prestazioni finali del prodotto. Il vincolo principale, che deve essere soddisfatto in fase realizzativa di strutture analoghe, è quello di prevedere delle zone di passaggio per garantire la fuoriuscita della polvere non reagita con il fascio laser. Il livello di complessità raggiungibile può essere davvero molto elevato: due esempi rappresentativi di elevato grado di complessità sono quelli mostrati in Figura 5-6. Si riporta per entrambe le figure sulla sinistra la fotografia del componente prodotto e sulla destra una sua rappresentazione grafica tridimensionale, che consente di mettere in risalto i dettagli interni realizzati. Il componente di Figura 5 è un inserto, caratterizzato da due circuiti di raffreddamento indipendenti uno dall’altro. La loro funzionalità è quella di poter raffreddare zone diverse del componente con gradienti termici differenti, dati due diametri diversi delle condutture. Il componente di Figura 6 è, invece, un elemento cilindrico che presenta un sistema di raffreddamento posizionato lungo il suo asse di simmetria: anche in questo caso, la realizzazione del sistema di raffreddamento integrato in un unico componente è possibile solo considerando tecnologie additive. Il settore degli stampi è uno di quelli che può trarre maggiori benefici dall’utilizzo della tecnologia SLBM per la realizzazione di componenti di piccole-medie dimensioni, viste le limitazioni sui volumi delle camere di lavoro disponibili in commercio, con geometrie molto complesse e con funzioni integrate, senza la necessità di un successivo assemblaggio di pezzi prodotti separatamente.
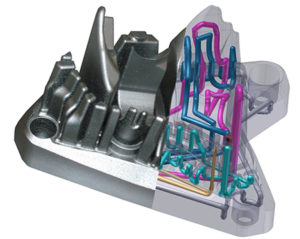
La Figura 7 mostra la parte esterna (lato di sinistra) e la parte interna (lato di destra) di uno stampo prodotto con SLBM: la complessità sia delle superfici esterne che di quelle interne danno l’idea delle potenzialità delle tecnologie additive nella realizzazione di componenti innovativi, che precedentemente non potevano essere realizzati a livello industriale. La conseguenza primaria è la rottura degli schemi classici in fase di progettazione; infatti, le forme che il componente può assumere possono essere riviste profondamente. Questa flessibilità in fase di costruzione di forme complesse apre alla possibilità di realizzare dettagli con forme difficili da realizzare, come ad esempio sottosquadri, cavità con rapporti di forma elevati, superfici curve associate a matematiche complesse.
In Figura 8a si mostra un ultimo esempio di stampo con circuito di raffreddamento interno, avente una struttura definita “ad anello”; Figura 8b mostra invece la riproduzione del medesimo componente, realizzata in materiale plastico semitrasparente, che consente di mettere in evidenza le zone interne vuote.
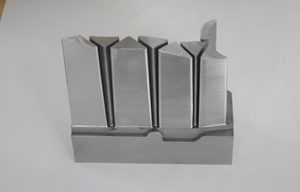
prodotto in metallo
Conclusioni
I principali vantaggi della tecnologia SLBM sono la possibilità di produrre componenti metallici “near net shape” , ovvero con geometria/dimensioni prossime a quella del componente finale mediante un’unica tecnologia di lavorazione.
Grazie alla modalità di costruzione “strato su strato”, è possibile produrre geometrie molto complesse, si garantisce una forte personalizzazione dei componenti senza interventi costosi sul step up del sistema ed un’elevata percentuale di recupero del materiale non utilizzato direttamente nel processo di fusione. Tramite questa tecnologia è possibile realizzare dei componenti sia in materiale denso (materiale pieno con densità apparente quasi del 100%) oppure sia in materiale poroso tramite strutture trabecoidali, anche se ancora poco diffusi: questo possibilità di scelta si traduce in un grado di libertà aggiuntivo sia a livello progettuale che dal punto di vista produttivo nell’ottica della realizzazione del componente.
In questo articolo sono stati riportati alcuni esempi esplicativi delle potenzialità della tecnologia SLBM nel campo della produzione industriale di componenti, mettendo in evidenza come il livello di dettaglio ottenibili sia attualmente molto elevato. Questo evidentemente apre a nuove soluzioni tecniche e tecnologiche in tutti i campi di applicazioni possibili in cui un componente metallico è presente.
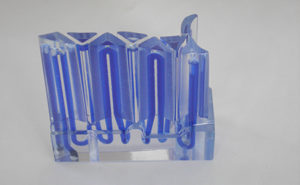
plastico
E’ indubbio come una oculata riprogettazione dei componenti (forme e dimensioni) nell’ottica della loro realizzazione mediante tecnologie additive sia strategica per garantire il miglior compromesso tra riduzione del peso, resistenza meccanica e prestazioni del componente stesso, tutto questo grazie ai gradi di libertà con cui è possibile ottenere forme complesse. A riguardo di questo tema, esistono infatti in commercio dei software specifici in grado di approcciarsi al mondo della produzione additiva, spaziando dal design del prodotto ottimizzandone la geometria in funzione dei carichi richiesti dall’applicazione specifica.
Ringraziamenti
Gli autori desiderano ringraziare Renishaw s.r.l. Italia per la condivisione delle immagini dei casi applicativi.
Articolo di Carlo Alberto Biffi, Ausonio Tuissi*
Consiglio Nazionale delle Ricerche, Istituto per l’Energetica e le Interfasi, Unità di Lecco, Corso Promessi Sposi, 29 Lecco (Italia).
In collaborazione con AITEM- Promozione L@ser