Le tecniche di lavorazione degli ingranaggi sono in rapida evoluzione. Macchine, utensili, software e tutto ciò che è presente in una linea di produzione ha subito (e sta subendo) profonde trasformazioni.
Il mondo gira con gli ingranaggi! È quello che mi dicevano quando ero giovane per invogliarmi a dedicarmi con passione a questo settore della meccanica. In effetti, una moltitudine di dispositivi che ci circonda nella vita quotidiana si muovono con l’ausilio degli ingranaggi. Più di un miliardo di ingranaggi sono prodotti ogni anno nel mondo e quindi è stato inevitabile che molte energie si siano spese per perfezionare la tecnologia della loro costruzione.
Gli ingranaggi devono essere sempre più silenziosi, ma anche sempre più precisi e questa necessità si è fatta particolarmente stringente oggi con la progressiva introduzione sul mercato dei motori elettrici in sostituzione di quelli a scoppio. La maggiore velocità di rotazione e il minore mascheramento del rumore da parte del motore richiede più cura nella finitura degli ingranaggi allo scopo di contenere la rumorosità percepita. Questa richiesta di silenziosità non è limitata al settore dell’automobile, ma si estende anche ad altri dispositivi largamente usati, quali possono essere per esempio i riduttori di velocità; dai piccoli ai grandi gruppi di riduzione, da quelli con ingranaggi cilindrici a quelli con ingranaggi conici, sino a quelli con vite senza fine, si sta assistendo a un progressivo aumento della precisione necessaria. Questo non solo per una riduzione della rumorosità ma anche per aumentare il rendimento delle trasmissioni e ridurre il costo della loro manutenzione.
Basta solo un esempio per dimostrare quanto sia importante questo ultimo aspetto, ed è quello legato alle turbine per la generazione di energia con l’eolico. Quanto costa la manutenzione ordinaria o straordinaria di un gruppo installato offshore?
La rumorosità di una trasmissione è indubbiamente legata alla precisione con cui sono costruiti i denti degli ingranaggi e i parametri interessati sono la divisione, il profilo e l’elica. Però bisogna mettere subito in chiaro che anche una coppia di ingranaggi perfettamente costruiti, cioè privi di errori, può risultare rumorosa quando è in funzione e cioè dipende dalla precisione con cui è costruita la scatola cambio. Errori di allineamento dei supporti degli alberi, giochi eccessivi delle sedi o cuscinetti difettosi possono vanificare tutte le attenzioni che si pongono nell’esecuzione delle dentature.
Il tecnico metodista ha a disposizione diversi metodi di finitura degli ingranaggi e la scelta non è sempre molto semplice, in quanto devono essere valutati attentamente molti aspetti del problema.
In primo luogo, bisogna prendere in esame la tipologia dell’ingranaggio da eseguire, nel senso di giudicare se è un ingranaggio che deve essere trattato termicamente o no, se è un ingranaggio che lavora ad alte velocità ed è fortemente sollecitato, se ha una geometria complessa. Per esempio, una dentatura che abbia un profilo complesso che si discosti molto dall’evolvente teorico oppure che abbia bisogno di un raccordo perfetto a fondo dente non potrà essere finita con alcuni metodi.
In secondo luogo, è importante conoscere quanti ingranaggi bisogna produrre, perché un conto è lavorare piccole serie e un altro è impostare una lavorazione di grande serie. Qui subentrano altre considerazioni che coinvolgono il livello di investimenti possibili e il layout delle linee di produzione. Fatte queste considerazioni, il tecnico deve capire quale è lo stato dell’arte delle varie macchine da scegliere e se si parla appunto di finitura degli ingranaggi le opzioni sono numerose perché è un settore che negli ultimi anni è stato oggetto di un grande sviluppo.
Esaminiamo ora quali sono le principali caratteristiche dei più diffusi metodi di finitura delle dentature cilindriche, fornendo qualche dato utile al metodista per orientarlo nella scelta tra le varie opzioni.
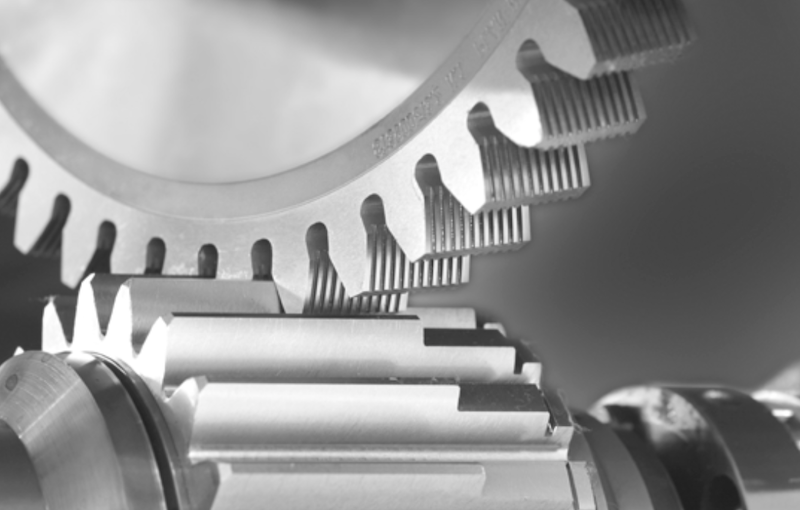
Rasatura
È sicuramente il metodo di finitura degli ingranaggi ancora più diffuso, anche se in molte linee di produzione è stato sostituito da altri sistemi più evoluti.
Il limite della rasatura è in primo luogo il fatto che consiste in un’operazione che deve essere eseguita sul tenero e quindi il pezzo rasato subirà inevitabilmente delle deformazioni durante il trattamento termico.
Nelle produzioni di grandi serie, prima dell’avviamento, si eseguono dei test per stabilire l’entità delle deformazioni e la loro caratteristica. Con questi dati è possibile progettare i coltelli rasatori con profili ed eliche che precorreggono le deformazioni che si verificheranno con il trattamento termico.
Un altro limite è dovuto al fatto che non è possibile finire bene il fondo dente, e quindi questa operazione non è consigliata nei casi in cui l’ingranaggio deve trasmettere coppie elevate. Inoltre, è un’operazione che non è indicata per basse produzioni, perché l’utensile ha un certo costo e richiede macchine specifiche per la sua riaffilatura.
Si possono rasare dentature fino a modulo 10 mm con precisioni che possono arrivare anche a classe DIN 4-5 ma, come si è specificato solo prima del trattamento termico. Tra i vantaggi si può citare che il ciclo di rasatura è molto breve se si riesce a lavorare con il metodo plongèe e che con le moderne macchine di rettifica del rasatore si possono ottenere profili relativamente complessi.
In definitiva, si può concludere che questo metodo è economicamente conveniente se si accettano le limitazioni di cui si è accennato.